Measurement Sensors
Dimension Measurement
Displacement Measurement
Inline vs. Offline Measurements
Inline measurement and offline measurement refer to different methods of measurement. Inline measurement can also be referred to as “automatic measurement,” and offline measurement can also be referred to as “manual measurement.” The difference boils down to whether measurements are performed as part of the manufacturing line (inline) or separate from the line (offline).
Inline Measurement
A structure that includes a sensor mounted along a manufacturing line to constantly monitor products passing underneath would be an example of inline measurement.
Incorporation of the below steps into a manufacturing line enables automatic inspection of mass-produced components.
- Registration of shapes and dimensions (with a tolerance range) for judging product acceptability
- Measurement when a target passes underneath the sensor
- Acceptability judgment
- Output of NG judgment when a product has been determined as unacceptable
Inline Measurement Characteristics
A structure that includes a sensor mounted along a manufacturing line to constantly monitor products passing underneath would be an example of inline measurement.
Incorporation of the above steps into a manufacturing line enables automatic inspection of mass-produced components.
We’re here to provide you with more details.
Reach out today!
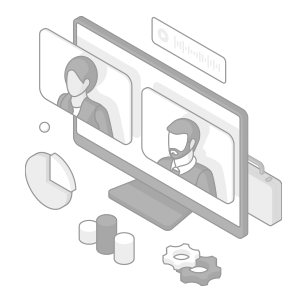
Offline Measurement and Relevant Features
Offline measurement is measurement performed through the manual manipulation of the measurement system in order to obtain measurements for any given point.
While measuring instruments such as vernier calipers and micrometers do allow for measurement at any arbitrary point, measurement results may vary depending on the experience and skill of the person measuring. In addition, because constant monitoring is not performed, it is impossible to determine when unacceptable products began to occur from the statistical data. Determining how often measurements will be performed is an important factor in obtaining stable test results with offline measurement.
Importance of Inline/Offline Measurement in Manufacturing and Quality Control
The importance of inline and offline measurements in manufacturing and quality control can’t be overstated.
These measurement methodologies are fundamental in maintaining high-quality standards and ensuring the efficiency of production processes.
Here’s why they’re important:
- Quality Assurance
- Both inline and offline measurement sensors are essential in quality assurance, enabling manufacturers to verify that their products meet all the specifications and regulatory requirements before reaching the market.
- Process Optimization
- By identifying deviations and defects early in the production process, inline measurement systems allow for immediate corrections. This optimizes the production process and minimizes waste, rework costs, and downtime. Likewise, offline measurement sensors provide detailed insights into product quality after the production cycle, offering data that can be used for further optimization of the production process.
- Cost Reduction
- Effective use of different measurement techniques and technologies can significantly reduce the costs associated with scrap, rework, and warranty claims. By catching defects early in production (inline) or ensuring the quality of the final product (offline), businesses stand to save considerable resources.
- Customer Satisfaction
- The consistent output of quality production facilitated by inline and offline measurements helps build customer satisfaction, trust, and loyalty. These measurement techniques are crucial in achieving consistency and thus provide a clear link between the manufacturing process and customer satisfaction.
- Compliance
- Many industrial branches are governed and regulated by strict standards, laws, and regulations, which dictate product quality and product safety. Both inline and offline measurement sensors ensure compliance with these regulations, avoiding costly penalties and product recalls.
Curious about our pricing?
Click here to find out more.
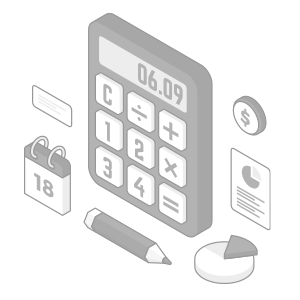
Inline Measurement Examples
Inline measurement systems are often used in various industries to automatically assess dimensional properties, position, or presence/absence of products during production or assembly.
Some common measurement examples include:
- Measuring Lead Frame Dimensions
- Shaft Diameter and Foreign Particle Detection
- Measurement of Needle Tips
- Tool Runout/Positioning
- Multi-Point Measurement of Battery Outer Diameter
- Thickness Measurement after Roll Pressing
As previously stated, inline measurement systems detect defects and deviations during the production process. Thus, they prevent defective products from going further in the production process and offer insight into potential problems with the production process itself, which might require immediate action or preventative maintenance.
Offline Measurement Examples
Offline measurements are more associated with quality control than quality assurance since they rely on measuring finished products. A good example is measuring the thickness of a batch of metal sheets with a micrometer or using calipers to check the diameter of plastic pipes in a batch following their production to ensure that the end results match the design specifications.
Discover more about this product.
Click here to book your demo.
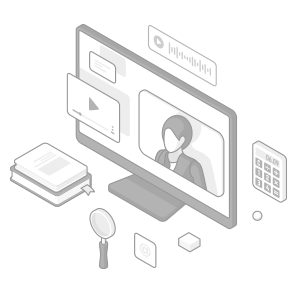
Advantages of Inline Measurements vs. Offline Measurements
Inline measurements offer significant advantages over their offline counterparts, particularly when it comes to efficiency and the ability to enhance quality control processes.
These advantages include:
- Enhanced Inspection Efficiency
- Installing inline inspection sensors, such as KEYENCE’s TM-X5000 Series, enables 100% inline inspections while shortening the time needed for measurement. This also includes near-line measurements and enhances the efficiency of the entire inspection process.
- Eliminate Operator Errors
- Offline measurements imply the use of manual tools, such as micrometers and calipers, by human operators. However, humans are more prone to errors that lead to inadequate control. Inline measurements eliminate operator intervention and provide uniform measurement results with an exceptionally high degree of repeatability.
- Prevent Damage to Targets
- One of the main advantages of relying on inline measurements, like KEYENCE’s TM-X5000 or LS-9000 Series, lies in their non-contact measurement methodology. These sensors don’t make physical contact with the measured object and, thus, have no chance of affecting the product in any way
Are you ready to enhance your inspection process with the latest inline measurement technology? Contact KEYENCE today to learn more about our TM-X5000 and LS-9000 Series and how they can benefit your production line.
Contact us to learn more about how our advanced technology can help take your business to the next level.
Contact Us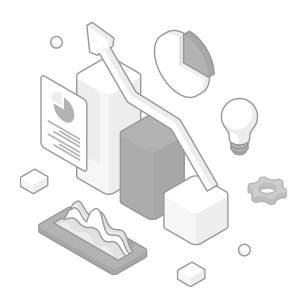
Related Products
Applications
Dimension Measurement
- Thickness and Width Measurement
- Step Height Measurement
- Inner and Outer Diameter Measurement
- Measuring Angles
- Meandering/Edge Measurement
Displacement Measurement
- Positioning and Stroke Length Measurement
- Vibration and Runout Measurement
- Deflection Measurement
- Measuring Eccentricity