Key points for stable, trouble-free operations
KEYENCE’s MK-G Series is equipped with three reliable functions for stable operation, reducing problems frequently encountered with continuous inkjet printers. These three fuctions have earned the MK-G Series its favorable reputation when compared to competing products.
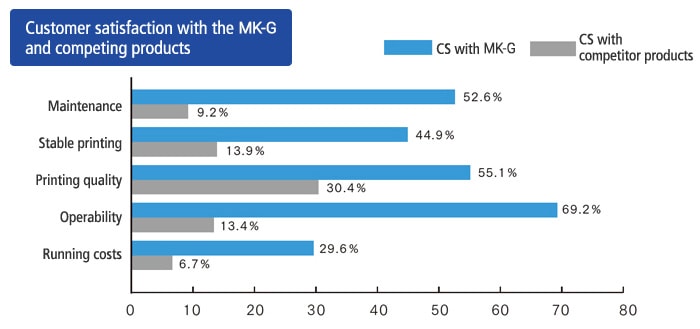
01 Automated maintenance for stable printing
Prevents nozzles from clogging during long breaks
-
World’s first Auto-shower cleaning
Conventional automatic cleaning only used solvent to clean the ink paths. With the newly installed auto-shower function, the MK-G is able to clean the ink path and all the parts that are key to maintaining print quality all at once.
-
-
Conventional automatic cleaning
Only the ink paths are cleaned with solvent. Separate manual cleaning is required for any other dirty parts.
-
Auto-shower cleaning
In addition to cleaning the ink paths, the key parts of the head are also subject to high-pressure cleaning. This eliminates the need for manual cleaning.
-
Resolves printing errors caused by temperature fluctuations
-
Automatic ink particle optimization
The optimum ink particle status for printing is always fluctuating due to the ambient temperature and ink thickness (viscosity).
The MK-G Series senses the ink particles 10 times per second, which enables it to continually maintain the optimum ink particle status.
This maintains perfectly printed text at all times, regardless of the surrounding environment. -
-
Dirt within the print head
-
Unstable text
If the optimum ink particle status is not maintained, the inside of the head becomes dirty and unstable text occurs.
-
Conventional | MK-G Series |
---|---|
It’s necessary to make adjustments for the ink viscosity and temperature of the environment while visually checking the particle status.
- Errors are not noticed until unstable text occurs. - It’s difficult to recognize the optimum status, and making adjustments requires time and effort. |
Ink particles are sensed and adjustments are automatically made to ensure the optimum particle status.
✓ Flawless printed text can always be achieved with minimal time and effort. |
Conditioning tank system
The device is equipped with a specialized tank (the conditioning tank) and a viscosity sensor for use in collecting the solvent after cleaning.
Doing this prevents ink dilution, which stabilizes viscosity and maintains perfect print quality.
-
During automatic cleaning
After automatic cleaning, the solvent is routed directly to the conditioning tank. This alleviates over-dilution of the ink stored in the main tank.
-
During viscosity management
The ink viscosity in the main tank is measured. Based on this reading, solvent is supplied to the main tank from the conditioning tank.
Nothing is wasted because priority is given to the conditioning tank.
Three Main Advantages
- Powerful cleaning
- Cleaning can be performed without concerns regarding ink dilution.
- Dark printed text
- Ensures dark and distinct printed text, a required capability for printers.
- Draining is unnecessary
- Wasteful draining due to ink dilution is prevented. This allows efficient expenditure of consumables.
02 Single cable connection with a vision system
-
Quick response to sudden unstable text
Installation with no unnecessary costs
In order to synchronize a message printed by any inkjet printer with a vision inspection system on a conventional inkjet, a software is required with an additional cost.
With the MK-G Series, these devices can be connected easily with a single cable, which enables printing inspections with no unnecessary costs for creating software. -
Just one cable needed to connect, with no extra costs.
-
Eliminates operator errors
Prevents mistakes when choosing settings
With conventional systems, it was inevitable that inspection mistakes would occur due to incorrect selections when setting the inkjet printer and the vision system separately. When printing settings are switched on the MK-G Series, the inspection settings on the vision system are automatically switched to match, which enables mistake-free inspections.
-
The devices can be connected with a single LAN cable.
When the settings on the inkjet printer are switched, the settings on the vision system are automatically switched to match.
Capture Data Storage
Image data captured using an IV2 Series Vision Sensor can be saved to a USB memory device and retrieved for checking inspection results even after a product has shipped. This is useful for tracing the causes of problems.
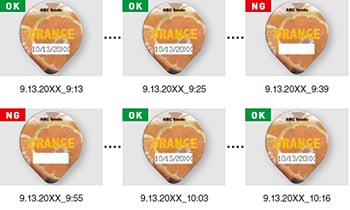
Save captured data to check inspection results for shipped products.
03 Super-adhesive ink for films
No printing omission regardless of packing material
Maintains adhesion with PP and PE films
The adhesive substance in the ink, known as the ink binder, is improved to conform with even polyether resin materials, which were difficult to print on with conventional inks.
Our new ink also features increased adhesion on other materials.
-
Printed text rubs off with conventional inkjet ink
-
Super-adhesive ink stays on firmly