Measurement Sensors
Dimension Measurement
Displacement Measurement
3D Laser Snapshot Sensors vs. Vision Systems: How Do They Compare?
To achieve the highest production standards possible, manufacturers need the help of automated inspection systems. Human efforts and manual inspection methods aren't sufficient for today's digitally and technologically advanced operations.
3D laser snapshot sensors and vision systems are both measurement and inspection technologies used to capture and analyze visual information.
However, both operate on distinct principles and have different strengths and unique applications. Let's go through the key features, comparisons, applications, and selection criteria for 3D laser snapshot sensors and vision systems.
Introduction to 3D Laser Snapshot Sensors and Vision Systems
3D laser snapshot sensors project a laser line onto a target and triangulate the reflected light to determine distance and depth. By sweeping the line across a part, multiple points of data are combined together into a detailed 3D image. Once the sensor has taken an image, it can then compare it against known tolerances to identify defects.
On the other hand, vision systems utilize industrial cameras, optics, lighting, and software algorithms for automated visual inspections. They employ pattern recognition to classify and verify objects. They often require a projector or lighting unit to capture accurate images.
Primarily 2D-based, vision systems capture surface appearance data, which can be limiting in complex environments where depth is essential. While some newer systems can capture basic 3D data, they mainly focus on 2D inspections for tasks like defect detection and code reading.
We’re here to provide you with more details.
Reach out today!
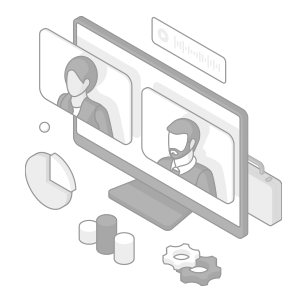
Key Features of 3D Laser Snapshot Sensors
3D laser snapshot sensors have features that set them apart from machine vision systems. The top features are discussed below:
Accurate
3D laser snapshot sensors use laser triangulation to achieve micron-level measurements and inspections.
Standalone
these systems are fully self-contained, meaning they don’t require any additional lighting, part movement or external equipment.
Robust
3D profiling uses height information to enable highly stable results across almost every material, including low contrast/no contrast parts.
Key Features of Vision Systems
Vision system solutions come with features and functions that make them desired in various applications:
Wide FOV
Cameras have a much wider inspection window than snapshot sensors, making them ideal for inspecting multiple parts/components at once.
Speed
vision systems can capture and process data much faster than a 3D laser snapshot sensor.
Cost-effective
Compared to laser-based systems, vision systems generally cost less.
Curious about our pricing?
Click here to find out more.
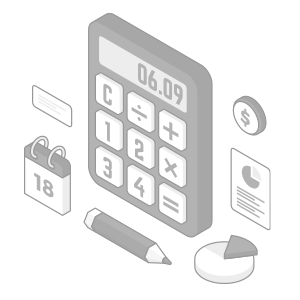
Comparing 3D Laser Snapshot Sensors and Vision Systems
Both systems can be used in similar ways. Therefore, when comparing 3D laser snapshot sensors and vision systems, the choice often comes down to the unique differences of each system and how suitable one is for the intended application.
Speed
Vision systems, equipped with high-speed camera systems and advanced image processing algorithms, offer faster scanning capabilities compared to laser snapshot sensors. However, their contrast-based nature limits defect detection to high-contrast parts, whereas laser snapshot sensors can detect subtle irregularities that might otherwise go unnoticed.
Complex Inspection Handling
Vision systems can handle fairly complex inspections, including presence/absence detection, barcode reading, and verification of coded information on packaging materials.
However, vision systems require specialized lenses, lighting, and recalibration whenever the part or environment changes. Laser snapshot sensors are self-contained and operate without the need for additional equipment.
While vision systems provide highly accurate X/Y measurements, they are not suited for Z measurements. Laser snapshot sensors excel at 3D inspections.
Choosing one over the other in this particular case will now be dependent on specific requirements. If the nature of the inspection task requires high accuracy and precise distance measurements, then a 3D laser snapshot sensor might be considered. But if color or texture information is important to get the inspection effort right, then a vision system might be more suitable.
We’re here to provide you with more details.
Reach out today!
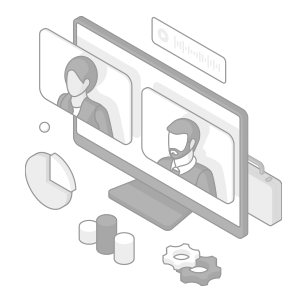
Applications of 3D Laser Snapshot Sensors
These sensors are used for 3D inspections of stationary objects. This distinguishes laser snapshot sensors from laser profilers, which scan moving targets. They are generally used in:
Quality Control
Inspecting product dimensional features, defects, and assembly accuracy.
Reverse Prototyping
Creating digital models of existing physical objects. This helps accelerate the development of new iterations or variants of an existing design.
Assembly Verification
Ensuring parts are properly aligned and coupled. Checking also for height, width, and length accuracy of components.
Applications of Vision Sensor Systems
Vision systems have diverse applications, including inline inspection for defects and quality checks on production lines, as well as offline inspections for manufactured products. They're also used in 3D robotic guidance systems, assisting industrial robots in tasks like pick-and-place and coupling automotive parts. Some common applications are:
Simple Defect Detection
Identifying and classifying defects and other irregularities in product or material design.
Code Reading
Reading 2D codes for product traceability and regulatory compliance.
Robot Vision
Helping robots with simple pick-and-place tasks for objects. Also assisting cobots with complex manufacturing tasks like welding.
Choosing the Right Technology for Your Needs
Both laser-based 3D sensors and machine vision systems are technologies for achieving production outputs that meet customer expectations and regulatory requirements.
As discussed, the choice between 3D laser snapshot sensors vs. vision systems depends on the application requirements and the options provided in each inspection/measurement technology.
For 2D inspection data or easily visible defects, a vision system is ideal. For precise distance and depth measurements, opt for a laser snapshot sensor, which measures height directly and performs well with low-contrast parts.
When not sure of which technology to choose for inline inspection or measurement needs, it's best to speak with the experts. Product developers should provide a data sheet or product specification sheet containing system features, capabilities, technical specifications, and performance characteristics.
KEYENCE offers many inspection/measurement sensors for different industries and applications. Explore these options or contact us today for more information on how we can provide expert assistance.
Contact us to learn more about how our advanced technology can help take your business to the next level.
Contact Us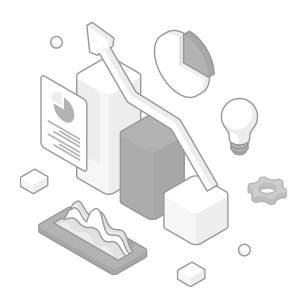
Related Products
Applications
Dimension Measurement
- Thickness and Width Measurement
- Step Height Measurement
- Inner and Outer Diameter Measurement
- Measuring Angles
- Meandering/Edge Measurement
Displacement Measurement
- Positioning and Stroke Length Measurement
- Vibration and Runout Measurement
- Deflection Measurement
- Measuring Eccentricity