Measurement Sensors
Dimension Measurement
Displacement Measurement
Package Seal Inspection
KEYENCE offers package seal inspection systems for food and beverage manufacturers to ensure food products and drinks are well-sealed and contaminant-free. Our solutions enable production facilities to carry out accurate food packaging and seal integrity tests in order to avoid product recalls, returns, and waste. Use our inspection technology to enhance regulatory compliance and consumer satisfaction.
Get detailed information on our products by downloading our catalog.
View Catalog![Automated Measurement and Inspection Examples [Food and Containers]](/img/asset/AS_138240_L.jpg)
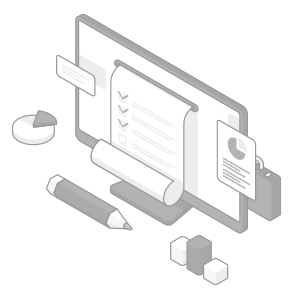
Challenges in Packaging Inspection and Seal Testing
Inspecting food and beverage seals presents several challenges to manufacturers. Common difficulties include:
- Diverse packaging materials
- High-speed production lines
- Difficult-to-detect defects
- Environmental factors
- Evolving regulatory standards
Primary packaging such as sachet, pouches, stick packs, and cans have unique properties and testing requirements. Every packaging material needs an ideal inspection device or system for accurate inspection results. In modern production environments where large volumes of products are produced, the speed of inspection is a significant factor.
Conventional package seal inspection systems especially struggle to keep up with fast-paced lines. Employing inadequate packaging inspection equipment can lead to delays in production runs and unnecessary downtime. Also, certain defects can be inconspicuous even to these inspection systems. Small damages to package seals, like subtle tears, pinholes, tiny tears, and minuscule foreign particles, can be difficult to detect.
Other factors, such as overwhelming or underwhelming environmental lighting and ever-changing regulatory requirements, can also pose serious challenges for manufacturers in their efforts to achieve accurate inspections for package seals.
Best Practices for Package Seal Inspection
For food and beverage companies, proven package seal verification approaches should be prioritized for inspection. Here are some of the main best practices:
Use the Correct Systems
Using the right packaging inspection products will save line operators and managers the stress associated with utilizing ineffective inspection solutions. Depending on factors such as production line setup and packaging materials used, some inspection systems are better suited for sealing inspections than others.
KEYENCE offers different inspection and measurement sensors, such as the 2D/3D laser profiler, suitable for different packaging and seals. Our laser profiler inspection device can measure three-dimensional data, capturing precise surface details, including subtle defects and dimensional variations. It can detect missing, incomplete, and damaged seals. Surface defects on seals, such as dents, scratches, and foreign objects, can also be identified thanks to the advanced imaging systems.
Equipment Needs to Be Correctly Calibrated
Inspection equipment should be regularly and adequately calibrated, especially during product changeovers. It might be a no-brainer to prep an inspection device for an initial production run, but it’s easy to rush through readjusting settings for a different product batch during tight deadlines.
Up-to-Date Personnel Training
In addition, inspection personnel should be trained on adequate equipment configuration and calibration to ensure the accuracy and reliability of inspection results. Following the best inspection practices helps with error-free inspection efforts.
Curious about our pricing?
Click here to find out more.
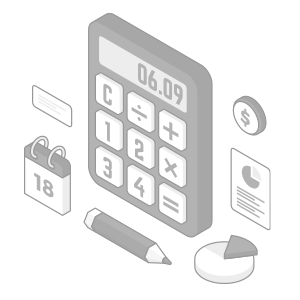
Benefits of Automated Packaging Inspection for Food Manufacturers
Automated inspection equipment significantly outperforms human or manual inspection arrangements . Here are some benefits of automated packaging inspection:
Speed
These solutions can inspect food and drink packages at high speeds. Speedy inspections increase efficiency and reduce labor costs.
No Fatigue
Automated packaging systems provide enhanced inspection results because their defect detection capabilities require less human intervention. Automated inspection tools work on a set of programmed rules and instructions and are not susceptible to fatigue faced by human inspectors after prolonged attention.
Failure Data
Self-operating inspection products are also able to collect data on why certain products fail inspection. Data collected helps with analysis and informs future inspection and production efforts.
With automated inspection devices, food and drink manufacturers comply with compliance regulations and deliver safe foods into the hands of consumers.
Ensure Quality and Safety with Our Package Seal Inspection Solutions
With the regular entry of new competitors in the food industry, retailers and consumers have access to unlimited options. Any food or drink brand wanting to be relevant and competitive must ensure the integrity of the packaging and seals of finished goods. Getting this effort right helps preserve product shelf life and consumer satisfaction.
KEYENCE is proud to be a reliable partner for food manufacturers in their inspection efforts. Our inspection and measurement sensors for the food and beverage industry enable manufacturers to deliver high-quality products to the market and stay compliant with regulatory standards. For more information about package seal inspection products, contact us today.
Contact us to learn more about how our advanced technology can help take your business to the next level.
Contact Us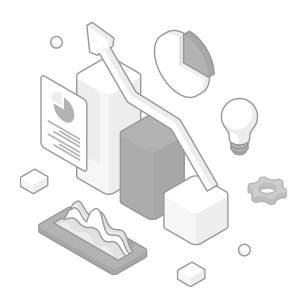
Related Products
Applications
Dimension Measurement
- Thickness and Width Measurement
- Step Height Measurement
- Inner and Outer Diameter Measurement
- Measuring Angles
- Meandering/Edge Measurement
Displacement Measurement
- Positioning and Stroke Length Measurement
- Vibration and Runout Measurement
- Deflection Measurement
- Measuring Eccentricity