Measurement Sensors
3D Inspection and Measurement
While 3D inspection and 3D measurement both rely on capturing and processing dimensional data, their primary focus and applications across various industries differ. The main difference is simply how 3D data is used.
A multitude of inspections and measurements (like volume, warpage, and tilt) become possible by acquiring a 3D image. That said, a target's size, material, and how it will be presented play key roles in obtaining good data. Below are a few of the options available, and you can request a free consultation with a 3D measurement expert if you have any questions.
Get detailed information on our products by downloading our catalog.
View Catalog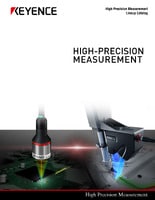
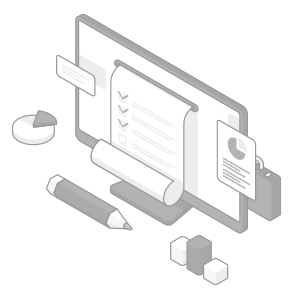
What is 3D Inspection?
The primary focus of 3D inspection is to ensure that the products conform to pre-set specifications. 3D inspection systems rely on an array of sensors that assess whether an object meets the predefined criteria or standards. While they conduct measurements, these measurements are used as comparisons against a reference model to determine standard compliance.
3D part inspection is used to check finished products for defects, warpage, or deviations from the intended design, typically throughout the manufacturing process, ensuring that products remain within tolerance.
What is 3D Measurement?
3D measurement systems, on the other hand, focus primarily on precision and accuracy, as their sensors are configured to capture highly accurate and precise measurements of various objects. They provide detailed dimensional data, often including exact coordinates, distances, angles, and geometries.
This data collection ensures that the end product meets strict part specifications or more accurate data capture in reverse engineering applications, in which precision and accuracy are essential.
3D Inspection Sensors
3D inspection sensors collect data and can be used like 3D measurement sensors. A big difference between the two is that 3D inspection sensors can also verify part conformity and detect defects. This is accomplished by comparing the captured data against pre-defined standards. Since they’re mostly integrated into fast-moving assembly lines, 3D inspection sensors prioritize speed and efficiency in detecting pass/fail conditions.
3D Measurement Sensors
3D measurement sensors are calibrated to capture highly accurate and precise dimensional measurement data. These sensors are typically used to verify exact part dimensions, and the data collected by 3D measurement sensors is often far more detailed than data provided by 3D inspection sensors.
3D Inspection Applications
3D inspection scanners are mostly used in applications such as quality control in assembly lines, where parts must pass simple pass/fail checks. These checks often require several different measurements for comparative purposes. As a result, the complexity of the measured data isn’t as vast.
3D inspection applications include assembly inspection, surface defect detection, body and chassis inspection, welding quality assessment, interior fitting verification, PCB and electronics manufacturing, and many others.
3D Measurement Applications
Since they include a wide range of methods, such as laser scanning, structured light capture, photogrammetry, and CMMs, 3D measurement systems are suitable for a wide range of applications across various industries.
This includes precise measurement for in-depth quality control, accurate dimensioning of molds, dies, and fixtures, creating and verifying various measurements in prototyping applications, and even surgical planning and object digitization.
Coating Inspection of Sealing Material
2D Profilers can measure the width, height, and volume of sealant beads inline, regardless of surface finish or color.
2D/3D Laser Profiler LJ-X8000 series
Connector Coplanarity Measurement
Unlike triangulation sensors, interferometers can measure small parts in confined spaces without blind spots or unstable data.
3D Interference Measurement Sensor WI-5000 series
Inspection for Electrode Terminal Burrs After Slitting
Detect burrs arising on terminals after electrode slitting. With ultra-high-resolution 3200 points/profile measurement, the LJ-X8000 Series produces stable detection even for minute burrs.
2D/3D Laser Profiler LJ-X8000 series
Weld Shape Inspection
Profile measurement can be continuously performed on captured 3D shapes. This allows pass/fail criteria to be applied to maximum and minimum values over an area or time, making it possible to catch small defects in continuous processes.
2D/3D Laser Profiler LJ-X8000 series
Sheet Thickness, Width, and Edge Profile
Free-form planes allow the system to pick up on deviations from the typical contour of a surface. This makes stable defect detection possible, even for targets with complex shapes.
