Measurement Sensors
Deflection Measurement
When choosing a deflection sensor to measure runout or deflection, you'll need to consider both accuracy and speed because the sensor needs to be responsive enough to capture the change. You can browse some options below or request a free consultation with a local specialist.
Get detailed information on our products by downloading our catalog.
View Catalog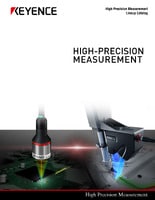
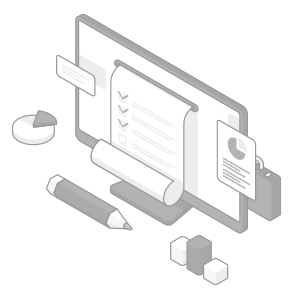
Rotor Runout Measurement
High-speed thrubeam deflection sensors can measure runout and ovality of rotors accurately and repeatably.
High-speed optical micrometer LS-9000 series
Drill Swings Multi-point Measurement
Measure drill bit diameter, wear, and eccentricity with a single 2D thrubeam sensor.
Telecentric Measurement System TM-X5000 series
Roll Runout Measurement
Measure roller runout using confocal sensors for high stability on reflective surfaces.
Confocal Displacement Sensor CL-3000 series
Injector Runout and Coaxiality Measurement
2D silhouette-based measurement makes it possible to accurately inspect the shape of the target. This provides a reliable solution for both multi-point inspection (such as coaxiality) and runout measurement.
Telecentric Measurement System TM-X5000 series
Importance of Precision When Measuring Deflection and Decentering
Precision in various measurements is paramount, as it directly impacts the performance, efficiency, and safety of a particular product, regardless of the industry. Pharmaceuticals rely on precision deflection measurement devices to accurately measure ingredients, electronics rely on precision for computation and signal processing, and construction relies on precision for calculating structural integrity.
Miscalculations caused by imprecise deflection measuring instruments can lead to underestimation of stress and strain, which in turn increases the risk of structural failures. The same happens across the board—imprecise measurements compromise product quality and adversely affect its functionality and reliability.
Beyond functional and reliability issues, most industries are regulated by strict laws and regulations. Failing to meet these regulations, particularly when it comes to critical systems, incurs massive legal penalties and reputational damage. In the end, inaccurate measurements during the manufacturing of bolts and sleeves were known to bring down entire aircraft.
In the context of measuring deflection and decentering, mechanical systems, in particular, rely on precise deflection and decentering measurements for parts manufacturing and function, further underlining their importance.
What is Measuring Deflection?
In structural engineering, deflection measurement refers to the degree to which a part of a long structural element, such as a wing on a plane, is laterally deformed. There are different types of deflection, and all of them are quantified in terms of an angle or a distance. Depending on the size and scope of measurement, measuring deflection can be done in various ways.
Depending on your application, you can rely on dial indicators for measuring minor displacement on smaller structures or rely on laser displacement sensors to measure the distance between the object and the sensor and translate the data into deflection measurements.
What is Measuring Decentering?
Besides deflection measurements, numerous industries also require precise measurements of decentering, or the deviation of a particular component or part from its specified central or aligned position.
The impact of decentering mostly depends on the application, and in some cases, even the most minute amount can be detrimental, while other cases might have an acceptable degree of tolerance. In the context of manufacturing and engineers, decentering usually refers to part and component misalignment, which subsequently affects their performance and longevity.
Types of Measurement Sensors Used for Deflection and Decentering
Depending on your application, both deflection and decentering can be measured rather precisely, down to the µm level, using thrubeam sensors, like an optical micrometer, and laser displacement measurement sensors.
Laser displacement sensors typically rely on light triangulation or time-of-flight to measure distance. Time-of-flight is self-explanatory; the sensor measures the time it took the light to depart the emitter, reflect off the object, and land on the photo-sensitive receiving element.
Triangulation measures distance using light triangulation. These sensors emit the light onto the object, which is then reflected onto the photo-sensitive receiving element. The distance is calculated based on the return angle of the light.
Thrubeam sensors are photoelectric sensors that measure deflection and decentering by emitting light onto the object, which produces a shadow on the light detector. The processing unit then measures the dimensions associated with the object and derives precise decentering and deflection measurements.
Integrating Measuring Deflection and Decentering into Your Processes
If you're manufacturing or production process relies on precise deflection and decentering measurements, laser sensors are the solution. They’re very precise, reliable, and have an exceptionally long measuring range.