Measurement Sensors
Dimension Measurement
Displacement Measurement
Wire and Cable Inspection Sensors
The manufacturing of wires and cables requires meticulous attention to detail to ensure that the final product meets the design and technical specifications. That’s why industries dealing with wires and cables rely on wire inspection sensors to thoroughly check the product during the entire production process, thus ensuring quality.
Get detailed information on our products by downloading our catalog.
View Catalog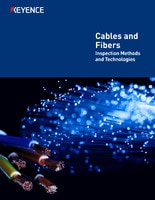
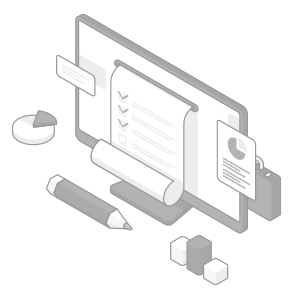
Key Characteristics of Wire and Cable Inspection Sensors
The key characteristics of wire inspection sensors mostly depend on the type of wire being manufactured. Regardless of the type, wire inspection sensors must feature high accuracy to detect even the smallest inconsistencies in wire or insulation diameter.
Durability is also a crucial factor, as many of these sensors are exposed to heat, dust, and mechanical vibrations—especially those mounted near the insulation extrusion machines that are used to apply insulation coating to the copper conductor.
KEYENCE’s LS-9000 high-speed optical micrometer meets both requirements. These units have built-in air purge filters and an IP67 rating, making them perfectly suited for harsher environments. They can also measure wires as small as ø10 µm since their optical design enables the measurement of ultrafine gaps and diameters.
The LS-9000 can also measure/inspect flat wires. Its rapid sampling speed allows the thrubeam optical micrometer to monitor the width of a flat wire with high precision and detect even the smallest of edge breaks.
When it comes to cladding flat wires, the CL-3000 confocal laser displacement sensor acts as a wire inspection sensor that performs non-contact thickness measurements. It enables 100% wire bond inspection without impacting cycle time while simultaneously enabling high-accuracy measurement of rough or hairline surfaces.
When it comes to multi-strand flat cables, 2D/3D laser profilers (such as the LJ-X8000) are used to inspect the width and shape of flat cables. They can also check for conductor position and the color of individual conductor strands within the cable. These measurement sensors can also be used to profile the outer diameter of a coated cable during extrusion.
Advantages of Wire and Cable Inspection
Using wire inspection sensors brings significant benefits to the entire manufacturing process, primarily by enhancing the overall quality of the product through early defect detection. This prevents defective products from reaching the end consumers to maintain product quality and brand reputation.
Additionally, wire bond inspection sensors increase the overall manufacturing process efficiency by allowing for real-time monitoring and adjustments, which subsequently reduce downtime and material waste. This contributes to sizable reduction costs over time, mostly due to minimized need for post-production corrections and rework.
Discover more about this product.
Click here to book your demo.
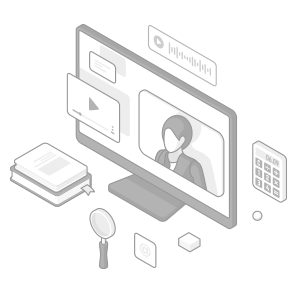
How Wire and Cable Inspection Works
Wire and cable production involves several different production processes, like drawing the wire to a desired diameter and coating it with an insulated material. Some wires have additional shielding, which is applied over their initial insulation coating and before another insulation layer is applied.
The process is only more complex if a cable contains several conductor strands, some of which might require additional shielding with braided copper sheaths and perhaps even steel bands to provide the cable with additional mechanical strength.
Wire inspection sensors are used at each step of the production process to ensure that all products are adequately dimensioned and that the insulating coats are adequately applied. This is mostly done by checking various dimensional measurements to ensure the quality of the product.
Choose KEYENCE Measurement Sensors for Wire and Cable Inspection
KEYENCE is the world’s leading expert in precision technologies and a reliable partner to many wire and cable manufacturers. If you’re looking for highly precise and accurate wire inspection sensors, don’t hesitate to contact KEYENCE and inquire about integrating our products with your production line.
Contact us to learn more about how our advanced technology can help take your business to the next level.
Contact Us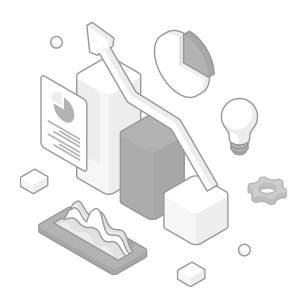
Related Downloads
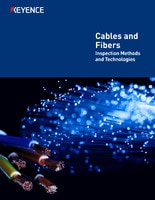
Telecentric measurement systems and thrubeam optical micrometers—which can continuously measure the total length of targets—see heavy use at worksites where cables, fibers, and other long targets are handled. If you work with targets like this, you won’t want to miss the detailed usage examples in this booklet.
Related Products
Applications
Dimension Measurement
- Thickness and Width Measurement
- Step Height Measurement
- Inner and Outer Diameter Measurement
- Measuring Angles
- Meandering/Edge Measurement
Displacement Measurement
- Positioning and Stroke Length Measurement
- Vibration and Runout Measurement
- Deflection Measurement
- Measuring Eccentricity