Measurement Sensors
Dimension Measurement
Displacement Measurement
Trim Final Assembly Verification
Final assembly is a critical stage in automotive manufacturing. It is a process where all vehicle components are gathered, requiring rigorous verification to ensure quality, performance, and safety. Specifically, trim final assembly verification (TFAV) focuses on inspecting the assembly of trim components, such as interior panels, dashboard elements, and exterior finishes.
Given the increasing complexity of automotive designs and the need for higher standards, TFAV is proven to be a vital quality control process for delivering a flawless product to the end consumer.
Get detailed information on our products by downloading our catalog.
View Catalog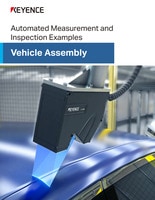
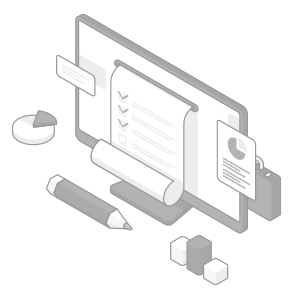
Common Challenges in Final Assembly Verification
There are many challenges that come with the final assembly process in automotive manufacturing. Ensuring that each part is uniform correctly requires highly detailed measurement and quality control.
Verifying Trim and Chassis Final Assembly
This is magnified by the diversity of materials and shapes used in modern car interiors and exteriors. Moreover, discrepancies in component tolerances, shifts in supplier quality, and human error can introduce inconsistencies that, if overlooked, compromise safety.
Recognizing Gaps, Flushness, and Alignment Errors Between Components
This is difficult to achieve consistently through manual inspection. Thus, manufacturers need more advanced tools and technologies that can deliver actual, repeatable, and swift inspections to meet automotive standards.
Why Trim Final Assembly Verification is Crucial for Automotive Quality Control
Trim final assembly verification is very important in the automotive industry for diverse reasons. One of the reasons is that it impacts customer satisfaction. Customers expect perfect finishes on both the interior and exterior of their vehicles, and imperfections can significantly influence their perception of quality. Ensuring that trim components are tightly attached and aligned contributes to safety by preventing likely hazards caused by loose or poorly fitted parts.
TFAV also plays a role in compliance with industry regulations and standards, as flawed assembly can lead to costly recalls and reputational damage. By integrating TFAV into quality control, manufacturers can prevent faults, reduce rework, and ensure vehicles meet customer expectations and regulatory requirements.
Automating Trim Final Assembly Verification for Greater Precision
Automation in trim final assembly verification has become an industry standard for achieving higher accuracy and consistency. Automated systems equipped with advanced sensors, cameras, and artificial intelligence (AI) software can detect assembly errors more correctly and swiftly than manual scrutiny.
Automated TFAV systems reduce human error, which is critical given the high volume and pace of production in modern assembly lines. These systems can measure critical parameters such as gap, flushness, and alignment, capturing high-resolution images and providing real-time feedback to production teams. Automated TFAV not only minimizes errors but also enhances efficiency by reducing inspection time, enabling faster and more accurate decision-making throughout the final assembly process.
Discover more about this product.
Click here to book your demo.
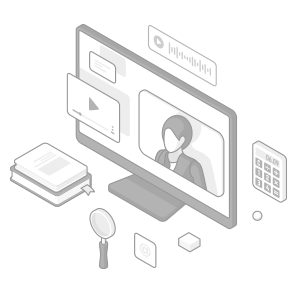
Benefits of Using Measurement Sensors for Trim Final Assembly Verification
Measurement sensors are central to accurate trim final assembly verification. Below are some benefits of using measurement sensors for this:
Precision
High-precision sensors can detect the smallest of errors in component alignment, surface uniformity, and fitment. For example, 3D Laser Snapshot Sensors and 3D profile sensors are widely used in automotive TFAV to measure gaps and flushness between trim elements.
Reliable
These sensors offer repeatable, high-resolution measurements that can identify inconsistencies down to the micron level. By utilizing such advanced measurement technology, manufacturers can quickly identify errors, reducing costly rework and ensuring uniform quality across the production line.
Data Logging
With sensors integrated into automated verification systems, data can be logged and analyzed for continuous quality improvement, leading to long-term cost savings and product development.
Why Choose KEYENCE for Final Assembly Verification Solutions?
KEYENCE is a recognized trailblazer in manufacturing automation and inspection technologies, making it an ideal choice for final assembly verification solutions. KEYENCE solutions are built with pioneering sensor technology that can precisely capture critical measurements in challenging environments, ensuring each component meets strict automotive standards. Their product line includes high-resolution cameras, laser sensors, and image processing units capable of detecting faults in time, enhancing the accuracy and effectiveness of the TFAV process.
KEYENCE’s systems are designed for ease of integration into existing assembly lines, reducing setup time and ensuring quick deployment. By choosing KEYENCE, automotive manufacturers can leverage industry-leading technology, comprehensive support, and a commitment to quality, ensuring that their final assembly processes consistently produce top-tier vehicles.
Contact us to learn more about how our advanced technology can help take your business to the next level.
Contact Us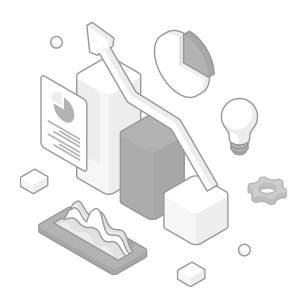
Related Products
Applications
Dimension Measurement
- Thickness and Width Measurement
- Step Height Measurement
- Inner and Outer Diameter Measurement
- Measuring Angles
- Meandering/Edge Measurement
Displacement Measurement
- Positioning and Stroke Length Measurement
- Vibration and Runout Measurement
- Deflection Measurement
- Measuring Eccentricity