Measurement Sensors
Dimension Measurement
Displacement Measurement
Syringe and Needle Inspection
KEYENCE offers measurement sensors for injection device manufacturers to help with quality control and defect inspection. Our inspection and measurement sensors enable manufacturers to verify the dimensional accuracy, function, sharpness, and packaging integrity of hypodermic needles attached to syringes. Use our needle inspection systems to ensure quality products that are safe for patients and compliant with regulatory standards.
Get detailed information on our products by downloading our catalog.
View Catalog![Automated Measurement and Inspection Examples [Medical Devices]](/img/asset/AS_119876_L.jpg)
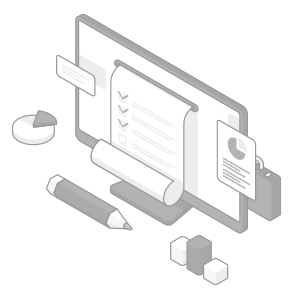
Needle Inspection: Ensuring Safety and Precision
Hypodermic needles or cannulas serve as the medium through which non-ingestible substances get into the body. Inspecting these needles is crucial for the safety of patients receiving vaccinations and blood transfusions.
Injection equipment manufacturers must ensure the safety of patients from potential infections, adverse reactions, or even death with the right inspection and measurement sensors for the medical equipment manufacturing industry. These sensors can help verify if the tip of the needle is sharp and free of irregularities that could cause human tissue damage or needle breaking in the patient's body.
In addition to tip sharpness, shaft straightness and surface finish are two of the many other properties of any hypodermic needle that require measurement precision. With KEYENCE solutions, such as our 3D laser profiler, manufacturers can ensure dimensional precision and the safety of finished goods.
Comprehensive Syringe Inspection for Quality Assurance
For syringe needles to penetrate the skin, their tip must be beveled. The bevel design starts with an extrusion process where stainless steel or niobium is rolled into tubes and passed through dies to thin and harden the material.
During this extrusion process, the tip of the needle is shaped into a specific point angle. The process of grinding or sharpening the bevels can create hooks, burrs, uneven surfaces, or other irregularities that impair functions or are dangerous to the patient.
A measurement and inspection system that can perform a full or comprehensive needle syringe inspection is desired. Such systems can be calibrated to simultaneously verify the length, diameter, point angle, straightness, and other properties of the syringe, helping manufacturers with quality assurance efforts.
Automated Syringe Testing for Defect-Free Products
A human-dependent or manual syringe inspection machine is ineffective when it comes to achieving defect-free syringe needle products. On the other hand, automated hypodermic needle testing systems help manufacturers carry out precision-based inspections on even large production runs.
Our syringe testing systems are fully automated and require minimal human input for such areas as system setup and programming. Use KEYENCE solutions to inspect syringe needles for defects such as cracks and burrs in addition to length, diameter, and sharpness checks.
We’re here to provide you with more details.
Reach out today!
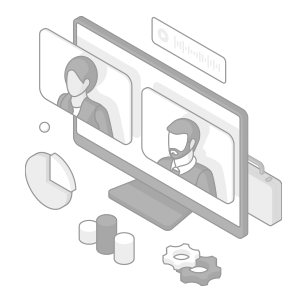
Challenges in Syringe and Needle Inspection and Testing
Some issues and problems pose a threat to accurate needle inspection and testing. These include:
- Surface treatment
- Material composition
- Improper equipment calibration
- High-volume production
For manufacturers producing large volumes of syringes and needles, an unreliable needle inspection and syringe testing system can lead to costly waste or incessant unplanned downtimes, with all of these issues affecting production and product quality.
This is why manufacturers must find a reliable hypodermic needle testing solution that can accurately inspect surface irregularities, guarantee high accuracy of measurements, and meet the demands of large productions.
Benefits of Automated Needle and Syringe Inspection Systems
There are many advantages to deploying automated inspection systems in syringe manufacturing facilities.
Accuracy
Advanced sensors and imaging techniques found in automated systems enable accurate measurements of needle tip diameter, sharpness, and other dimensions.
Automation
With high-speed inspection to meet production volume demands, automated syringe testing and inspection systems help manufacturers inspect a large number of products in a short time. Quick and fast inspection increases efficiency and productivity. It also reduces manual labor and associated costs.
Quality Control
Also, the injection device manufacturing industry is highly regulated. Especially with new needle tip models coming out, regulatory standards require manufacturers to get their quality control efforts right. A small defect in any production batch can compromise patient safety and potentially be dangerous to even the healthcare professionals handling affected needles.
Through our automated syringe inspection solutions built for accuracy and reliability, KEYENCE is proud to be a partner for injection device manufacturers in quality assurance.
For more information about our measurement and inspection sensors for hypodermic needles, contact us today.
Contact us to learn more about how our advanced technology can help take your business to the next level.
Contact Us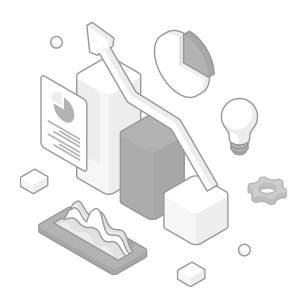
Related Products
Applications
Dimension Measurement
- Thickness and Width Measurement
- Step Height Measurement
- Inner and Outer Diameter Measurement
- Measuring Angles
- Meandering/Edge Measurement
Displacement Measurement
- Positioning and Stroke Length Measurement
- Vibration and Runout Measurement
- Deflection Measurement
- Measuring Eccentricity