Vision Examples in the Automotive Industry
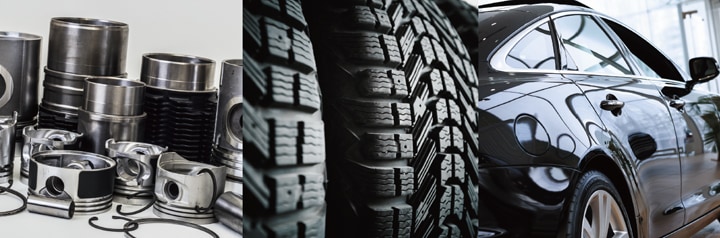
Using Vision to Inspect and Manage 30,000+ Parts
In the automotive industry, even minor malfunctions may lead to grave accidents. The demands for quality and accuracy are high, and inspection standards are set high to meet them. Car generally consists of over 30,000 parts, including tiny bolts. The number of parts is increasing due to multifunctionalization. It is not easy to perfectly inspect these parts and manage the information.
For manufacturers of finished cars, it is imperative to quickly identify the extent of the impact when recalls are issued and collect the relevant products. Otherwise, the company will suffer great losses and their brand will be damaged. In Japan, the End-of-Life Vehicles Recycling Law was enacted in few years ago and recycling of materials such as airbags and CFCs has been made compulsory. Consequently, it is urgent that traceability covering not only manufacturing of parts and assembly of whole vehicles but also maintenance, inspection and vehicle disposal.
The need for a database of inspection results and other information is thus increasing year after year. Image processing has been getting attention as a way to achieve this. It is expected that replacing inspections that rely on human eyes and experience with image processing will increase efficiency and achieve both cost reduction and accuracy improvement. The following are actual introduction examples of image processing systems in the automotive industry. Please use them as a guide to improve efficiency at your production sites and ensure traceability.
Presence/Absence Inspection
Inspection of rubber bushings
This is an example of an inspection to detect contamination from the injection molding process.
Key inspection points
It is traditionally challenging to identify assembled parts with slight color variations like rubber bushings. The Multi-Spectrum Lighting technology stably detects the slightest variations in color and shading to detect contamination.
Recognition result in multi-spectrum mode

- A
- Coloring is similar
![[A]](/Images/ss_visionbasics_e_auto_019_1962874.jpg)
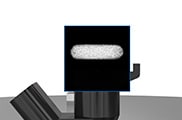
O-ring color difference inspection
This is an example of an O-ring or gasket inspection.
Key inspection points
Multi-Spectrum allows for stable imaging and detection of parts that have slightly different colors and shading such as O-rings, gaskets, and parts that may come from multiple suppliers.
Recognition result in multi-spectrum mode
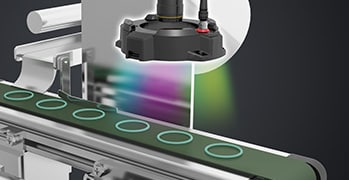
- A
- Coloring is similar
![[A]](/Images/ss_visionbasics_e_auto_022_1962877.jpg)
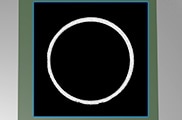
Presence inspection for conformal coating on ECU
Inspect whether a moisture-proof agent is applied properly on ECUs using machine vision.
Key inspection points
Since typical moisture-proof agents are transparent, it was difficult to recognize the application and sometimes defective application was overlooked. Use a moisture-proof agent containing a fluorescence agent, illuminate the target with a UV light and capture the image with a 21 megapixel camera. This allows high-accuracy inspection of the application of the agent which was difficult with conventional methods.
Recognition result with a 21 megapixel machine vision
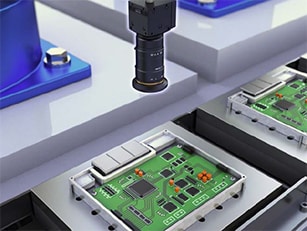
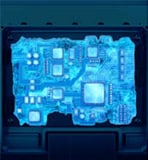
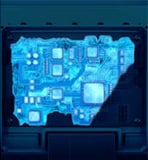
Fuse assembly error inspection
Inspect whether fuses are installed correctly in a fuse box using machine vision.
Key inspection points
Since fuses have the same shape, it was difficult to differentiate them with a monochrome camera. Inspection for incorrect fuse configuration can be achieved through capturing colors or characters with a color camera. The Auto-Teach Inspection tool allows you to complete settings by just registering an OK product, so operation is easy even when there are many types of products.
