Vision Examples in the Commodities Industry
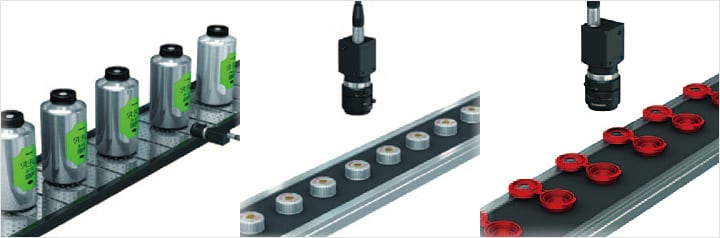
Appearance inspection of spouts
This is an appearance inspection of spouts.
Key inspection points
Inspections for defects that are similar in color to the product can be unstable under conventional lighting. Multi-Spectrum mode allows for stable inspections by extracting only the areas required for detection, even when it is difficult to distinguish the color of faint burn marks or fouling from that of the finished product.
Recognition result in multi-spectrum mode
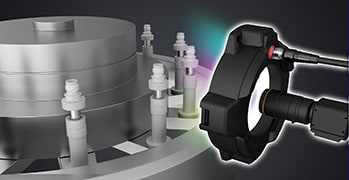
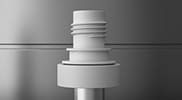
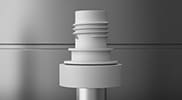

(after color extraction)
Inspecting center misalignment of packings
Conventional machine vision could not precisely check center misalignment because they could not recognize the edge accurately.
The Profile Position mode of the XG-X/CV-X Series allows accurate inspection for center alignment by drawing an approximate circle based on the data of the inner and outer peripheries of the packing.
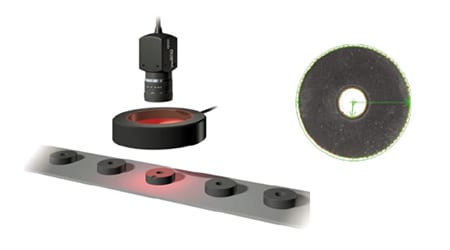
Inspecting container inner surfaces
Using machine vision, detect stains on the inner surfaces of paper cups.Since the seam in the cup affected the inspection, conventional methods set a master area to exclude the seam from the detection. This required complicated settings, increasing processing time and decreasing production efficiency. The inability to check the area near the seam was also a problem.
The Real-time Image Extraction filter can ignore seams and extract stains only, allowing accurate detection of stains only without the need for position correction. The setting requires just drawing of an inspection area and since master processing is not used, stains near the seam can also be detected. The processing speed can be improved significantly, increasing production efficiency.
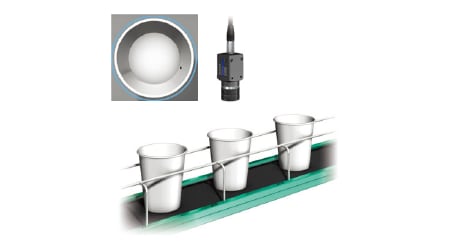
Detecting misaligned labels
Check the positions of labels attached to cups or bottles. Color vision sensors were used to detect misalignment, but there was no way to adjust tolerance. The detection often failed due to the influence of the wobbling caused by conveyor transfer.
Using machine vision enables more accurate recognition of label positions. The XG-X/CV-X Series offers unique detection algorithms to convert the label position into numerical values to achieve quantitative control. Since position correction is also possible, the inspection is stable in spite of wobbling during transfer. When the brightness difference between the containers and labels is small, using a color camera improves stability.
Bottle mouth dimension measurement
Measure the dimensions of PET bottle mouths. Conventionally, sample inspection was performed with an optical comparator because the line speed was fast. Since not all products could be checked, it was impossible to prevent the outflow of defective products completely.
