Measurement Sensors
Dimension Measurement
Displacement Measurement
Bottle Inspection Sensors
The food and beverage industry is a fast-paced production environment in which thousands upon thousands of products are manufactured, packaged, dated, and then packaged again before being distributed to retailers and consumers.
This fast-paced environment demands high-quality defect detection systems that can keep up with production without compromising product quality. Defect detection systems ensure customer safety and loyalty. These systems also protect your brand from reputational and financial loss.
Detecting defects is particularly important when it comes to beverages and beverage packaging. Bottle inspection machines are designed to detect a wide range of defects and contaminants in bottles (such as cracks, deformities, and foreign material) before they even reach the consumer.
Get detailed information on our products by downloading our catalog.
View Catalog![Automated Measurement and Inspection Examples [Food and Containers]](/img/asset/AS_138240_L.jpg)
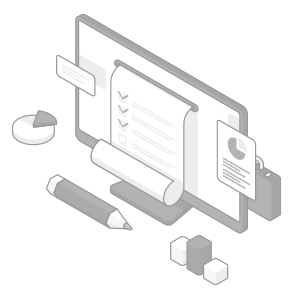
Key Characteristics of Bottle Inspection Sensors
Bottle inspection sensors in the food and beverage industry must feature several characteristics that would make them ideal for quality control in bottling operations. KEYENCE bottle inspection sensors feature high-resolution imaging capabilities that allow them to perform detailed bottle inspections, regardless of color or material.
Their high accuracy (in the single-digit µm range) allows them to detect minute defects that are otherwise invisible to the naked eye. Additionally, these sensors are designed to accommodate a wide variety of bottle sizes and shapes thanks to the powerful algorithms that are in charge of image processing.
Lastly, their robust design implies effective operation in harsh manufacturing environments, including exposure to varying temperatures and moisture.
How Bottle Inspection Works
Bottle inspection machines rely on 2D/3D Laser profilers, which are laser displacement sensors capable of measuring different properties. They're also complemented by powerful image-processing algorithms, which enables them to perform a wide range of operations that aren't strictly measurement-based.
For example, KEYENCE's LJ-X8000 Series is often used for surface inspection, which can help detect changes in the surface that are caused by bottle-wrapping tears. The sensor is equipped with a large-aperture receiver lens, which is specifically designed to capture the reflected light from scattering across the surface of the target—something that often happens with reflective cylindrical objects.
Additionally, it's not uncommon for bottles to tip to their side when moving via conveyors, and these sensors excel at detecting the bottle's orientation. This way, bottles that have fallen over or become unbalanced aren't selected for packaging, which helps reduce system downtime due to broken bottles or suck conveyors.
Likewise, the TM-X5000 systems are often used in quality assurance and control in bottle capping operations. They're capable of accurately measuring the outside diameter of the opening on a bottle/container, including simultaneous measurements of both the threads and the ring. They can also detect whether or not the bottle cap has been secured or whether the overall packaging might have a dent or some other defect.
Benefits of High-Speed Bottle Inspection
The benefits of using high-speed bottle inspection sensors are multifaceted. The main benefit of this inspection method is speed; machine inspection is much faster and much more accurate than manual inspection—which is susceptible to human error. This ensures that your product is properly packaged for distribution and safe from any contaminants, and thus safe for consumption.
This offers many financial and reputational benefits by safeguarding your business from potential issues caused by inadequate packaging. Additionally, bottle inspection ensures that you are compliant with the standards and regulations governing your industry.
Lastly, the increased efficiency of quality assurance also implies a more effective production process, which increases the output and, by extension, the profitability of your business.
Why Choose KEYENCE's Bottle Inspection Sensors
KEYENCE is the world's leading provider of precision technologies, including non-contact measurement sensors that are often used in bottle inspection applications. If you're looking to enhance your bottle inspection throughout your production process, don't hesitate to contact KEYENCE and inquire about integrations of our equipment with your production lines.
Contact us to learn more about how our advanced technology can help take your business to the next level.
Contact Us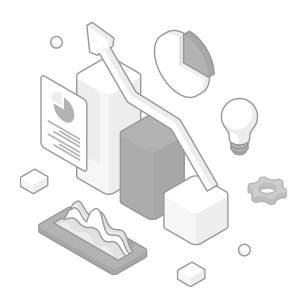
Related Products
Applications
Dimension Measurement
- Thickness and Width Measurement
- Step Height Measurement
- Inner and Outer Diameter Measurement
- Measuring Angles
- Meandering/Edge Measurement
Displacement Measurement
- Positioning and Stroke Length Measurement
- Vibration and Runout Measurement
- Deflection Measurement
- Measuring Eccentricity