Measurement Sensors
Dimension Measurement
Displacement Measurement
Contact vs. Non-Contact Measurement Systems
Choosing between a contact measurement system and a non-contact measurement system may be a challenging task, as you must consider the advantages and drawbacks associated with each system type and factor that into your specific application requirements.
This article explains what to consider when choosing a measurement system. We’ll discuss contact vs non-contact measurement systems, what they are, how they work, some of their less obvious differences, and their specific applications.
What are Contact Measurement Systems?
Contact measurement systems refer to a group of measurement tools and devices that are most used for dimensional measurement. This includes coordinate measuring machines (CMMs), hard probe articulating arms, calipers, micrometers, roundness testers, contracers (contour measuring instruments), gauge blocks, height gauges, and surface plates.
CMMs tend to be some of the most advanced devices in the current market. These devices are computer-controlled and capable of measuring within very tight tolerances, ranging from 2-3 µm for entry-level devices down to 0.3 µm (0.0000118″) for the most advanced models.
CMMs are capable of dimensional measurements in three dimensions, but they’re usually more expensive, space-consuming, and not as easily moved—though they do come in all shapes and sizes. When it comes to actual operation, CMMs tend to be time-consuming because they navigate the inspected part from one point to another using a contact measurement sensor.
Other methods aren’t as advanced and typically include an array of traditional manual tools and equipment, such as calipers, gauge pins, gauge blocks, height gauges, and micrometers.
Unfortunately, these tools are only capable of measuring in one dimension of measurement, except for modern height gauges, which are capable of 2D and limited 3D measurements. We used dimensional measurements in our example but contact measurement systems can measure a wide range of physical phenomena.
This includes vibration, runout, surface texture, flatness, warpage, etc. The choice of measurement system ultimately depends on the physical property being measured, as well as the nature of the sample or part being tested.
We’re here to provide you with more details.
Reach out today!
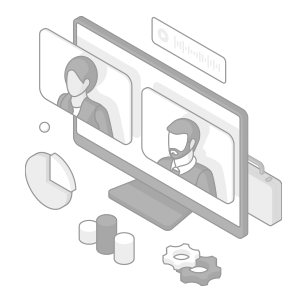
What are Non-Contact Measurement Systems?
Non-contact measurement systems, also known as non-tactile measurement systems, rely on modern non-contact measurement sensors—devices that convert a physical property into a measurable electrical signal—to measure various physical phenomena without actually touching the object being measured.
These systems are particularly important in applications that involve delicate, soft, or extremely hot materials where contact with the object might damage the object or the sensor or alter the measurements in any way.
The physical phenomena measurable using non-contact measurement systems include surface roughness and texture, temperature, vibration and displacement, thickness, color and light properties, fluid flow and airspeed, electromagnetic fields, chemical composition, and dimensions and geometry.
This measurement approach relies on transducer devices such as vision systems, laser scanners, structured light scanners, photogrammetry, and even CT scanners. Some systems rely on optical comparators, also known as profile projectors or shadowgraphs, which are now over a century old. While they don’t produce a digital signal, their outputs can be digitized.
Besides making non-contact measurements, the main benefits of these systems are associated with data collection. They collect and record a large amount of data, all the while not making physical contact with the measured object. They also gather more of the object or part’s surface.
This data collection happens very fast, and some systems feature a refresh rate in the MHz range, allowing non-contact measurement systems to capture data about very complex shapes very quickly—especially if the complex shapes feature multiple axes or various physical features.
However, when it comes to the discussion of contact vs non-contact measurement systems, it’s worth noting that non-contact measurement systems aren’t as accurate as contact measurement systems. The accuracy associated with some of the most advanced models on the market is typically within the single-digit micron range.
Discover more about this product.
Click here to book your demo.
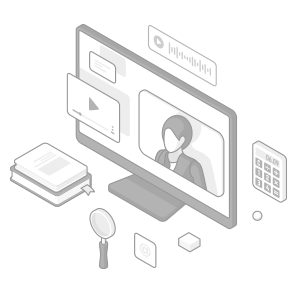
Applications for Contact Measurement Systems
When it comes to contact vs non-contact measurement systems, it’s worth noting that contact measurements relying on tactile probes will typically be more accurate than non-contact measurement methods.
Thus, systems are better suited for applications with high-precision requirements, especially where measurement tolerances are in the micron range. Internal measurements, such as hole diameters or slot width, might also require contact measurement.
Contact measurement systems often provide simpler and more cost-effective measurement solutions for more basic measurement tasks compared to more sophisticated non-contact systems. On top of everything, contact measurement systems are notably less susceptible to environmental interference, which can affect the accuracy of non-contact measurements.
Applications for Non-Contact Measurement Systems
Unlike contact measurement systems, non-contact measurement systems excel at dimensional measurements and profiling of fragile, soft, or elastic material that would be easily damaged or deformed by tools.
They’re not as accurate as high accuracy contact measurement systems, which is why they’re best suited for applications that prioritize precise measurements of objects with complex geometries, as well as rapid measurements and large-volume inspections of dynamic or moving objects.
This includes measuring properties of machinery in motion without affecting their operation or for rapid measurement and scanning of large volumes of manufactured parts, which is rather beneficial in mass production manufacturing.
Real-time monitoring and feedback are among the most useful applications for non-contact measuring systems, as they can detect various defects in mass production, provide feedback, and trigger adequate action in automated processes and control systems.
Implementing KEYENCE Contact or Non-Contact Measurement Systems
Hopefully, this guide has given you more insight into the contact vs non-contact measurement systems debate and which system might better suit your particular application. However, it’s also worth noting that there’s no one-size-fits-all in measurement, and sometimes, you might have to resort to a combination of tools paired with the sharpness of the mind to measure certain things.
If you want to learn more about measurement sensors, don’t hesitate to contact KEYENCE—the world’s industry leader in factory automation solutions.
Contact us to learn more about how our advanced technology can help take your business to the next level.
Contact Us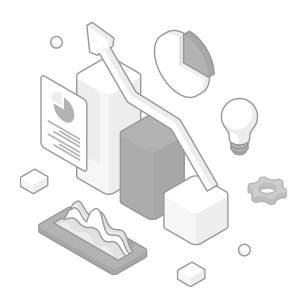
Related Downloads
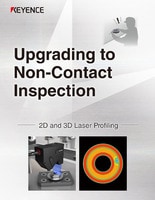
Conventional contact-type measuring systems and camera-based inspection have known issues. This guide uses different processes and target objects as examples to detail how laser profilers can solve these issues with non-contact 3D measurement. This is a perfect introductory guidebook for users new to laser profilers.
Related Products
Applications
Dimension Measurement
- Thickness and Width Measurement
- Step Height Measurement
- Inner and Outer Diameter Measurement
- Measuring Angles
- Meandering/Edge Measurement
Displacement Measurement
- Positioning and Stroke Length Measurement
- Vibration and Runout Measurement
- Deflection Measurement
- Measuring Eccentricity