Measurement Sensors
Dimension Measurement
Displacement Measurement
3D Final Product and Packaging Inspection
Inspecting food products and their final packaging for adherence to quality standards is one production effort manufacturers must get right. While inspection mechanisms are typically deployed at critical control points, final inspections help manufacturers ensure nothing falls through the cracks.
3D inspection systems are one of the best technologies for accurate, final inspections. 3D final product inspection systems are a product of choice among food producers for many reasons.
To better appreciate their role, we explore the benefits, applications, and features of 3D inspection systems that make them desirable in final packaging inspections in the following.
Get detailed information on our products by downloading our catalog.
View Catalog![Automated Measurement and Inspection Examples [Food and Containers]](/img/asset/AS_138240_L.jpg)
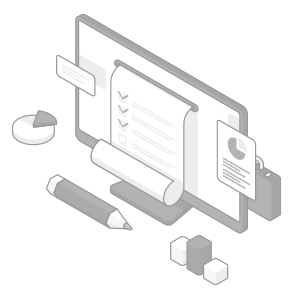
Key Benefits of 3D Inspection Systems
Food and beverage producers do not use 3D inspection systems for no reason. Here are two of the many advantages inspection technologies with 3D capability bring to food production.
Automation
Inspecting for defects or inconsistencies in final food products numbering into the thousands or millions using manpower would be painstakingly boring and difficult. When boredom sets in, humans lose focus, leading to inaccurate assessments. Plus, why put many employees to inspection when one machine system can complete the job a lot faster? 3D inspection technologies help automate inspection tasks, allowing operators, managers, and other line workers to work on other production tasks.
Regulatory Compliance
Some areas of production have strict regulations regarding seal integrity, labeling quality, and accurate declaration of product information. 3D systems help check whether all aspects of final products conform to established quality regulations, allowing food producers to avoid fines and legal battles.
Applications of 3D Final Product Inspection
Here are different ways a 3D product inspection system can be used to identify issues with food packages.
Container Integrity Checks
Incorrect sealing, bottle leakages, and punctured packaging are some issues that can introduce contamination and decrease product shelf life. A 3D inspection system can help check for these problems during final packaging, ensuring high-quality products reach consumers.
Product Positioning Verification
Verification of product positioning addresses areas such as incorrect insertion, overlaps, and empty spaces. With the capability to capture depth information, three-dimensional inspection systems can recognize when, for example, a product is lying horizontally instead of standing vertically.
Labeling Errors Identification
Inaccurate or unclear coded data or printed information on food labels disempowers the consumer when making buying decisions. 3D inspection systems follow a set of rules to recognize and isolate labeling issues during final packaging inspection.
Correct Fill Level Checks
Consumers do not appreciate receiving less for what they paid for in full. Using 3D inspection systems can help detect low fill levels in drinks and beverages.
Discover more about this product.
Click here to book your demo.
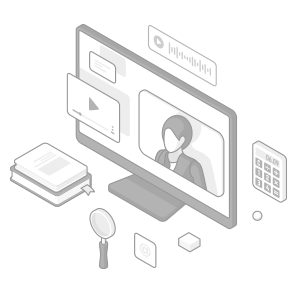
Features of Advanced 3D Inspection Systems
Below are three of the many features that make 3D inspection systems desirable in final inspection efforts.
Depth Data
The ability to measure height (depth) data during inspections is one of the features that make 3D inspection systems useful. A 3D laser profiler, for example, can create a three-dimensional profile of products under its inspection, enabling all angle checks.
Speed
3D inspection systems such as laser displacement sensors can help complete inspection tasks for thousands of food products in a fraction of the time it would take a team of human checkers.
Precision
Human checkers and traditional inspection systems are liable to misclassifications due to fatigue and design limitations. 3D-based inspection systems typically consist of sensors, optics, and software algorithms that all contribute to accurate inspection results.
Integrating 3D Inspection into Your Quality Control Process
For food producers who have yet to tap into the power of 3D product inspection systems, this is the time. With new players entering the market every day and regulatory standards getting stringent, manufacturers can stay in the game for a long time with 3D packaging inspection solutions by their proverbial side.
As a leader in measurement and inspection solutions, KEYENCE provides a wide range of measurement sensors and inspection products that find application in different manufacturing plants and production lines.
Contact us today for more information on how one of our 3D packaging inspection solutions can integrate into your new or existing quality control process.
Contact us to learn more about how our advanced technology can help take your business to the next level.
Contact Us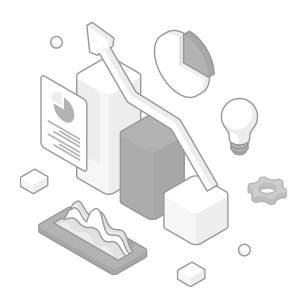
Related Products
Applications
Dimension Measurement
- Thickness and Width Measurement
- Step Height Measurement
- Inner and Outer Diameter Measurement
- Measuring Angles
- Meandering/Edge Measurement
Displacement Measurement
- Positioning and Stroke Length Measurement
- Vibration and Runout Measurement
- Deflection Measurement
- Measuring Eccentricity