The XG-X/CV-X Series supports various cameras capable of high-speed processing and fast transmission. This allows inline 100% inspection even for production lines requiring fast line speed. Dimension measurement based on geometric calculation achieves inline dimension measurement of all products. Unlike optical comparators, inspection does not depend on human operation so measurement errors can be eliminated.
Detecting chipping of a bottle mouth
Inspect the mouths of beverage bottles made of PET or glass for chipping. Although inspection was performed with machine vision, chipping could not be recognized due to the influence of extraneous light, resulting in frequent outflow of defective products.
The XG-X/CV-X Series can accurately recognize chipping of the mouth by using its unique stain detection algorithm as well as image enhance filters such as Contrast Conversion and Preserve Intensity. You can also hold and check NG images during operation to adjust tolerance without stopping the line. This improves production efficiency.
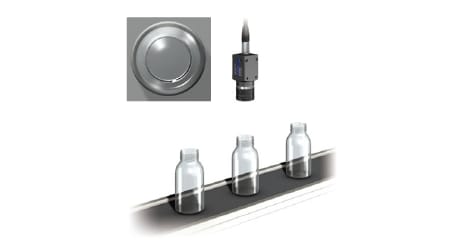
Detecting deformed cups
Check for deformation of cups using machine vision. Although machine vision was used for the inspection, it could only measure the width in XY directions. Defective products may have been overlooked depending on the deformation state.
The Trend edge mode of the XG-X/CV-X Series can measure up to 5000 points so deformations can be recognized more accurately. This mode is especially suitable for the measurement along a circumference, such as cups. The system can accurately recognize the edge with its unique algorithm and measure the entire circumference of a cup. This reduces incorrect judgment and prevents the outflow of defective products.
Inspecting the appearance of lateral surfaces of containers
Inspect the lateral surfaces of a container along the full circumference. Conventional methods required the capture of images of surfaces from their respective directions. Appearance inspection of cylindrical containers took enormous labor. Inspection was often affected by uneven lighting and it was difficult to improve the accuracy and stability.
Replacing a normal area camera with a line scan camera ensures stable appearance inspection of the lateral surface of cylindrical targets. A line scan camera can continuously capture the lateral surface along the full circumference and show it as one developed image. The inspection is hardly affected by lighting and can achieve higher accuracy. The system can recognize shapes or characters and read various codes on a curved surface, which were difficult with conventional area cameras.

Adjust the focus on the surface nearest to the camera.
Inspecting the appearance of lateral surfaces of containers
Adjust the focus on the surface nearest to the camera. Check the appearance of paper packs. The line speed for paper packs or sheet-shaped products was too fast to use conventional machine vision for inspection. Using an area camera for inspection requires even lighting of a large area, leading to problems with cost for the lights and mounting space.
A line scan camera achieves inspection of paper packs at minimum cost, even when used for high-speed line and large areas. When the field of view is about 500 mm, a line scan camera can keep up with line speeds of about 600 m/minute. Satisfactory inspection can be achieved with just a normal bar light, eliminating the need for a large lighting system.
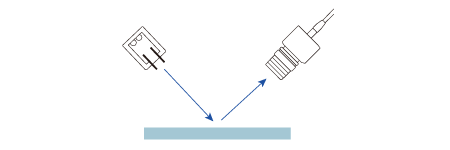
The use of a bar light saves costs and spaces.
Checking for defects on a sheet
Check for defects on a sheet using machine vision. The inspection of sheet-shaped targets was difficult due to the influence of glare.
The XG-X/CV-X Series can accurately detect foreign particles, holes, and stains on sheets. Using color processing allows inspection of subtle changes and prevents the outflow of defective products.
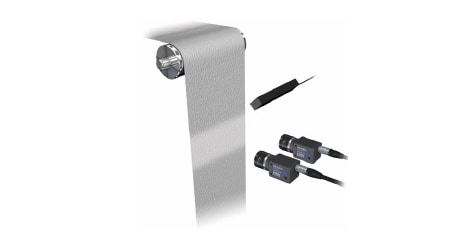
Inspecting resin coated products for flaws or chipping
Check appearance for flaws or chipping on a resin surface. Using conventional machine vision for inspection required preprocessing and programming. The introduction took a lot of labor. Sometimes detection was difficult depending on the background color.
