Measurement Sensors
Dimension Measurement
Displacement Measurement
Transmission Assembly Inspection
The build quality of a vehicle's transmission system can significantly impact its need for diagnostic services. A well-coupled transmission is less likely to require frequent repairs or replacements, while a poorly designed one may need more frequent attention or fail on the user prematurely. To guarantee the structural integrity of assembled gearbox parts and ensure manufacturers’ competitiveness in a crowded market, transmission assembly plants need inspection systems.
Get detailed information on our products by downloading our catalog.
View Catalog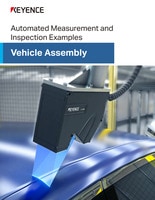
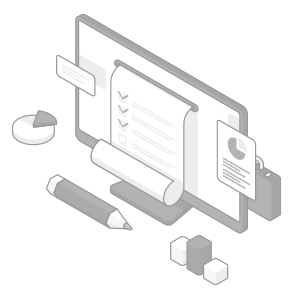
Key Benefits of Transmission Inspection Systems
Transmission inspection technology helps engineers in manufacturing plants pinpoint the reason for transmission defects and inconsistencies.
What needs fixing in the transmission design is checked and fixed before the final product is coupled and sent to the market. Below are some of the key benefits to manufacturers having assembly transmission inspection solutions in place.
Defect Detection
With inspection systems, structural defects and performance issues are detected early in the assembly process, ensuring defective units don't slip through.
Consistency of Design Parts
Inspection systems like a 3D laser profiler can be used to uncover dimensional irregularities, even on tiny components.
Automation
The inspection system provides automated checks, eliminating the need for manual inspections. Automation reduces labor costs and improves efficiency.
Data Collection
A lot of transmission inspection systems can collect and analyze data on specific production metrics. This helps manufacturers identify areas for improvement in future production runs.
Improve Compliance
Automotive part manufacturing is one sector where strict compliance with quality standards is mandatory. Transmission quality control systems help manufacturers meet traceability and high-quality requirements.
We’re here to provide you with more details.
Reach out today!
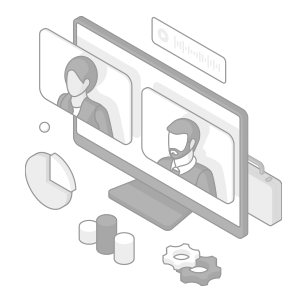
Applications of Transmission Assembly Inspection
Transmission production inspection systems are used at different stages of the production workflows.
3D measurement sensors can measure the thickness of gaskets, shims, and other components. They can also be used to inspect the diameter of bores and cylinders for accuracy. Dimensional accuracies of parts like gears, shafts, and bearings can also be ascertained using inspection systems.
In addition to measuring component tolerances, the alignment of parts such as the input/output shaft and planetary gear set must be checked, too.
Features of Advanced Transmission Inspection Systems
To meet the always-evolving automotive systems' technological demands, advanced inspection solutions must be used to complete checks for defects and proper functioning of gearboxes. Here are a few features to look for in cutting-edge inspection technology.
Non-Contact Measurement Capabilities
An inspection system for automotive transmission needs must be able to measure height, width, length, and distance without physically touching the target. These types of sensors make it easier to measure parts in hard to reach places.
Powerful Software and Data Processing Algorithms
These two factors contribute greatly to a system's accuracy and speed during measuring and inspection tasks.
Data Analysis
Data analysis capability provides product engineers with tools and metrics they can use to make data-driven decisions.
Implementing Transmission Inspection in Your Workflow
Checking for necessary parts during transmission assembly plays a vital role in automotive gearbox systems. Implementing transmission inspection solutions at critical control points in your manufacturing workflows helps with quality assurance, reliability of automotive systems, and compliance efforts.
KEYENCE offers a line of measurement sensors, including laser displacement sensors that can be incorporated into new or existing transmission plants. For more information on KEYENCE transmission assembly inspection systems, contact us today.
Contact us to learn more about how our advanced technology can help take your business to the next level.
Contact Us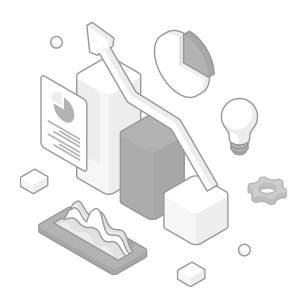
Related Products
Applications
Dimension Measurement
- Thickness and Width Measurement
- Step Height Measurement
- Inner and Outer Diameter Measurement
- Measuring Angles
- Meandering/Edge Measurement
Displacement Measurement
- Positioning and Stroke Length Measurement
- Vibration and Runout Measurement
- Deflection Measurement
- Measuring Eccentricity