CMM (Coordinate Measuring Machine)
What is Reverse Engineering and Why is it Important?
We can credit reverse engineering for booming innovation and competition across industries. The process is now more than just disassembling and reassembling like it was in the past. It now includes software, 3D printing, and advanced measurement systems. Reverse engineering is used in everything from software to pharmaceuticals to manufacturing and is pivotal in modern engineering.
The reverse engineer process, with help from software, has offered modern advancements that deliver a more streamlined and efficient approach.
Traditionally, working backward through a design was a challenging and time-consuming process. Nowadays, the steps of reverse engineering have been simplified with the help of portable CMMs and similar machines. Even in light of emerging measurement technologies, the effectiveness of the practice is dependent on several factors.
In this blog, we’ll explore the integration of reverse engineering in the manufacturing industry and the role it continues to play.
What is Reverse Engineering?
Put simply, reverse engineering is taking something apart to determine exactly how it was made without having a blueprint to follow, or to derive or duplicate the design, technical specifications, manufacturing methods, or functionality of an object by studying an existing product, prototype, etc. Reverse engineering is the opposite of conventional engineering—instead of designing first and then building the product, reverse engineering collects a product and builds a design based on its dimensions and GD&T features.
Contact us to learn more about how our advanced technology can help take your business to the next level.
Contact Us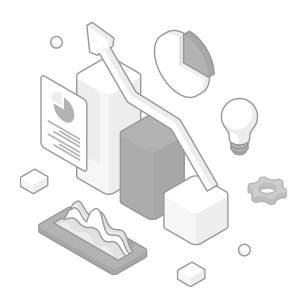
Why is Reverse Engineering Important?
Reverse engineering leads industries to produce the best products because it increases competition. The cycle goes on as engineers continuously try to be the next best version.
The boost of being the next-best is valuable for industries like the medical industry. With reverse engineering pushing engineers to manufacture the next best orthopedic and orthodontic devices, the industry rapidly evolves and gives the best devices for patient care.
The aerospace industry is another industry that has significantly evolved because of reverse engineering. Engineers are competing to make the most durable, safe, and high-functioning aircraft components—increasing aircraft safety and efficiency by the day.
The practice benefits consumers, and it also benefits companies, too. The constant innovations drive companies into success and an evolving market. Reverse engineering at a company’s disposal means that there are growth opportunities for any competitor product.
We’re here to provide you with more details.
Reach out today!
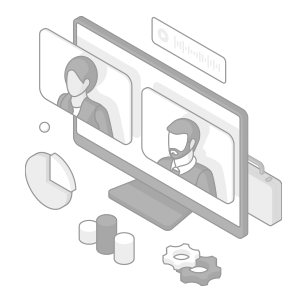
How to Reverse Engineer
The reverse engineering definition is simple, but the process is more complex—it’s not just taking something apart and looking at its components. There are three steps to the reverse engineering process.
- 1. Information extraction. This step is when engineers collect surface and GD&T feature data. If using an advanced scanning or coordinate system, the result is a point cloud—which is a 3D coordinate dataset.
- 2. Modeling. Once the engineers collect surface and GD&T feature data, the point cloud is converted into a CAD model or the dimensional measurements are drawn in a DXF, STP, or IGES file.
- 3. Review. In the last step, engineers convert the model into a 3D product and test its usability.
Within this process, it’s normal for repeated iterations of each step before the final product is released.
Discover more about this product.
Click here to book your demo.
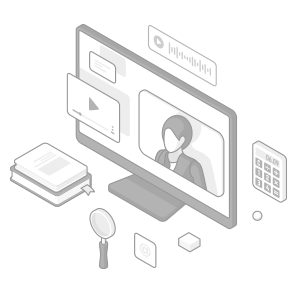
Applications of Reverse Engineering in Manufacturing Processes
Thanks to new practices and different types of CMM machines, reverse engineering applications have expanded quite a bit in manufacturing.
Common reverse engineering examples in manufacturing include:
- Creating data to effectively replace legacy parts that other manufacturers don't create anymore.
- Help with failure analysis and determining why another part or machine broke down or failed in its processes.
