Measurement Sensors
Dimension Measurement
Displacement Measurement
Sensors for Food Sorting
Food manufacturing and producing companies face significant challenges with mislabelled products, damaged goods, leaky products, and unsealed packages… all of which lead to quality issues.
Conveyor belts and other traditional food sorting systems are prone to errors, such as labels being applied to the wrong side of the box.
Modern measurement sensors for the food and beverage industry are an alternative to traditional sorting systems. These systems inspect the quality, safety, and aesthetics of food products delivered to the market, ensuring no compromised products leave the production line.
Get detailed information on our products by downloading our catalog.
View Catalog![Automated Measurement and Inspection Examples [Food and Containers]](/img/asset/AS_138240_L.jpg)
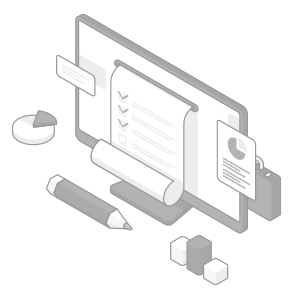
The Importance of Food Sorting
Many processes and activities occur down a production or manufacturing line. During these fast-paced processes, product leakages, defective packaging boxes, foreign objects of similar sizes and shapes, and other problems could arise.
Defect detection is why food sorting and inspection sensors are crucial throughout the manufacturing process. Historically, manual sorters were employed. However, as the demand for consumer goods continues to rise, accurate and efficient food sorting is more important than ever before.
Types of Sensors Used in Food Sorting and Processing
Many sensors for food sorting are available, each providing different functions and useful for different applications. Common types used in food industries include laser displacement sensors, measurement sensors, laser profilers, and 3D sensors.
Laser displacement sensors are non-contact devices that measure a target’s position, height, or distance. Some of them are very compact and can be used in narrow spaces. Others offer superior measurement and provide more reliable results on a wide range of materials. These sensors can be used to spot deviations in food products and packaging boxes.
3D sensors are used in food sorting applications. They capture and process three-dimensional data, and can measure small parts in confined spaces stably and without blind spots. This is a key advantage over confocal and triangulation sensors. They are also great at catching small defects in continuous processes, such as packaging boxes moving through a production line. Overall, 3D inspection and measurement provides advanced sorting and detailed product analysis.
The type of food processing sensor employed will be based on application, space constraints, and other considerations.
We’re here to provide you with more details.
Reach out today!
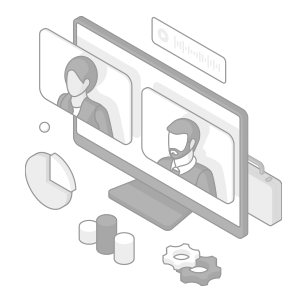
Benefits of Using Sensors in Food Inspection and Sorting
Food inspection technology and sorting systems profit greatly from sensors. A sensor, for example, can be mounted on a robot designed for inspection and sorting. 3D sensors provide high-quality images for analysis and can help scan big targets in wide conveyor food processing applications. Overall, sensors help in inspection so food companies can achieve 100% quality control.
Food industries need to analyze, monitor, and inspect food products for consistency, defects, spoiled produce, unsealed packages, and other irregularities that could severely affect companies’ revenue and the health of consumers.
All in all, using food sensors in the food industry helps companies sort through and inspect food produce at great speed and efficiency, ensuring quality products get into the hands of consumers.
Implementing Sensor Technologies in Food Sorting
Measurement sensors can be implemented at different stages of food sorting and inspection. KEYENCE’s CL-3000 Series confocal displacement sensor can be mounted on robots to inspect activities on the production line. Incorporating a sensor like this for food inspection and sorting leads to faster production and better food quality.
Fortunately, KEYENCE provides multiple sensors that can be used in the food industry. Our reliable sensor technology can give human inspectors the needed assistance to identify issues in food production and packaging before they are sent out to the market. Have more questions about KEYENCE’s sensor systems? Contact us today.
Contact us to learn more about how our advanced technology can help take your business to the next level.
Contact Us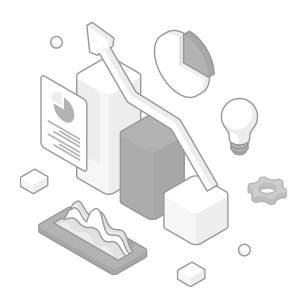
Related Products
Applications
Dimension Measurement
- Thickness and Width Measurement
- Step Height Measurement
- Inner and Outer Diameter Measurement
- Measuring Angles
- Meandering/Edge Measurement
Displacement Measurement
- Positioning and Stroke Length Measurement
- Vibration and Runout Measurement
- Deflection Measurement
- Measuring Eccentricity