Measurement Sensors
Dimension Measurement
Displacement Measurement
Tolerance and Measurement Accuracy
Explore tolerance and measurement accuracy in our blog. Learn about the significance of tolerance in manufacturing and factors affecting measurement accuracy.
What is Tolerance?
Tolerance refers to the total allowable error within an item. This is typically represented as a +/- value off of a nominal specification. Products can become deformed due to changes in temperature and humidity, which lead to material expansion and contraction, or due to improper feedback from a process control device. As such, it's necessary to consider errors about design values in the manufacturing and inspection processes. If these errors cannot be tolerated, most products will be deemed unacceptable. In this way, tolerance is meant to be used when setting the acceptable error range (the range within which quality can still be maintained) based on the design value with the assumption that variation will occur at any given step.
What is Measurement Accuracy?
Accuracy represents a measurement's degree of correctness. Accuracy can be used in such expressions as, “This measurement system offers a high degree of accuracy, so it can be assumed that the expected measurement results can be obtained,” or, “The accuracy of the measurement system has decreased; calibration may be required.” When applied to the measurement process, accuracy is referred to as measurement accuracy. The accuracy of the measurement equipment can be used as an indicator to determine how accurate the results will be. Measurement systems with higher measurement accuracy can perform measurements more accurately.
We’re here to provide you with more details.
Reach out today!
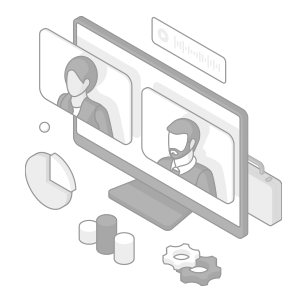
How Tolerance and Measurement Accuracy Affect Each Other
When manufacturing a cylinder with a length of 50 mm and a tolerance of ±0.1 mm (acceptable range: 49.9 mm to 50.1 mm), inspection with a measurement system is assumed to be as follows.
- Measurement system A: Accuracy ±0.001 mm
- Measurement system B: Accuracy ±0.01 mm
- Measurement system C: Accuracy ±0.03 mm
According to the above, the acceptable range for each measurement system will be as follows.
As shown bellow, measurement systems with higher accuracy are capable of obtaining more accurate results.
In addition, increased measurement accuracy makes it possible to reduce the number of products with acceptable tolerances judged mistakenly as unacceptable.
Reference product: 50 mm, tolerance: ±0.1 mm
- Measurement system A: 49.901 mm to 50.099 mm
- Measurement system B: 49.910 mm to 50.090 mm
- Measurement system C: 49.930 mm to 50.070 mm
Discover more about this product.
Click here to book your demo.
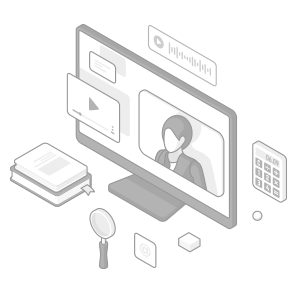
Significance of Tolerance in Measurements
Tolerance is simply a measurement in engineering and manufacturing that represents a degree to which the physical dimension of a product can vary without affecting its functionality. It can be thought of as wiggle room engineers allow when designing and producing parts to ensure part and component interchangeability.
As such, the significance of tolerance in measurements can’t be overstated; it determines how well the parts fit and interface with one another, how well they operate, and how well they endure constant use. Tolerance in measurements also ensures that the products are reliable, safe, and can be produced at reasonable costs.
Parts and components produced without properly defined tolerances may not fit together or interface with each other as intended. This could lead to incorrect operation, further leading to failures in assemblies and costly reworks associated with incorrectly defined tolerances in parts and components manufacturing.
Types of Tolerance
Tolerance in measurements is broadly categorized into several different types, including dimensional, geometric, and positional tolerances.
Below are the definitions of each type:
- Dimensional Tolerance
- As the name implies, these tolerances specify the limits of allowed variation for physical dimensions.
- Geometric Tolerance
- These define the tolerances of geometric shapes, ensuring that the part’s geometry doesn’t deviate significantly from the specified dimensions or allowed limits.
- Positional Tolerance
- These tolerances relate to the locations of features on a specific part or component. It ensures that holes, slots, and other features are positioned correctly relative to each other.
Each of the aforementioned types of tolerance in measurements ensures that parts and assemblies function as intended by the designer, which underlines the importance of precision and dimensional accuracy in modern engineering and manufacturing—and other industries as well.
Curious about our pricing?
Click here to find out more.
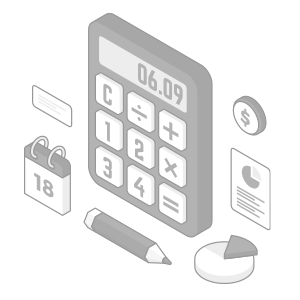
Factors Affecting Measurement Accuracy
Tolerance and measurement accuracy are usually affected by various factors, including the type of measurement sensors
used to conduct tolerance measurements, environmental conditions in which measurements are conducted, and measurement methodology.
Different types of tolerance measurement sensors, such as laser displacement sensors, optical micrometers, and distance sensors, each have their respective advantages and limitations that can affect measurement accuracy. For example, laser profilers might offer higher accuracy in measuring surface profiles, while 3D interference measurement sensors excel at capturing precise dimensions and complex geometries.
Furthermore, measurement methods, like using a contact or non-contact measurement system, also affect tolerance and measurement accuracy, with non-contact measurement devices, such as spectral interference displacement sensors, being a better choice for certain applications.
Challenges and Limitations in Maintaining Measurement Accuracy
Maintaining high tolerance and measurement accuracy isn’t without its challenges, most of which are associated with the inherent limitations of measuring devices. For example, contact measurement sensors can damage fragile workpieces and bend flexible ones, leading to damage or inaccurate dimensional readings. However, even non-contact measurement methods have their unique drawbacks, as these systems often struggle with transparent or highly reflective materials.
Laser displacement sensors are great for high-precision distance measurements, but their effectiveness can be compromised by the reflection of absorptive surfaces. Similarly, optical micrometers can provide accurate readings down to a single-digit µm range but are difficult to position in constricted spaces.
So, when choosing an adequate measurement device and method, several factors must be considered, such as the device and space specifications, the type of workpiece material, and the desired accuracy level.
Measurement Accuracy Solutions
To overcome these challenges, KEYENCE, the world’s leading provider of precision technologies, continuously develops and implements innovative solutions. If you’re looking to upgrade the tolerance and measurement accuracy of your manufacturing or production processes, don’t hesitate to contact KEYENCE. Our experienced representatives will answer any inquiries you might have regarding the integration of KEYENCE equipment into your current manufacturing lineup.
Contact us to learn more about how our advanced technology can help take your business to the next level.
Contact Us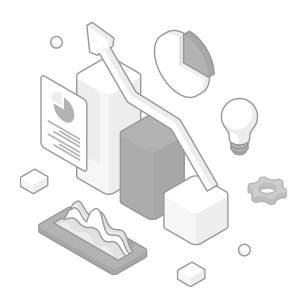
Related Products
Applications
Dimension Measurement
- Thickness and Width Measurement
- Step Height Measurement
- Inner and Outer Diameter Measurement
- Measuring Angles
- Meandering/Edge Measurement
Displacement Measurement
- Positioning and Stroke Length Measurement
- Vibration and Runout Measurement
- Deflection Measurement
- Measuring Eccentricity