Recognition result with machine vision
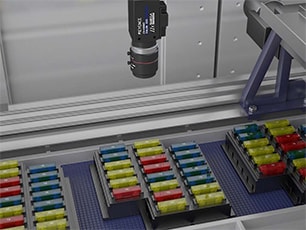
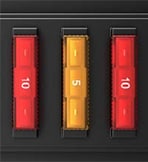
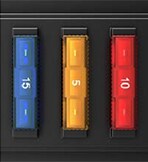
Appearance Inspection
Missing-roller inspection for bearings
This is an example of a missing-roller inspection for bearings.
Key inspection points
Lighting color selection can help to solve problems such as those that occur when grease adheres to the target, making it difficult to inspect. In this example, LumiTrax™ Mode makes it possible to detect missing rollers in bearings filled in with transparent grease.
Recognition result in LumiTrax™ mode
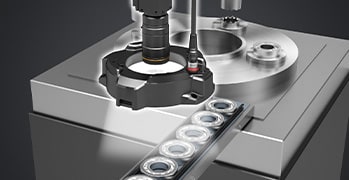
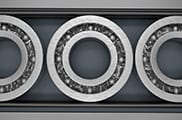
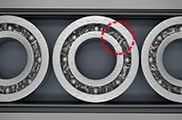
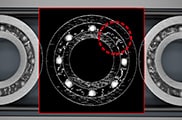
(shape image)
Shaft material sorting
This is an example of shaft material sorting.
Key inspection points
Multi-Spectrum Mode is effective at sorting slight differences in color. This is often necessary when working with metal work materials and so forth. Sort materials by detecting slight differences in color using data collected from eight wavelengths.
Recognition result in multi-spectrum mode
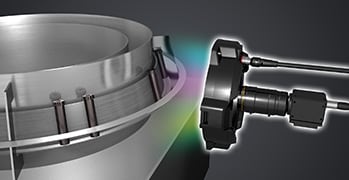
- A
- Coloring is similar
![[A]](/Images/ss_visionbasics_e_auto_029_1962884.jpg)
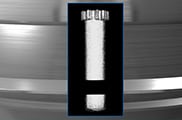
Burn-mark inspection after heat treatment
This is an example of an external post-quenching appearance inspection.
Key inspection points
Inspections for defects colored similarly to how the product is colored can be unstable under conventional lighting. Multi-Spectrum Mode allows for stable inspections by extracting only the burn marks required for detection, even when it is difficult to distinguish the color of the burn marks from that of the finished product.
Recognition result in multi-spectrum mode
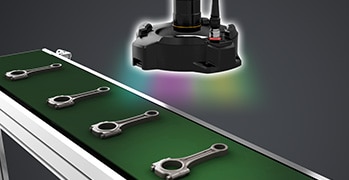
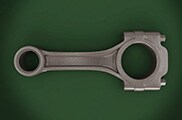
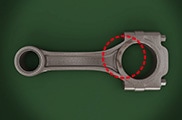
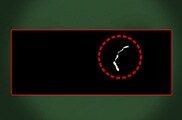
(after color extraction)
Sealant coat inspection
This is an example of a sealant coat inspection.
Key inspection points
Under conventional lighting conditions, it can be difficult to cleanly extract the coated parts, especially when the sealant color resembles that of the product. This makes detection unreliable. Multi-Spectrum Mode is able to extract even the slightest difference in color, allowing for accurate inspections of coating condition.
Recognition result in multi-spectrum mode
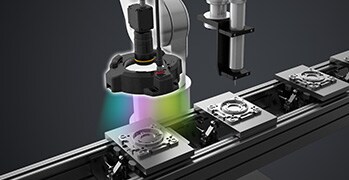
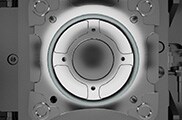
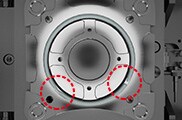
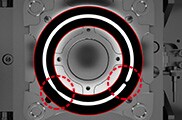
(after color extraction)
Bearing Side Inspection
Inspect the sides of glossy bearings for cracks using a vision system.
Key inspection points
With conventional lighting conditions, it was difficult to detect flaws such as subtle cracks due to the small difference in contrast with the background. With a line scan camera, it is possible to detect just these cracks.
