3D Vision-Guided Robotics Supporting Bin Picking
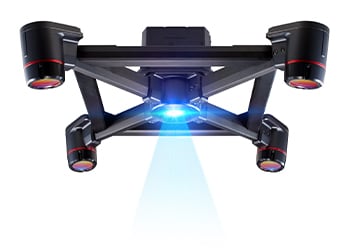
When installing industrial robots, it is not only necessary to select the robot and tooling, but also prepare peripheral equipment. Although operator training and experience are important, they present they present challenges that can be addressed with the implementation of 3D vision-guided robotics. This page describes the advantages and precautions when implementing 3D vision-guided robotics for bin picking. It also describes the benefits of using the RB 3D vision-guided robotics system from KEYENCE.
- What is bin picking?
- 3D vision-guided robotics applications
- Features of KEYENCE 3D vision-guided robotics
- Reasons why people choose KEYENCE 3D vision-guided robotics
What is bin picking?
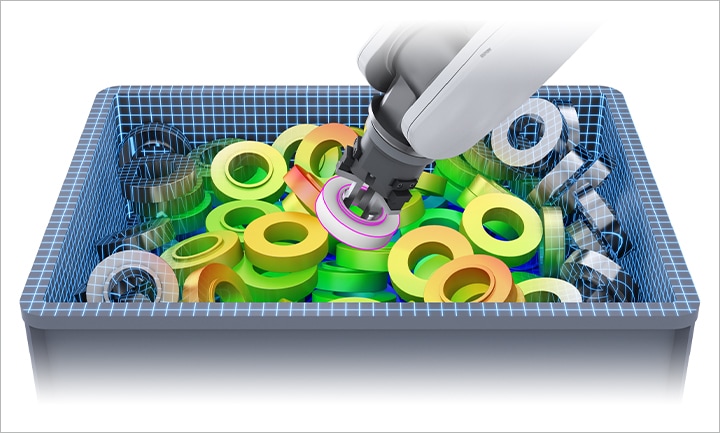
Bin picking refers to the picking up of individual targets from a part container. Examples include picking targets from containers and bins during product assembly and palletizing/depalletizing to sort packages at each delivery destination. Performing this bin picking with a robot requires the industrial robot, a camera for recognizing the position of the target, and a customizable vision system that controls the robot arm based on the captured image data. When performing bin picking with three-dimensional targets, there is a need for space recognition that includes not only the 2D X and Y dimensions, but the height of the target as well. Needing the third dimension would be the differentiating factor between choosing 2D or 3D vision-guided robotics.
Targets that support bin picking and stacked picking
The topic that is often most important when deciding whether to install 3D vision-guided robotics is what kind of targets can be used with it. 3D vision-guided robotics is capable of highly accurate 3D recognition of various parts and products, including shapes with curved surfaces, soft objects, and parts with complicated structures. Similarly, it can detect a range of size in parts from screws and bolts, to automotive gears and connecting rods, and even larger items such as automotive components like mufflers. The system can also detect different materials such as metal, plastic, and rubber. The diversity of parts and products that can be supported such as cylinders, thin boards, as well as parts with glossy and shiny finishes.
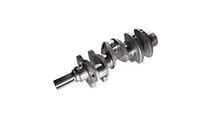
Crankshaft
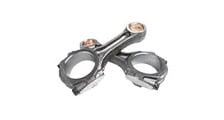
Connecting rod
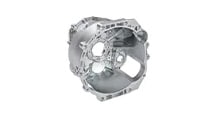
Transmission Housing
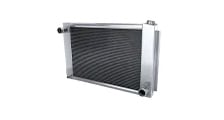
Radiator
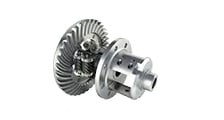
Differential Base
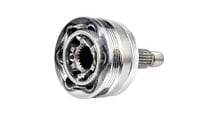
CV Joint Housing
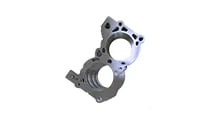
Stamped Metal
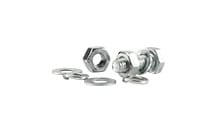
Fasteners
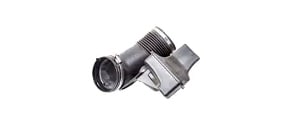
HVAC Component
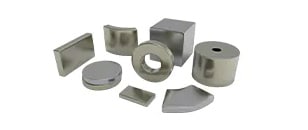
Sintered Metal Parts
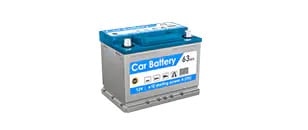
Battery
3D vision-guided robotics application examples by target
Stable picking is possible for targets having various shapes and materials. For details, see the following videos.
