Measurement Sensors
Dimension Measurement
Displacement Measurement
Laser Snapshot Sensors vs. Laser Profilers: How Are They Different?
3D laser sensors play a vital role in modern industrial automation processes. Two variations of these sensors — laser snapshot sensors and laser profilers — can both capture measurements accurately and ensure product tolerances. However, they differ in principle and application.
This guide will explore the key differences between the two sensors and provide full details on how they both work. This will help you determine which sensor to choose for your specific needs and make the correct choice.
What Are Laser Snapshot Sensors and Laser Profilers?
Laser Snapshot Sensors
Laser snapshot sensors perform high-speed, high-accuracy 3D inspections on stationary targets. These sensors are self-contained, meaning no additional lighting/encoders/lenses are needed to capture a 3D image.
Laser snapshot sensors work by sweeping a laser line across an object’s surface. The sensor captures reflected light and uses it to reconstruct a 3D image. As a result, these sensors can measure width, height, area and volume.
Laser Profilers
Laser profilers capture 2D cross-sectional profiles of an object. They are often used for edge detection, thickness measurements, surface flatness verification, and so on. By scanning a part in motion, a laser profiler can stitch together 2D lines to create a complete 3D model.
Laser profilers function by emitting a laser line onto an object’s surface. When the sensor detects how the line bends or interacts with the object, the deformation is translated into a 2D cross-sectional profile. To scan an entire object, the laser profiler must be moved across the object or the object must pass under the laser sensor.
We’re here to provide you with more details.
Reach out today!
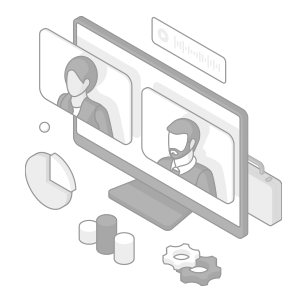
Key Differences Between Laser Snapshot Sensors and Laser Profilers
When it comes to deciding between a laser snapshot sensor or laser profiler, several critical factors come into play. Once you understand how each works and fits into your production line, you can make informed decisions.
1. Movement
Laser snapshot sensors don’t require any movement to take a 3D scan. Laser profilers must have some sort of movement (either of the sensor or the part) to create a 3D image.
2. Part/Inspection Size
Laser profilers have larger FOVs than laser snapshot sensors. This is important when the inspection region is large or if you want to monitor extruded parts.
3. Integration
Laser snapshot sensors are standalone systems, so immediate inspection is possible without the need for any additional equipment. Laser profilers need peripherals in order to take 3D scans.
4. Accuracy
An added benefit to being standalone is improved accuracy. Snapshot sensors tend to be more accurate than laser profilers.
This is because the additional equipment needed for laser profilers reduce the accuracy of the overall setup.
Common Applications for Laser Snapshot Sensors and Laser Profilers
Laser Snapshot Sensor Applications
- Connector terminal coplanarity
- Weld bead shape inspection
- Flatness inspection
- IC chip seating and orientation checks
Laser Profiler Applications
- Flush/Gap measurements
- Tire shape / DOT code inspection
- Weld seam tracking
- Food volume measurements
Conclusion
Choosing between laser snapshot sensors and laser profilers depends on the specific requirements of your application. For complete 3D inspections on stationary targets, laser snapshot sensors are your best bet. In contrast, laser profilers offer highly detailed 2D/3D measurements that are perfect for dimensional analysis and surface profiling.
For more detailed information on how to choose the right measurement system for your needs, check out KEYENCE’s guide to measurement sensors.
Contact us to learn more about how our advanced technology can help take your business to the next level.
Contact Us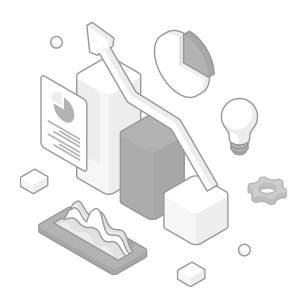
Related Products
Applications
Dimension Measurement
- Thickness and Width Measurement
- Step Height Measurement
- Inner and Outer Diameter Measurement
- Measuring Angles
- Meandering/Edge Measurement
Displacement Measurement
- Positioning and Stroke Length Measurement
- Vibration and Runout Measurement
- Deflection Measurement
- Measuring Eccentricity