Recognition result with a line scan camera
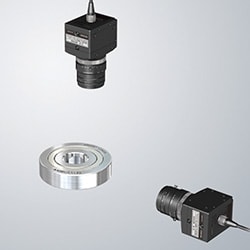
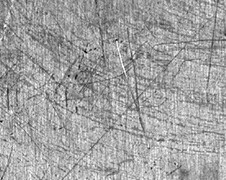
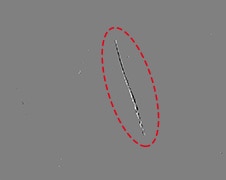
(Shape image)
Aluminum Sheet Appearance Inspection
Inspect aluminum sheets for shallow dents and small holes using a vision system.
Key inspection points
The surface glossiness of aluminum sheets makes it difficult to capture clear images of the shadows of shallow dents and microscopic holes. With a line scan camera, it is possible to capture such images by canceling the glossiness.
Recognition result with a line scan camera

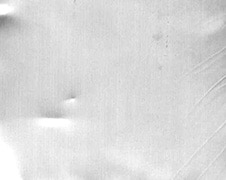
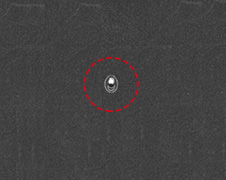
(Shape image)
Cylindrical Metal Component Side Appearance Inspection
Inspect the sides of cylindrical metal components for rubbing flaws, pinholes, and linear flaws using a vision system.
Key inspection points
It was difficult to capture images of metal components because it is easy for them to develop diverse defects ranging from pinholes to flaws. With a line scan camera, it is possible to detect all the defects on the side of a cylinder with a single captured image.
Recognition result with a line scan camera
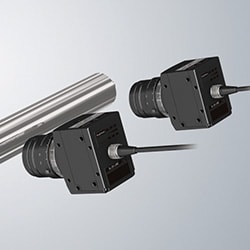
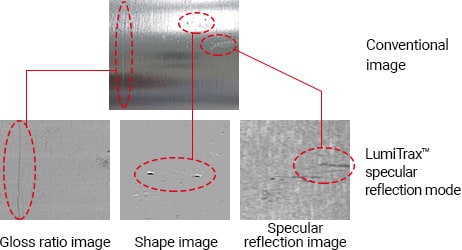
Sheet Appearance Inspection
Inspect sheets for difficult-to-see stains using a vision system.
Key inspection points
The intensity due to wrinkles on the sheet is similar to the intensity in stained parts. This phenomenon may result in unstable inspection. With a line scan camera, the image can be selected to match the defect to detect, which, in combination with image enhance filters, allows for clean extraction of just the stained part.
Recognition result with a line scan camera
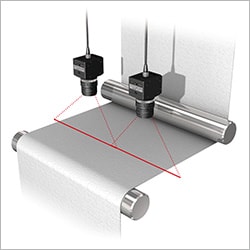
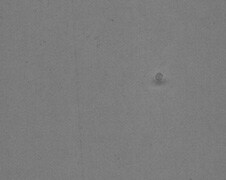
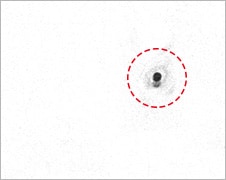
(Specular reflection image)
Black Rubber Sheet Appearance Inspection
Inspect black rubber sheets for wrinkles using a vision system.
Key inspection points
Wrinkles on black sheets are often difficult to detect due to poor contrast. Shape images allow for inspection with wrinkles and foreign particles clearly extracted.
Recognition result with a line scan camera
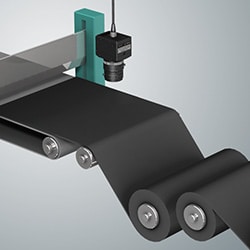
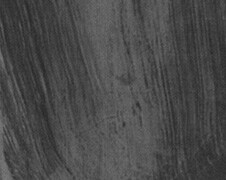
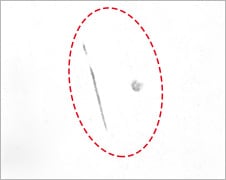
(Specular reflection image)
Glass Appearance Inspection
Inspect glass for stains and chips using a vision system.
Key inspection points
Cracks and chips occur easily in glass. Inspections for these two types of defects had to be performed separately with different lighting and settings. With a line scan camera, it is possible to simultaneously detect these defects in liquid crystal glass.
