Measurement Sensors
Dimension Measurement
Displacement Measurement
Measurement Sensors for Building Material Manufacturing
The building material manufacturing industry relies on measurement sensors across the various stages of production, ensuring the efficiency of the production process and the quality of the building material. More specifically, the use of measurement sensors in building material manufacturing ensures that the end product adheres to industry-specific standards.
The variety of building material applications for measurement sensors underscores their versatility.
Get detailed information on our products by downloading our catalog.
View Catalog![Automated Measurement and Inspection Examples Building Materials [Flooring material/External wall/Roof]](/img/asset/AS_118581_L.jpg)
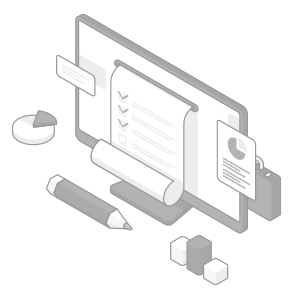
Common Measurement Applications
The building material manufacturing industry relies on different types of measurement sensors, such as laser profilers and laser displacement sensors, to ensure accuracy and consistency in material production.
Some of the most common applications include measuring plywood thickness as well as the thickness of surface plates, depth and width measurements after growing, mortar joint width measurements, thickness and width of siding materials, roofing materials inspection, and many other applications.
For example, laser profilers such as the LJ-X8000 Series 2D/3D Laser Profiler provide plywood surface inspections before adhesive applications, to minimize disposal costs and improve the overall product quality. Additionally, the CL-3000 Series confocal displacement sensor can be used to measure the thickness of the adhesive to be applied to said surfaces.
We’re here to provide you with more details.
Reach out today!
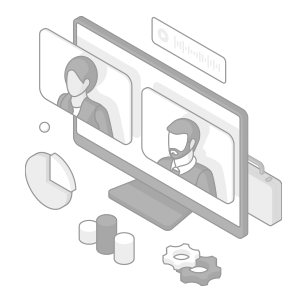
Plywood Thickness Measurement
Plywood board is manufactured by bonding multiple veneers, which can lead to thickness variation across the width. Laser displacement sensors can be set up across the board to continuously monitor for thickness variation. Thickness inspection during the manufacturing process will lead to higher yield rates and quality.
Thickness Measurement of Surface Plates and Printed Sheets
Variations in thickness of surface plates and printed sheets greatly impact product quality.
By continuously monitoring thickness across the sheet, process adjustments can be made to eliminate variation and improve quality.
Plywood Surface Inspection Before Adhesive Application
Foreign particles can be found on plywood surfaces by inspecting them before adhesive application. Checking the plywood’s surface conditions prior to applying surface plates or printed sheets can minimize disposal costs and improve overall product quality.
OK: No foreign particles / NG: With foreign particle
Adhesive Thickness Measurement
For flooring materials, applying the proper amount of adhesive is critical for the bottom line. If too little is applied, the surface material can come off, but applying too much increases material costs. By measuring adhesive thickness immediately after application, the optimal thickness can be maintained, improving quality while reducing costs.
Tongue and Groove Shape Measurement after Processing
Using 3D data, the roughness and irregularities of wooden surfaces can be averaged out, allowing for stable checking of processed shapes.
Mortar Joint Width Measurement During Forming
Flatness and mortar joint width will have an impact on both the appearance and strength of external walls, but their proper management can also reduce production waste. Measuring the mortar joint width immediately after forming can eliminate downstream processing issues, significantly reducing costs.
Positioning and Meandering Measurement in the Cutting Process
Final dimensions can be precisely controlled by monitoring workpieces for any meandering or shifted position prior to cutting.
Appearance Inspection after Pressing (Damage and Crack Inspection)
The LJ-X8000 Series allows for inline surface inspection for a variety of materials and colors. This improves the quality of the pressing process and ensures defective products are identified before additional processing occurs, reducing manufacturing costs.
Damage inspection
Crack inspection
Benefits of Using Measurement Sensors
Integrating building laser measurement sensors in building material manufacturing processes offers numerous benefits:
Increased Efficiency and Productivity
Increased efficiency and productivity are the primary benefits introduced by measurement sensor integrations. By automating the measurement processes, building material manufacturers significantly reduce the need for manual inspections, which also reduces inspection times.
This significantly speeds up the production cycles and enables a high throughput while minimizing human error, leading to more consistent and reliable measurements. Besides increasing efficiency and productivity, using these sensors also optimizes material use and reduces waste.
Improved Quality Assurance and Inspection
The adoption of precise laser measurement sensors also improves quality assurance and inspection processes by detecting even the slightest deviations from the specified standards. This ensures that every individual product meets the predetermined quality criteria.
This is particularly important for building materials with a very small margin for error due to potential structural integrity and safety implications. The increased accuracy and precision associated with laser measurement sensors also imply higher quality levels, allowing manufacturers of building materials to increase their market competitiveness.
Enhanced Safety and Reliability
Enhanced safety and reliability are the second biggest benefits of precise measurement sensors. Thanks to their precision, these sensors can detect potential defects or inconsistencies in building materials during the manufacturing process, mitigating the risks associated with potential structural failures and accidents.
This provides a rather comprehensive safety profile, as it ensures the safety of the end user but also ensures that the product won’t fail within its intended use while protecting manufacturers from reputational damages and financial losses associated with product recalls or critical failures.
Measurement Sensors for Building Material Inspection
The structural role of numerous building materials only underscores the importance of building material inspections during the manufacturing process. Advanced sensors, such as laser profilers and laser displacement sensors, are capable of performing non-contact tests, which allow for inspection of otherwise delicate and easily damaged materials such as films and foils.
In the end, building sensors are integral to the building material manufacturing process, as they provide a host of benefits capable of elevating the entire production process.
If you’re interested in enhancing the efficiency of your production process while maintaining and increasing the quality of your product, KEYENCE offers a comprehensive range of products that can help you achieve your goals. Contact us today!
Contact us to learn more about how our advanced technology can help take your business to the next level.
Contact Us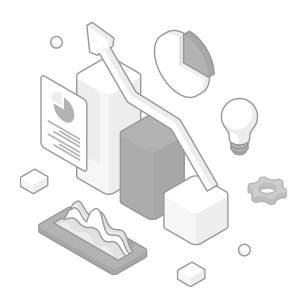
Applications
Dimension Measurement
- Thickness and Width Measurement
- Step Height Measurement
- Inner and Outer Diameter Measurement
- Measuring Angles
- Meandering/Edge Measurement
Displacement Measurement
- Positioning and Stroke Length Measurement
- Vibration and Runout Measurement
- Deflection Measurement
- Measuring Eccentricity