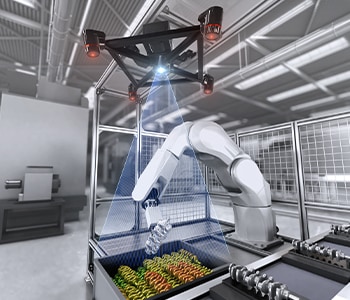
For example, 3D vision-guided robotics can be used to perform bin picking of heavy objects with complicated shapes such as an automotive engine crankshaft. These crankshafts pose a large physical load on operators should they have to manually pick these targets repeatedly. Furthermore, dropping heavy parts can lead to accidents and machine damage. Bin picking using 3D vision-guided robotics allows for accurate picking and placing in which the center shaft of each crankshaft is gripped according to the captured image data. This method eliminates the physical load on operators as well as reducing the risk to operators or machines.
Advantages of bin picking
Installing 3D vision-guided robotics and performing bin picking provides various advantages. This section introduces the advantages of using a robot to automate bin picking.
- Advantage 1Solving the labor shortage problem
- Labor shortage is a serious problem at production sites, but this problem can be solved by switching to robots for picking work.
- Advantage 2Reduced labor costs
- With robots performing bin picking, there is no need to pay the overtime that is required by human workers when they perform the same picking, which reduces costs. Also, robots provide stable operation for 24 hours a day.
- Advantage 3Automating the part supply
- At conventional production sites, parts feeders and fixtures were used to align parts so they were easy for robots to pick. With bin picking using 3D vision-guided robotics, there is no need to align parts in this manner, which decreases the man-hours spent by operators on manual work and increases overall productivity.
- Advantage 4Preventing defective products
- Bin picking via 3D vision-guided robotics eliminates the human errors of forgetting to place targets where they should be or placing targets in a backwards orientation, leading to problems that can occur when aligning targets. Defective products stemming from these errors can be prevented.
- Advantage 5Effective use of space
- As the number of work processes and manufactured product types increases, so too do the number of parts feeders and jigs, which makes it difficult to find space to install everything. However, with bin picking via 3D vision-guided robotics, the number of parts feeders and other pieces of peripheral equipment can be minimized, allowing for production lines to be established in limited space.
- Advantage 6Stable work speed
- The work speed varies depending on operator experience when operators have to align the targets and insert them into robots. However, using robots for everything including bin picking minimizes these variations in work speed, allowing for shortened takt time.
- Advantage 7Supports large targets
- Handling large or heavy targets manually during picking subjects operators to heavy stress. There are also situations where two, three, or more operators have to handle a single target. Robots can safely and reliably pick targets even if they are large or heavy.
3D vision-guided robotics applications
In this section, bin picking, palletizing/depalletizing, and stacked picking are introduced as detailed applications of 3D vision-guided robotics. Various other applications are also supported, so feel free to contact KEYENCE for details. We will propose the optimal way for you to implement 3D vision-guided robotics.
Bin picking
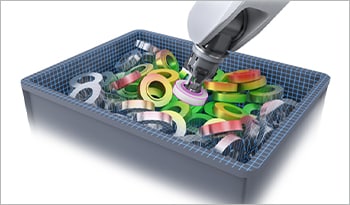
Conventionally, picking involved troublesome actions such as setting parts in jigs, aligning parts in trays, and installing parts feeders. 3D vision-guided robotics can be used to recognize scattered parts and even to perform random picking. This is an efficient method because it eliminates the hassle of aligning targets and the need for operators to do so while also minimizing the amount of peripheral equipment.
Palletizing/depalletizing
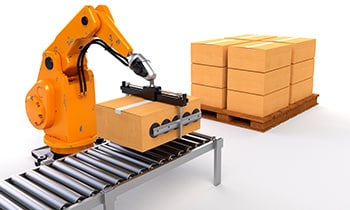
Palletizing refers to loading of packages onto a pallet, while depalletizing refers to unloading these packages. Automating this work conventionally required a dedicated device: a palletizer or a palletizing system. However, 3D vision-guided robotics can be used to support this work with a regular industrial robot.