Recognition result with a line scan camera
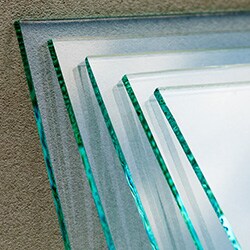
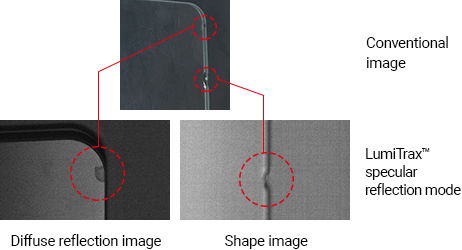
DPF appearance inspection
Check for appearance defects such as cracks or clogging in DPFs (Diesel Particulate Filters) using machine vision.
Key inspection points
Appearance inspection of DPFs or catalysts for cracks or clogging was difficult due to the large target size. Using a 21 megapixel camera offering the highest number of pixels in the industry enables high-accuracy inspection.
Recognition result using a 21 megapixel machine vision
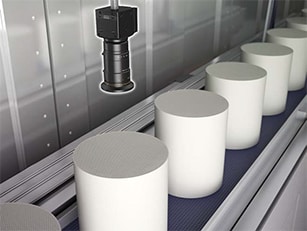
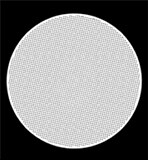
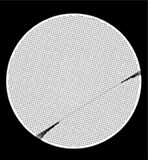
Oil seal appearance inspection
Check for appearance defects such as chipping or burrs on oil seals using machine vision.
Key inspection points
For oil seals, it is extremely important to inspect their contact surfaces for chipping or burrs. Stable inspection was difficult because they deformed easily. This problem can be solved with the new defect-detection mode "Trend edge stain," that extracts a profile from the edge information of the target and identifies as defects those sections that greatly deviate from the profile.
Recognition result with machine vision
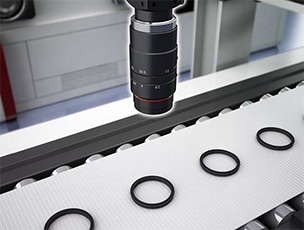
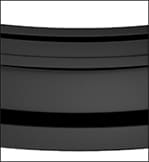
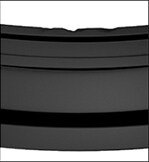
Engine valve head appearance inspection
Inspect engine valve heads for flaws or stains using machine vision.
Key inspection points
Conventional area cameras were not capable of detecting surface stains or individual differences that were specific to forged products. The "LumiTrax function" allows accurate detection of defective shapes.
Recognition result with machine vision and LumiTrax

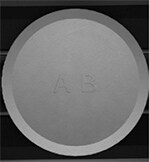
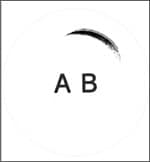
Piston side coating appearance inspection
Inspect appearance, such as the coating on the sides of pistons, using machine vision.
Key inspection points
With an area camera, it was difficult to determine optimum lighting condition due to lighting unevenness. With a line scan camera, it is easy to obtain an evenly-lighted image.
Recognition result with a line scan camera
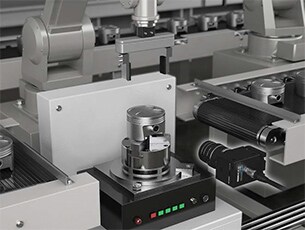
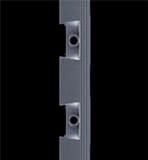
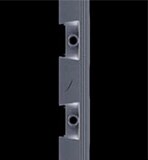
Differential gear appearance inspection
Inspect the sides of differential gears for linear flaws, dents, and stains using a vision system.
Key inspection points
For the inspection of the sides of cylindrical targets such as gears for remaining black scales, stains, flaws, or dents, it was difficult to apply lighting evenly. With a line scan camera, images of cylindrical shapes can be captured continuously. Also, LumiTrax™ specular reflection mode allows for the detection of linear flaws, dents, and stains with a single captured image.
Recognition result with a line scan camera
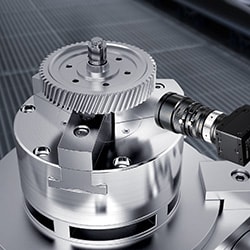

Dimension inspection
Connector terminal bend inspection
Inspect the connector terminals of ECU units using machine vision.
