Measurement Sensors
Dimension Measurement
Displacement Measurement
What Is Measurement?
"Measurement" refers to assessing a target's dimensions, such as its size, length, weight, or capacity. While there are numerous terms similar to "measure," including "weigh," "calculate," and "quantify," their usage differs based on the context. Broadly, measurement falls under the umbrella of "instrumentation," representing a specific action within this wider field.
It is also appropriate to say that measurement is done by a worker using a measurement system, and a technician does instrumentation. This website focuses on measurement as it pertains to the design, manufacturing, and inspection process of machine components.
Measurement | Instrumentation |
---|---|
Measurement
|
Instrumentation
|
Difference Between Measurement and Inspection
Measurement involves quantifying results with the aid of tools, while inspection entails comparing these quantified results against established standards to assess a product's acceptability. For instance, when using a ruler to measure length, one can make a decision based on the reading, such as determining if the measured length is slightly over or under the desired amount.
Essentially, this means that based on the measurement obtained with a ruler, the length is marginally longer or shorter than what was intended. Although it's not always necessary to distinguish between these concepts in practice, understanding the difference between measurement and inspection is beneficial.
Discover more about this product.
Click here to book your demo.
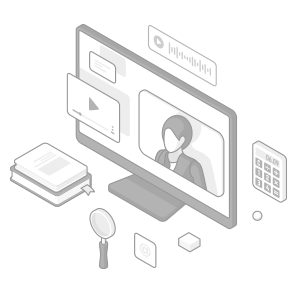
Differences in Measurement Methods
Determining the dimensions of a target can be achieved through direct or indirect measurement methods.
Direct Measurement
Direct measurement involves physically aligning the target with the measurement system to accurately gauge dimensions such as length and height. While this method provides immediate and original results, the accuracy can be influenced by the proficiency of the individual conducting the measurement.
-
1Target
Indirect Measurement
Indirect measurement, for instance, involves utilizing a dial gauge to assess the height discrepancy between a measurement target and a gauge block. This discrepancy is then used to indirectly ascertain the target's height. As this measurement method relies on a reference point, it is also known as "comparative measurement."
-
1Target
-
2Gauge block
We’re here to provide you with more details.
Reach out today!
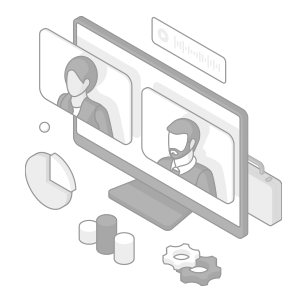
Types of Measurement Techniques
When considering what measurement is, it’s important to understand the technology that brought about different measurement techniques. Each of these techniques has inherent advantages and drawbacks, making them better suited to some applications but ill-suited for others. Here are some of the primary measurement methods employed in today’s industrial landscapes that show why measurement is important.
Electronic Measurement
Electric measurement is the most common measurement type in modern industry. Most industries, including medical and healthcare, depend on electronic measurement for product manufacturing and service delivery.
Electronic measurements, such as the 4-20mA current loop and voltage measurement, are simple, reliable, and can transmit signals over long distances with minimal quality loss.
Physical properties that can be measured using electronic measurements include temperature, pressure, flow rate, pH value, conductivity, humidity, level (both solids and liquids), displacement or position, vibration, and light intensity.
Optical Measurements
Optical measurements use light (visible or otherwise) and various optical components like lenses, mirrors, and photosensitive elements to measure different physical properties. For example, an optical micrometer can provide highly precise measurements of an object’s dimensions by analyzing how the light it emits interacts with the object’s surface.
As such, optical measurements are invaluable in industrial fields that demand high-precision measurement without physical contact, such as semiconductor manufacturing and material science.
Laser Measurements
Laser measurement methods rely on the coherent and monochromatic light emitted by the laser emitter element to measure distances, speeds, and geometries with exceptional precision. Laser profiler systems and laser displacement sensors are at the forefront of these technologies and offer unparalleled precision and accuracy in measuring object profiles and displacement.
These measurement methods derive displacement by measuring the time it takes for the emitted light to reflect off the surface and return to the photosensitive element located inside the sensor head. Likewise, some systems rely on laser triangulation, which detects the change in angle and position at which the light reaches the photosensitive element.
In either case, laser measurement methods are essential in numerous industries due to their accuracy, which often reaches the single-digit µm range—one-thousandth of a millimeter. Laser measurements are most commonly used in automotive manufacturing, aerospace, and construction industries, where even the smallest of inaccuracies can lead to significant consequences.
3D Measurements
3D measurement technologies rely on 3D cameras or 2D laser triangulation to create detailed three-dimensional representations of objects or environments. Using 3D interference measurement sensors, engineers can capture the geometry of complex surfaces with high resolution and high dimensional accuracy.
This measurement method is important for reverse engineering parts and components and for quality control and virtualization of various parts and components to create accurate 3D models required for subsequent analysis.
Curious about our pricing?
Click here to find out more.
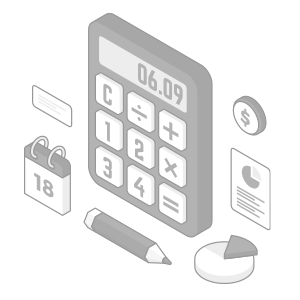
Challenges With Traditional Measurement Methods
Despite technological advancements, contact and non-contact measurement systems have their respective limitations. Manual contact measurement methods performed by an operator can be accurate down to the µm level, but they’re susceptible to human error. That’s why computerized contact measurement methods offer higher accuracy.
Contact measurement methods, while generally accurate, still require physical interaction with the object to make measurements, which can be potentially detrimental to delicate workpieces. Non-contact measurement devices, such as spectral interference displacement sensors, distance sensors, and other measurement sensor types, offer solutions to that particular problem.
They have downsides, such as requiring specialized knowledge, calibration, and added complexity. Nevertheless, their benefits often outweigh these challenges.
Bridging the Gap
KEYENCE, as the world’s leading provider of precision technologies, offers a wide range of precision measurement sensors
for industrial applications that demand accuracy.
If you are looking to upgrade your manufacturing or production process, contact KEYENCE and inquire about potential integration with your production line.
Contact us to learn more about how our advanced technology can help take your business to the next level.
Contact Us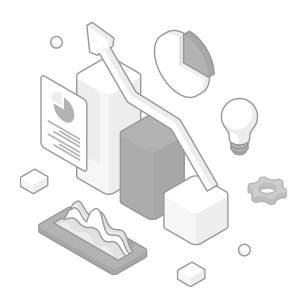
Related Products
Applications
Dimension Measurement
- Thickness and Width Measurement
- Step Height Measurement
- Inner and Outer Diameter Measurement
- Measuring Angles
- Meandering/Edge Measurement
Displacement Measurement
- Positioning and Stroke Length Measurement
- Vibration and Runout Measurement
- Deflection Measurement
- Measuring Eccentricity