Measurement Sensors
Dimension Measurement
Displacement Measurement
What are Displacement Sensors (Displacement Gauges) and Dimension Measurement Systems?
A displacement sensor (displacement gauge) is used to measure travel range between where an object is and a reference position. Displacement sensors can be used for dimension measurement to determine an object's height, thickness, and width in addition to travel range. Selecting the most appropriate equipment according to the application, required accuracy, and usage environment is necessary. Measurements with displacement sensors can be classified into two large categories: non-contact measurement using light or magnetic fields / sound waves, or contact measurement performed in direct contact with the target.
The principles and features for each method are as follows.
Item | Non-contact type | Contact type | |||
---|---|---|---|---|---|
Optical type | Eddy current type | Ultrasonic type | Laser focus method | ||
Detection targets | Most targets | Metal | Most targets | Most targets | Solid |
Measurement distance | Normal | Short | Long | Short | Short |
Accuracy | High | High | Low | High | High |
Response speed | Fast | Fast | Slow | Normal | Slow |
Dust, water, oil, etc. | Normal | Strong | Normal | Normal | Strong |
Measurement surface | Small | Normal | Large | Small | Small |
Scroll
We’re here to provide you with more details.
Reach out today!
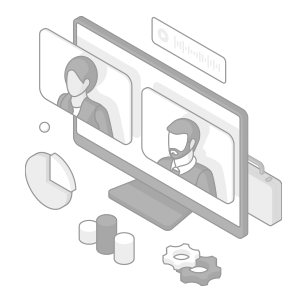
Various Applications
Displacement sensors (displacement gauges) are used for a wide range of purposes. Below are a few examples.
Intent | Example |
---|---|
Thickness | Measuring whether the thickness of rolled steel sheets is uniform, whether the thickness of laminated glass is within the standards, etc. |
Height and step | Measuring whether the height of aligned PCBs is uniform, and whether unusual steps on chips assembled on the PCBs are present. |
Outer diameter | Measuring the outer diameter of mass-produced cylindrical components to determine whether the components are acceptable or not. |
Warpage and Flatness | Measuring whether a glass substrate is warped, whether a polished metal component is flat, etc. |
Stroke and positioning | Measuring the stroke amount of a camera module, whether the target has arrived in the correct position within the processing equipment, etc. |
3D Shape | In addition to checking components for warpage, measuring for warpage in all directions on a flat surface rather than just one line. |
Scroll
Reflective Models Photoelectric/proximity switch
Preasent
Not preasent
Reflective Models Displacement sensor
Small
Large
Far
Close
Thrubeam Model Photoelectric/proximity switch
Preasent
Not preasent
Thrubeam Model Displacement sensor
Small
Large
Placed in center
Placed near top
Discover more about this product.
Click here to book your demo.
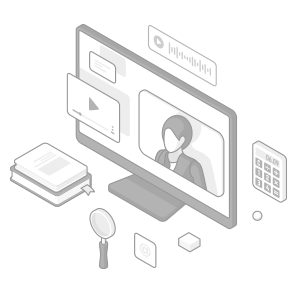
Types of Laser Displacement Sensors
There are several types of displacement sensors; most sensors cover a broad range of applications, while others are more specialized.
For example, inductive displacement sensors detect changes in electromagnetic fields they emit each time they come in close proximity to a metallic object.
Contact displacement sensors measure the contact probe's displacement and position by using light, CMOS sensors, and encoders.
Laser displacement sensors are incredibly versatile, as they can measure displacement (and various derivative measurements) across a variety of different materials… including transparent ones.
Laser profilers measure displacement or height using a laser line to determine a 2D/3D profile of an object's surface.
Common laser profilers include the following:
- Triangulation sensors
- These measure displacement based on the angle of the reflected laser beam.
- Time-of-flight sensors
- These sensors measure displacement by calculating the time it takes for a laser beam to travel back to and back from the target.
- Confocal sensors
- These measure the intensity of reflected light to calculate displacement.
How do Laser Displacement Sensors Work?
How is displacement measured? Laser displacement gauges work by emitting a laser beam onto a target surface and calculating the appropriate metrics depending on the sensor type. Laser triangulation displacement sensors work by detecting the angle of the reflected light, which is then analyzed and used to calculate displacement.
Time-of-flight laser displacement gauges, as their name implies, calculate the time it takes for light to return from the moment it’s been emitted toward the target, using the speed of light to calculate distance. Confocal sensors, however, analyze the wavelength of the reflected light, which varies with distance, to determine displacement.
All these methods, though offering similar results with an exceptionally high level of accuracy, differ in their working principles and, thus, in their applications across numerous industries.
Curious about our pricing?
Click here to find out more.
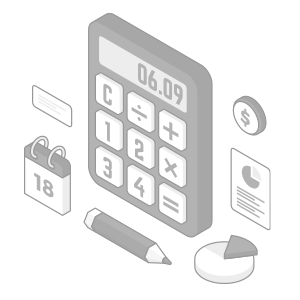
Units of Displacement Measurement
The units of displacement measurement also depend on the application and the level of precision a specific application requires. For general industrial applications, millimeters or inches are the most common displacement measurement units employed.
However, extremely precise measurements—such as the positioning of components in the semiconductor industry—might require measurements in the micrometer or even nanometer range.
Ultimately, the unit of measurement is a critical factor to consider when selecting a laser displacement sensor, as it directly affects the sensor’s adequacy.
How are Laser Displacement Sensors Used?
As stated above, laser displacement sensors are found in a wide range of industrial applications thanks to their accuracy, which is often in the single-digit µm range, their reliability, and their non-contact nature, which allows them to precisely measure even the most fragile of objects.
These sensors are most commonly used in the automotive industry for quality control, ensuring that components and applications are manufactured precisely and within specified tolerances. In electronics manufacturing, these sensors are often used to measure wafer thickness and component placement.
Laser displacement gauges are also used in robotics for precise positioning, in material handling systems to measure and detect objects, and in construction for monitoring structural displacements. The broad scope of their applications across various industries only attests to the versatility of laser displacement gauges and their importance when conducting precise displacement measurements.
KEYENCE offers a comprehensive range of different displacement measurement sensors. If you want to learn more, contact us today. We have plenty of resources to help you choose the best possible integration for your current production and dimension measurement system.
Contact us to learn more about how our advanced technology can help take your business to the next level.
Contact Us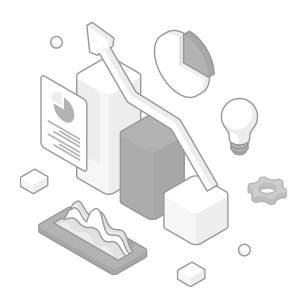
Related Downloads
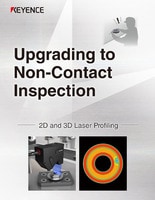
Conventional contact-type measuring systems and camera-based inspection have known issues. This guide uses different processes and target objects as examples to detail how laser profilers can solve these issues with non-contact 3D measurement. This is a perfect introductory guidebook for users new to laser profilers.
Related Products
Applications
Dimension Measurement
- Thickness and Width Measurement
- Step Height Measurement
- Inner and Outer Diameter Measurement
- Measuring Angles
- Meandering/Edge Measurement
Displacement Measurement
- Positioning and Stroke Length Measurement
- Vibration and Runout Measurement
- Deflection Measurement
- Measuring Eccentricity