- Trial and error can offer insight into how a product or part can be improved.
- In some cases, the reverse engineering process is a necessity for repairing specific parts or other machines.
Reverse engineering tools like handheld probe coordinate measuring machines make the task much simpler and more user-friendly. Professional engineers are a vital necessity, but newer measurement systems have simplified the learning curve. The upside to a simple handheld CMM is that it easily outpaces the capabilities of traditional methods.
Curious about our pricing?
Click here to find out more.
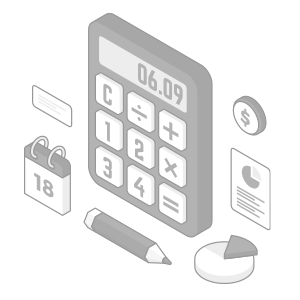
Benefits of Implementing Reverse Engineering Process
Depending on how reverse engineering examples are applied, manufacturers can reap several benefits. The bullet points below offer a comprehensive answer to the question: What is reverse engineering?
- It can help to address weak points in intellectual property.
- Offers a separate look at how something might need to be repaired.
- Helps lead to products that offer more interoperability across other components and systems.
- It can add to cost reduction as it helps to avoid creating new components entirely from scratch.
- There will always be a competitive advantage involved with utilizing the process to enhance products and develop new ones.
Although the term is commonly used from a bird's-eye view, it is essential to understand that there are several types of reverse engineering as well.
Contact us to learn more about how our advanced technology can help take your business to the next level.
Contact Us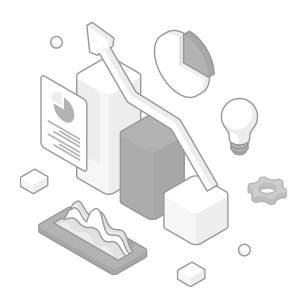
Different Types of Reverse Engineering
When reverse engineering, engineers follow two popular processes: drawings and scanning. Both of these methods use CAD models for the prototyping process but differ in how the CAD model is created.
Point Cloud
Technology like scanners and CMMs collect data using a laser, lights, or a contact probe. When engineers collect data, these devices create basic geometry and point clouds. The point cloud is then put into software, which turns into a CAD model. Engineers then use CAD files like DXF, STP, or IGES to evolve the model further.
Using scanning for the reverse engineering process is a popular choice for collecting data efficiently and producing accurate CAD models. Scanning tools cut out tedious measurement processes and simultaneously collect thousands of data points. These tools are especially useful for keeping up in quickly moving industries and collecting complex measurement data.
Drawing
Drawing also uses CAD models, but it follows a different process than scanning.
Engineers collect measurement points with devices that don’t automatically transition those measurements into a point cloud and then model. Instead, the measurements are collected and analyzed by engineers and then drawn in CAD files like DXF, STP, and IGES.
We’re here to provide you with more details.
Reach out today!
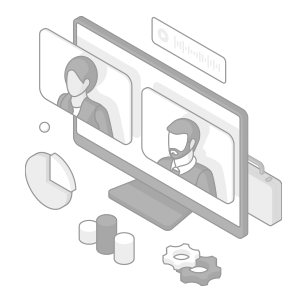
CAD Files With Reverse Engineering
CAD files are an integral part of reverse engineering. Using these makes it much easier for engineers to follow modeling without 2D distortion.
Engineers upload data into CAD files, which then create a 3D wireframe. Engineers use the wireframe to expand upon the original model. These files are manipulated with drawings, printing, and modeling.
Discover more about this product.
Click here to book your demo.
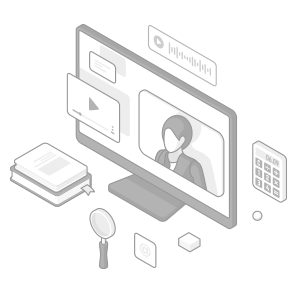
DXF vs. STP vs. IGES CAD Files
Out of these three CAD files, there are differences in how they store data and how engineers access it. Let’s get into the specifications.