The XG-X/CV-X Series offers a dedicated mode for stain detection to check for the presence of marking or flaws on product surfaces. This allows easy introduction of machine vision on production lines.
Detecting deviation inside resin caps
Detect the deviation of paper backing inside resin caps. Visual inspection was performed conventionally, but the labor costs were high.
Machine vision can easily detect the deviation of paper backing inside the resin caps. The fast transmission speed of the XG-X/CV-X Series enables accurate inline judgment. It is also possible to determine the direction or level of the deviation based on the change in color or gloss
Detecting stains, dust and pinholes
Detect the deviation of paper backing inside resin caps. Visual inspection was performed conventionally, but the labor costs were high.
Machine vision can easily detect the deviation of paper backing inside the resin caps. The fast transmission speed of the XG-X/CV-X Series enables accurate inline judgment. It is also possible to determine the direction or level of the deviation based on the change in color or gloss.
Detecting burns on resin caps
Check for burns on resin caps produced during molding. Conventional machine vision could not recognize burns depending on the color of the resin cap.
Using a color machine vision allows recognition of burns only, regardless of resin cap color. This eliminates the labor for changeovers on lines producing multiple types of resin caps, improving production efficiency.
Detecting products remaining in molds
Detect products remaining in molds after molding. Conventional machine vision was commonly used to check for remaining products, but differentiation was difficult when the contrast between the product and mold was low. Sometimes remaining products were overlooked and caused mold breakage.
Color machine vision can reliably extract the color of the product only, despite low contrast, and prevent the product from remaining in the mold. A broken mold can cause production line shutdown and require repair work, resulting in significant losses. Using machine vision can prevent this from occurring.
Measuring the width of sheet material
Check for crushed parts of PET bottles. Conventional machine vision could not detect crushed parts of PET bottles due to the low contrast.
Install machine vision in a star wheel transfer process and detect a crushed part of PET bottles. The XG-X/CV-X Series can recognize changes in the PET bottles reliably by using various image processing functions.The system allows 100% inspection to prevent the outflow of defective products.
Detecting crushed PET bottles
Measure the width of sheet material. Inspection of large targets required multiple machine vision. It also required labor for image composition.
The XG-X/CV-X Series supports a high-resolution camera with 21 megapixels to cover the large area with two cameras. It is also possible to use a group of existing cameras as a quick fix to measure a large target. Since the XG-X/CV-X Series can connect multiple cameras and offers a composition function, it can be used for a broad range of applications.
Measuring the dimensions of building boards
Measure the dimensions of various sections of building boards. Calipers or other tools were used, so the measurement took time and the results varied depending on the worker.
Machine vision can automate dimension measurement of building boards. The system can measure even detailed dimensions such as the distance between patterns, which ensures stable product quality. Inline measurement helps improve production efficiency.
Measuring the amount of banked rubber
Measure the amount of banked rubber during rubber molding. Product quality was not stable due to increases and decreases in the amount of the bank.
Using machine vision to measure the amount of banked rubber and continually maintain constant feeding amount ensures proper management and stable product quality.
Detecting notches of packings
Check the position of notches of packings. In some cases, conventional machine vision could not differentiate between chipping or other defects and notches, or could not detect minute notches accurately.
The Trend edge mode of the XG-X/CV-X Series can measure up to 5000 points so that changes along a circumference can be detected more accurately. This ensures accurate recognition of the notches of packings. The system can also check the appearance for stains or burrs simultaneously, which improves efficiency.
Inspecting connectors for improper arrangement
Check connectors for improper wiring. Conventional monochrome cameras could not differentiate colors so it was impossible to differentiate wires.