Stacked picking
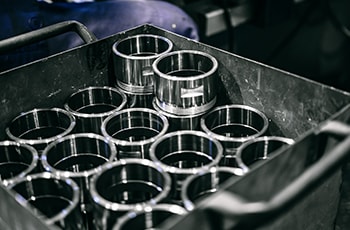
Stacking refers to the process of placing boxes and similar containers on top of each other. This is a perfect application for 3D vision-guided robotics, as this system provides accurate position in the X and Y directions, as well as in the Z to determine the height of targets.
Flexibility with Vision-guided Robotics! FA Robot Picking Examples
Features of KEYENCE 3D vision-guided robotics
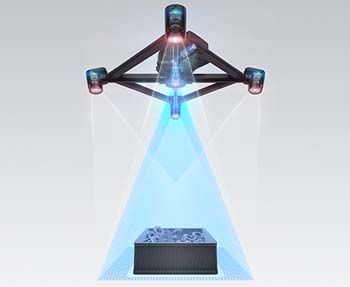
KEYENCE's 3D vision-guided robotics system, the CV-X480D, supports bin picking. This sections introduces the features of the system.
Reliably approaches targets even in deep containers
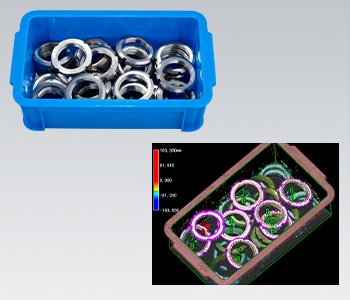
The CV-X480D vision-guided robotics system can search for targets without being affected by blind spots or obscure parts positions. The newly developed 3D search function uses four separate cameras to create a 3D image free from blind spots, in order to determine the position and orientation of the target. The system allows targets to be picked without collisions with the container or other targets even if the target is located inside a deep container.
Automatic calculation of robot movements according to the surrounding environment
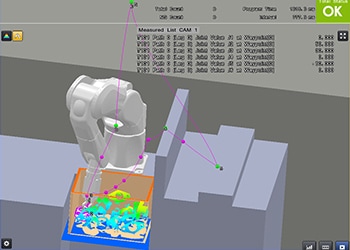
The CV-X480D 3D vision-guided robotics system is equipped with a path planning tool that automatically calculates the path of the robot to avoid collisions within the bin of parts, the bin itself, and any other peripheral devices. This path is calculated by taking into account cell layout and the movement restrictions of the robot. The picking simulator can be used to inspect and program the pick positions of the part in advance of real world testing, dramatically improving the success rate of target picking.
Automatic part insertion with no tooling changes or target stocker required
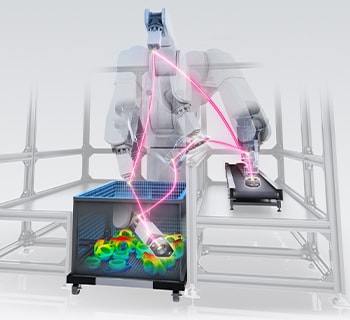
Installing the 3D vision-guided robotics system allows for automatic part insertion with no tooling changes required. Multiple product types can be covered with minimal time spent, allow for dramatic reductions in takt time. The CV-X480D is also equipped with automatic 3D calibration, enabling smooth setup, limiting the need for manual adjustments.
Allows for industrial robot installations even in compact spaces
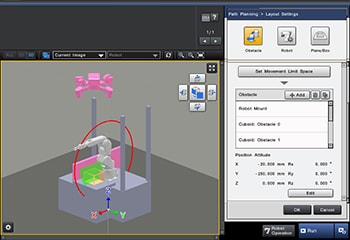
Conventionally, installing an industrial robot required peripheral equipment and devices such as stands and belt conveyors. None of these items are required with a 3D vision-guided robotics, so it is possible to automate processes by installing an industrial robot even in small and narrow spaces. Furthermore, multiple targets can be supported with program changes, so these systems are suited to production lines with multiple product types.
Path planning function/picking simulator application examples
With KEYENCE products, the optimal robot path can be calculated automatically with consideration given to collisions with peripheral equipment and the position of the robot. Detailed introductions to application examples are given in the following videos.
3D vision-guided robotics combined with an area camera
It is possible to additionally install up to two area cameras alongside the RB 3D camera. Along with the 3D camera for bin picking, the area cameras can be used after the pick to perform tasks such as grip correction and position. Combining 3D vision-guided robotics with an area camera in this manner provides higher accuracy and allows different types of work to be performed simultaneously.
