Measurement Sensors
Dimension Measurement
Displacement Measurement
Sensors for Cheese Portioning and Inspection
Cheese manufacturing relies on measurement sensors to achieve optimal yield, efficient processing, and consistent food quality. Laser sensors check the dimensions, alignment, and positioning of the cheese block. They also double as inspection tools for the conveyor belt system and the cutting machine.
Get detailed information on our products by downloading our catalog.
View Catalog![Automated Measurement and Inspection Examples [Food and Containers]](/img/asset/AS_138240_L.jpg)
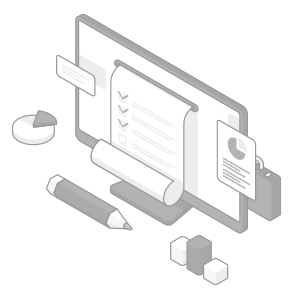
Importance Of Precise Cheese Portioning for Consistency and Efficiency
Cheese manufacturing sites can reduce waste more effectively when a cutting machine can precisely determine the volume of the cheese and cutting frequency. This allows manufacturers to maximize profitability.
Weight-accurate slicing is a critical part of cheese portioning optimization. Certain cutters offer automatic slicing gap monitoring to maintain consistency in slice quality. Consistency in the size of a cheese product lets processed goods sit well in product packaging. This enhances customer satisfaction as consumers are quick to notice irregularities in package sizes.
Common Cheese Inspection Methods and Technologies
There are different technologies and methods used in cheese inspection and measurement, each offering unique benefits. The following are the common methods and sensors for food quality and safety.
Cheese Position Monitoring
Cheese position monitoring ensures uniformity and quality in the final product. By using sensors such as 2D/3D laser profilers like the LJ-X8000 Series, manufacturers can accurately measure and monitor cheese placement on conveyors or packaging lines. This cheese inspection ensures that each piece of cheese is evenly spaced, preventing potential issues like damage to equipment or irregular cheese shapes during production.
Cheese Volume Measurement
KEYENCE's LJ-X8000 Series measures the volume of sliced cheese as it is sent for sorting. By measuring the height and width of the cheese, this sensor can accurately calculate its volume and ensure consistency in size. This helps maintain product quality and prevent customer complaints due to irregular package sizes.
Previously, manual inspection and vision systems were used for this, but these can require a lot of time and resources. The use of advanced sensors has made the cheese inspection process more efficient, accurate, and cost-effective.
Cheese Wrapping Tear Inspection
One of the challenges in cheese inspection is detecting tears or damage in the wrapping material. This could lead to contamination and spoilage of the cheese, affecting its quality and safety. Laser surface inspections using the LJ-X Series can accurately capture changes in surface shapes caused by film tears. Conventional manual inspection or even vision systems find it hard to detect these defects, making the 3D laser profiler a useful tool in ensuring the integrity of cheese packaging.
Implementing The Right Sensor Technology for Cheese Portioning Optimization
There are different types of measurement sensors for the food and beverage industry. However, the type chosen in individual industrial situations will depend on the type of surface, range, and other parameters. As mentioned earlier, sensors on the principle of triangulation are better suited for short-range profiles and non-reflective/transparent surfaces. On the other hand, confocal displacement sensors are the better option for longer ranges and all material types.
KEYENCE offers 2D and 3D inspection and measurement solutions in both laser triangulation and confocal sensing technology with high-quality performance. The LJ-X8000 Series, for example, is a 2D/3D Laser Profiler that measures targets with ultra-high precision and has a wide field of view. It would find application in cheese manufacturing lines and other food and beverage industrial applications.
Ready to get the right cheese portioning measurement and cheese inspection tool? Contact us today!
Contact us to learn more about how our advanced technology can help take your business to the next level.
Contact Us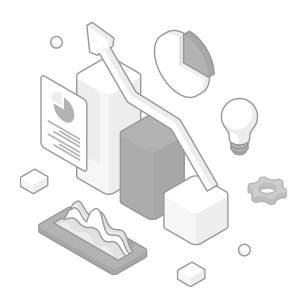
Related Products
Applications
Dimension Measurement
- Thickness and Width Measurement
- Step Height Measurement
- Inner and Outer Diameter Measurement
- Measuring Angles
- Meandering/Edge Measurement
Displacement Measurement
- Positioning and Stroke Length Measurement
- Vibration and Runout Measurement
- Deflection Measurement
- Measuring Eccentricity