Using a color camera allows easy inspection for improper arrangement or different types based on the difference in wire colors. The system can check for other defects such as missing wires or flaws simultaneously, which improves efficiency. The XG-X/CV-X Series supports color cameras and allows mixed connection with monochrome cameras or line scan cameras, so the system can be used in a variety of applications.
Inspecting the appearance of aluminum can bottoms
Check for foreign particles or stains adhered to the bottoms of beverage cans. Although conventional machine vision could detect flaws or stains, detection sometimes failed because of the irregular gloss appearing on the curved surfaces of can bottoms.
The XG-X/CV-X Series offers Shading correction processing and Defect inspection mode to cancel irregular gloss and allow stable inspection. Shading correction processing can eliminate the gloss common with metal objects. This preprocessing assumes gradual shading information on the background, generates a background image without foreign particles or flaws and then identifies the differences from the input image in real time. This processing enhances just foreign particles and flaws.
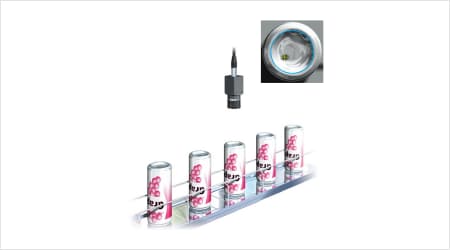
Inspecting resin bottles for defects
Check the appearance of the mouths of resin bottles. Although foreign particles on the side of the mouth could be detected accurately with conventional machine vision, detection accuracy was low for other defects such as burrs or chipping on the circumference of the mouth, resulting in frequent incorrect recognition.
The Profile Defect stain mode of the XG-X/CV-X Series can stably detect defects on an oval circumference. It assumes an oval to be a reference shape based on the profile and detects edge points that deviate greatly from the reference oval as defects. Consequently, inspection is possible when the image is captured from angles other than only from directly above.
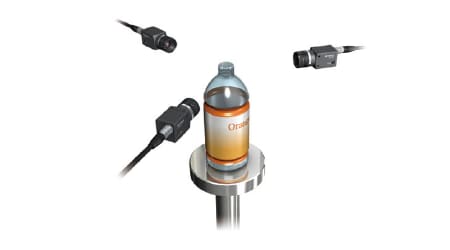
Inspecting O-rings and packings for burrs and chips
Check for burrs and chips of O-rings and packings. Since O-rings and packings are soft materials, they may not be perfect circles due to deformation. This deformation caused incorrect detection.
The Profile Defect stain mode of the XG-X/CV-X Series can stably detect defects in free-form shaped areas. It assumes a reference free-form shape area based on the profile for each input image and detects edge points that deviate greatly from the reference area as defects. This allows accurate defect detection even for targets with variable shapes such as O-rings and packings.
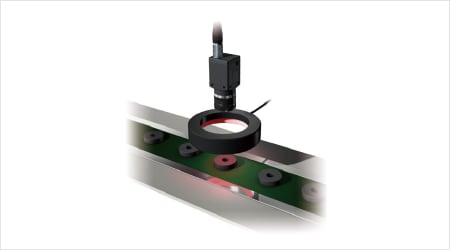
Inspecting the appearance of media disks
Check the appearance of media disks. Color cameras were used to check media disks for stains or flaws, but it was necessary to change the setting every time the color of the resin section of the media was changed.
The Fine color stain mode of the XG-X/CV-X Series can detect stains and flaws that are different from the background with the same settings, even when the product type is changed. Fine color processing detects color differences based on hue, chroma and brightness information, which enables detection of all stains with colors that are different from the background color. The Ignore Intensity function excludes brightness that represents black to white shading information. This prevents the inspection from being affected by the shadow of steps after shaping.
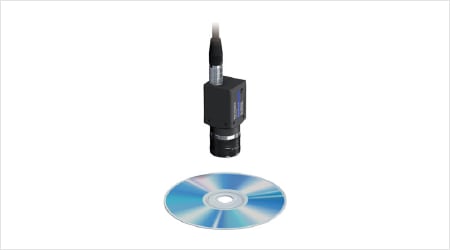