DXF
DXF files, or Drawing Exchange Format or Drawing Interchange Format, are a type of CAD data file used for sharing 2D drawing data or text-based formats. This file is the most collaborative type of CAD file; it’s an open format, so multiple engineers can simultaneously work on it. The collaborative design is adjustable to all CAD applications. Beyond its ease of collaboration, DXF files are known for producing accurate designs without distortion from the measured object.
STP
STP files—also called STEP—were developed by the International Organization for Standardization (ISO) to standardize file sharing across software programs. This file saves detailed body information about 3D models. Because of the advanced model data, it is used for 3D modeling and 3D printing. Engineers can easily share this data collaboratively for building new model designs.
IGES
IGES files—Initial Graphics Exchange files—are CAD files for blueprints and drafting. This file is used for engineering drawings like wireframes, models, and circuit diagrams. These drawings are then used for planning and pricing design construction. IGES files are not as advanced as STP and DXF files, but they are still widely used.
We’re here to provide you with more details.
Reach out today!
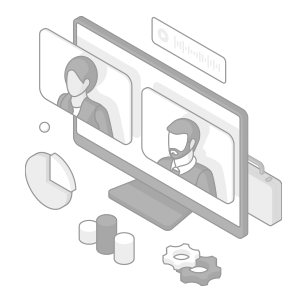
Common Challenges Faced in Reverse Engineering
The use cases for reverse engineering in manufacturing are extensive, and legal and ethical considerations are frequently involved. Companies have used the practice to steal technology and trade secrets for their own gain, which is why numerous countries have strict regulations.
The scope of these details varies around the world, but there are two main things to consider in the U.S. before attempting to reverse engineer a product. In general, this process is allowed under the Defend Trade Secrets Act (DTSA).
- It is legal if the original version is legally obtained. Improper means include theft, bribery, and misrepresentation.
- It is legal if no contractual agreements are violated.
Of course, the topic goes much deeper. In general, ethical applications of reverse engineering are permitted in the U.S. to improve products or achieve interoperability with previously incompatible products.
Discover more about this product.
Click here to book your demo.
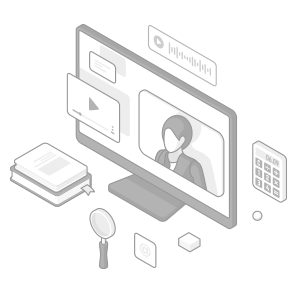
The Future of Reverse Engineering
Reverse engineering is rapidly adapting and changing. New innovations are continuous, and engineers have millions of opportunities to recreate products in a more cost-effective, usable, and advanced way. The weight of opportunity is inspiring but also daunting when businesses feel like they can’t keep up with new technologies. Luckily, leading systems and machinery can make this process easier and more cost-effective to implement.
At KEYENCE, we offer coordinate measurement machines, the XM and the WM Series, that collect measurement data in an instant. These machines create data point clouds similar to the scanning method of reverse engineering.
The XM and WM touch probe CMMs are handheld and require virtually no training to use. With the press of a button, these devices collect GD&T data points in seconds, create point clouds from free-form capture, and export DXF, STP, and IGES files. These files then turn into full 3D models in CAD software.
With KEYENCE’s CMMs, you’ll have the tools to become a reverse engineering leader with industry-proven equipment. Contact us today to get your hands on a CMM or to discuss your reverse engineering needs.
Contact us to learn more about how our advanced technology can help take your business to the next level.
Contact Us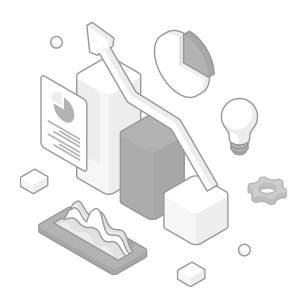
Related Downloads
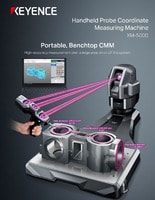
Brochure for the XM-5000 Series Handheld CMM. Portable CMM to easily and accurately measure 3D and GD&T features anywhere including the shop floor and in the machine tool.
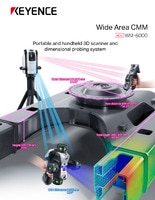
Brochure for the WM-6000 series Wide-Area CMM. A portable setup with a wireless handheld probe that enables users measure large parts and equipment.