2D/3D Laser Profiler LJ-X8000 series
Lumber Grading
Highly accurate measurements can be made even when measuring targets with height differences or where the distance from the target to the camera could vary.
2D/3D Laser Profiler LJ-X8000 series
Bead Appearance Inspection After Welding for Can Sealing
Detect chipping or dents in laser welded beads using 3D laser profilers. The measurement is unaffected by the color or gloss of the weld, making inspection results stable through glare or bead shape variation.
2D/3D Laser Profiler LJ-X8000 series
Smartphone Assembly Inspection
Targets with multiple materials can be captured in a single profile, allowing measurements to be made between glass and metal surfaces. The LJ-X Series is equipped to handle reflections ten times higher than conventional products.
2D/3D Laser Profiler LJ-X8000 series
360° Inspection of Stepped Shaft
For targets with different diameters, conventional vision systems often have a hard time focusing on the larger and smaller diameter areas at the same time. Measuring the height of the dents with a laser profiler makes it possible to inspect the whole surface at once.
2D/3D Laser Profiler LJ-X8000 series
Post-Assembly Construction and Height Difference Inspection
3D inspection allows users to accurately detect whether components are properly seated in the assembly or if elements are tilted. Using a KEYENCE 2D/3D laser profiler with a blue laser ensures stable measurement, even for targets with varying materials.
2D/3D Laser Profiler LJ-X8000 series
3D Measurement of Transparent and Mirrored Surfaces
A displacement sensor with an extremely small beam spot of just 3.5 µm can be used for accurate profile measurements of roughness and subtle shapes. 3D shape measurements are also possible through detailed scanning synchronized with the X-Y stage. Measurements with impressive angle characteristics are possible not only for opaque targets but also for transparent targets and 3D shapes with mirrored surfaces.
Confocal Displacement Sensor CL-3000 series
Cookie Inspection
The laser profiler's wide field of view makes it possible to inspect multiple targets traveling on a conveyor belt together. 3D position correction can be used to identify and inspect each cookie within the measurement range, enabling accurate sorting to improve quality and eliminate waste.
2D/3D Laser Profiler LJ-X8000 series
3D Inspections With Laser Snapshot Sensors
3D inspections have become very important for ensuring product quality across industries. KEYENCE laser snapshot technology for 3D inspections offers significant advantages over conventional methods. By capturing 3D profiles, the KEYENCE 3D inspection device can provide fast, accurate, and reliable data on any object. It makes use of a non-contact approach that minimizes the risk of damaging delicate parts, and the detection of fine surface variations is another feature it has to ensure superior quality control.
Laser Snapshot Sensors vs. Traditional 3D Inspection Methods
Traditional 3D inspection methods often rely on contact or mechanical tools, which often produce errors, especially with delicate parts. Laser snapshot sensors offer a non-contact alternative subsequently, reducing the potential for inaccuracies caused by surface friction. The precision of laser snapshot sensors is unmatched when it comes to dealing with complex surface areas, and they quickly provide real-time feedback that enhances efficiency in production lines.
Laser Snapshot Sensor Solutions for Complex 3D Inspection and Measurement
Laser snapshot technology for 3D inspections excels when it comes to inspecting complex parts or components with detailed features. These sensors provide detailed profile measurements with snapshot sensors using snapshot technology to capture 3D data from multiple angles. In industries where quality standards are stringent, such as aerospace and automotive, the advantages of this device are particularly significant.
With the LJ-S8000 Series, you can achieve high-speed 3D measurements with micrometer-level accuracy, enabling precise detection of surface defects and dimensions. This capability gives manufacturers an edge by ensuring that their products meet quality standards and maintaining customer satisfaction.
LJ-S8000 Sensors for 3D Inspection and Measurement
KEYENCE’s LJ-S8000 Series sensors are designed to offer reliable solutions for 3D inspection and measurement tasks. These sensors utilize laser snapshot technology for high-speed 3D measurements with micrometer-level accuracy, enabling precise detection of surface defects and dimensions across industries. With an ultra-fast imaging speed of 0.2 seconds, these sensors can perform real-time inspections on a wide range of materials and targets.
To learn more about how LJ-S8000 Series sensors can optimize your inspection processes, contact us and explore how they can enhance your 3D measurement capabilities.
Related Downloads
![Key Technology and Applications [3D Measurement]](/img/asset/AS_110781_L.jpg)