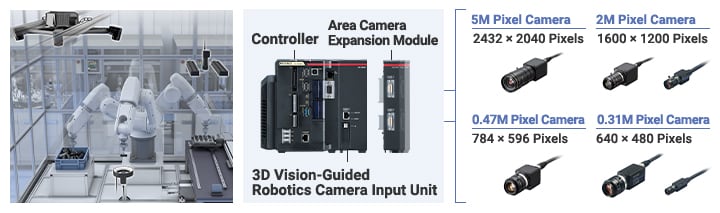
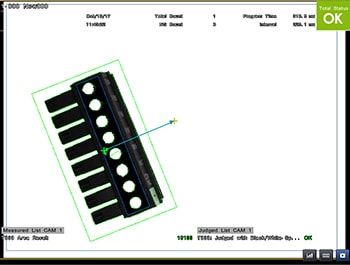
Gripping misalignment correction/product type difference check
Uses 2D vision-guided robotics to provide high precision positioning after bin picking. Simultaneously perform checks and inspections of targets in relation to product type, front/back, and orientation, etc.
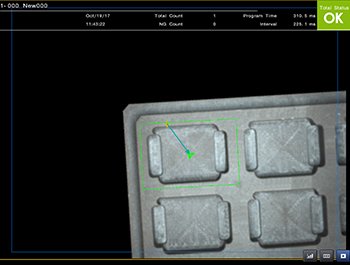
Place position displacement correction
Uses 2D vision-guided robotics to detect the position of the tray where products will be placed. The system will calculate the offset relative to the registered position, to correctly place the parts.
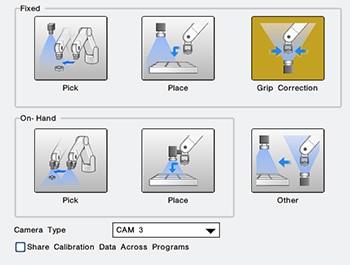
Easy linking with 2D vision-guided robotics
KEYENCE’s CV-X480D can easily link with 2D vision-guided robotics. Simply select the application to match the type of correctional operation required to achieve the quickest and ideal setup.
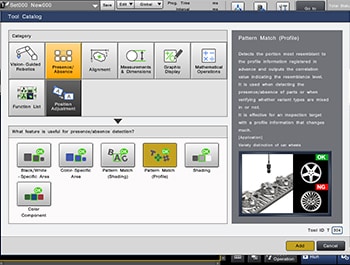
Operations such as product type difference checks and inspections for presence/absence performed simultaneously with bin picking
Adding an area camera to the system allows for efficient operation where product type difference checks and inspections for presence/absence are performed at the same time as the bin picking performed by 3D vision-guided robotics.
Reasons why people choose KEYENCE 3D vision-guided robotics
This final sections introduces specific points where KEYENCE's CV-X480D 3D vision-guided robotics system excels and the reasons why it benefits customers.
KEYENCE-developed optical systems

The four cameras of the CV-X480D vision-guided robotics system capture each image from different angles, eliminating blind spots and creating an incredibly stable 3D image. Additionally, the built-in high precision CMOS sensor, high speed processor and specially designed LED projector allow for highly precise target detection.
Reproduction of the bin picking environment
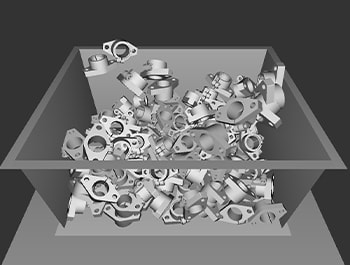
The dedicated physics engine of the CV-X480D 3D vision-guided robotics system can reproduce a realistic simulation of target pileup on a PC with no need to prepare real targets or containers. The PC simulation is a highly accurate reproduction of the worksite, which reduces the hassle of preparing actual equipment.
Built-in path planning tool
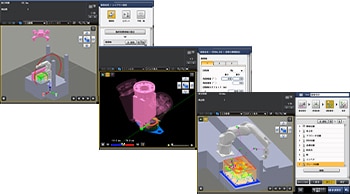
The CV-X480D 3D vision-guided robotics system has a built-in path planning tool and picking simulator, which can be used to perform simulations on a PC. Once the environment layout is built in the path planning tool, the optimal path, in which all obstacles are avoided, can be calculated automatically. An advantage of this tool is that the robot, container, and obstacles can be placed and on-screen teaching of items such as the target gripping position can all be performed with a mouse. No specialized knowledge is necessary.
For more information on KEYENCE’s CV-X480D 3D vision-guided robotics system, read the following document.