Measurement Sensors
Measuring Eccentricity
When looking for the best way to measure eccentricity, there are several important factors to consider, including the type of measurement system and the installation environment. Selecting equipment that doesn't adequately meet your needs can lead to insufficient precision and increased man-hours during production. This site is designed to help users determine the best way to measure eccentricity with confidence.
Get detailed information on our products by downloading our catalog.
View Catalog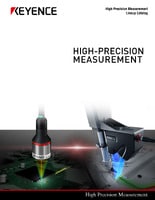
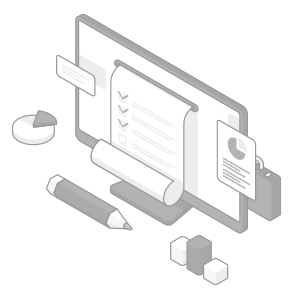
What Units Are Used for Eccentricity?
When measuring eccentricity of components in manufacturing, it is typical to use standard linear measurement values, such as inch, thou, millimeter, or micron.
Eccentricity Measurement With a Reflective-Type Sensor
Measuring eccentricity using a reflective-type sensor is a process that involves monitoring the deviation of the shape of an object from an ideal circle or rotation by determining how far the object deviates from its true center. Regardless of the type of sensor you use, the measurment principle remains the same: the scanner will take measurements of various points along the rotation of the object, measure the distance between the surface and the sensor, and build a profile of the surface.
This profile is later analyzed to determine the object's maximum and minimum radii, which indicates eccentricity. Reflective-type sensors offer high precision, which is crucial for applications that require tight tolerances, including aerospace and automotive industries, as well as precision manufacturing. However, not all reflective-type sensors work for all types of surfaces.
The laser is pointed at the apex of the circle to capture fluctuations in distance through high-speed sampling.
- Measurement must be performed at a sampling rate of at least ten times the rotation speed.
- Errors increase as the shaft diameter decreases because the apex position shifts to the left or right due to eccentricity.
Eccentricity measurement of high-precision rollers
Confocal Displacement Sensor CL-3000 series
Micro-head Spectral-interference Laser Displacement Meter SI-F series
Eccentricity Measurement With a Thrubeam-Type Sensor
Thrubeam sensors emit light from a transmitter to a receiver and gather data by measuring any interruptions or shifts in the light due to the presence of an object. Fluctuations in peak-to-peak data can be used to determine eccentricity.
Unlike reflective-type sensors, thrubeam sensors perform stable measurements in environments with heavy vibration and/or product tilt.
Fluctuations in the edge positions of the roller are captured through high-speed sampling.
- The peak-to-peak value of the run-out is found using a peak-to-peak hold or a similar function.
- Measurement must be performed at a sampling rate of at least ten times the rotation speed.
Eccentricity measurement of motor shafts
High-speed optical micrometer LS-9000 series
Measurement of Eccentricity at Multiple Points With Thrubeam Model
Measuring eccentricity using thru-beam type sensors involves passing an object between a measuring system's light emitter and light receiver. The object is typically rotated around its longitudinal axis (which is offset from the geometrical axis) perpendicularly to the light beam.
Depending on the type of sensor you're using to measure eccentricity, the system will either measure the object's shadow, its silhouette, or edge detection in a single line of sight. As the object rotates, the silhouette (or the edge) changes in the receiver's field of vision. These changes are recorded and compiled into a surface profile. The eccentricity measurements are derived from the difference between the maximum and minimum radii detected during rotation.
The eccentricity is measured by finding fluctuations at multiple specified point positions using the image obtained by the 2D optical projection method.
- The run-out of V grooves and protrusions in the circumference can be measured.
- The run-out of a point at a predetermined distance from the end can be measured.
Eccentricity measurement of sponge rollers
Telecentric Measurement System TM-X5000 series
What is Eccentricity?
In the context of engineering, component and parts manufacturing, and quality control, eccentricity refers to a deviation from the circular path of rotation. Since the center of rotation is offset from the geometrical center, it's implied that eccentricity is the measure of the non-concentricity of an object's shape or its rotation. The measurement of eccentricity is the distance between the object's theoretical center and the center determined by its physical properties.
In metrology, particularly in quality control, measuring eccentricity is derived from the difference between the largest and the smallest radii measured from the rotational axis to the object's surface. Measuring eccentricity is crucial for all cylindrical parts and components, whether they're eccentric by design or not—if the observed object isn't up to specs, it could cause damage or inefficiency inside the systems they're installed in.
What is Needed to Measure Eccentricity?
Just like with everything else in metrology, precise measurements require precise equipment. However, measuring eccentricity also requires a combination of procedural methodology, depending on the type of sensor and the approach to measurement.
For example, 2D triangulation sensors are capable of determining the distance between the sensor and the surface, which can be used to derive the maximum and minimum radii and quantify eccentricity, and the same applies to multi-color confocal sensors.
Thrubeam-type sensors, while working on an entirely different principle, would still perform the same measurements, but instead of reflecting the light off of an object, they would use the object's shadow or silhouette to quantify eccentricity.
What are Easy Ways to Measure Eccentricity?
Measuring eccentricity in engineering and parts and component manufacturing requires specific and precise measurements. These can be done by hand with relative precision. However, the process is rather tedious, time-consuming, and susceptible to errors and surface damage.
On the other hand, automating the process using non-contact, highly precise measurement systems eliminates nearly all aforementioned concerns, saves time, eliminates error, and doesn't come into contact with the measuring surface.