Key inspection points
KEYENCE offers a package of tools for connector inspection. You can start inspection quickly without configuring calculations. Using a 21 megapixel camera improves the inspection accuracy.
Recognition result with a 21 megapixel machine vision
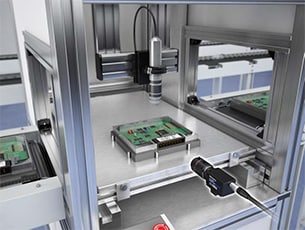
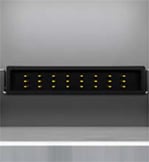
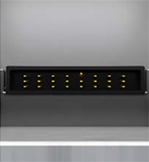
Spark plug dimension inspection
Inspect the dimensions of spark plugs using machine vision.
Key inspection points
Dimension inspection of complex-shaped targets required the use of multiple measurement tools and calculations. KEYENCE's image processing system offers dimensions/geometry tools that allow high-accuracy inspection with intuitive operation.
Recognition result with machine vision
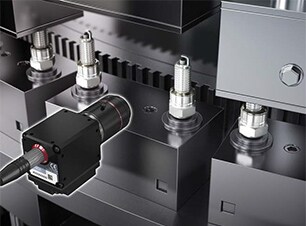
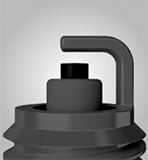
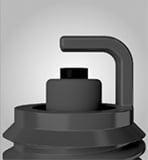
Positioning/alignment
Battery lamination layer alignment
Machine vision make the alignment of battery cells easy.
Key inspection points
Easy configuration and flexible customization support the alignment required in the battery cell manufacturing process. Using a 21 megapixel camera enables the inspection of large targets.
Alignment using a 21 megapixel machine vision
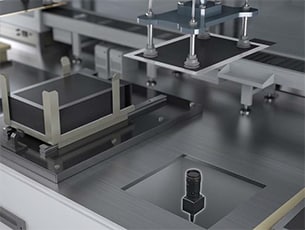
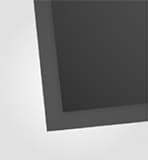
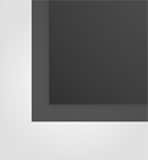
Robot pick and place
Position targets for robot picking using machine vision.
Key inspection points
The combination of robot and camera allows more flexible picking. Control does not require any teaching or programming, and the man-hours for startup and changeover are significantly reduced.
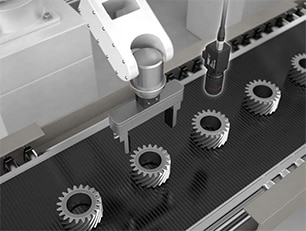
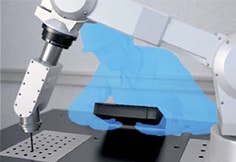
Conventional method
Recognition inspection
Inspection of engraved characters of an ECU case
This is an example of character inspection of an ECU case.
Key inspection points
Sometimes when inspecting engravings on metal targets, the effect of light reflection under normal lighting makes it difficult to identify characters. LumiTrax™ Mode uses four-directional lights to extract only the surface irregularities. This will allow for accurate inspections of engravings.
Recognition result in LumiTrax™ mode
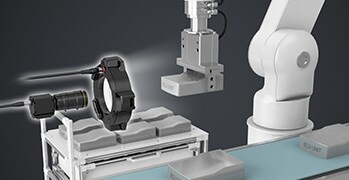

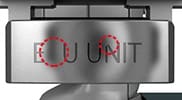
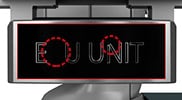
(shape image)
Inspection of engraved characters on a gear
This is an example of an inspection of engraved characters on a gear.
Key inspection points
The reliable inspection of lot numbers and other information engraved on a variety of parts can be difficult depending on the condition of the surface material. But LumiTrax™ Mode makes it possible to extract only the irregular parts of engravings. This contributes to more reliable inspections.
Recognition result in LumiTrax™ mode
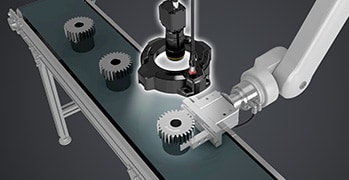

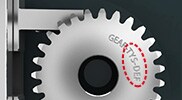

(shape image)
Fuel pump 2D code reading
Read 2D codes marked on fuel pumps using machine vision.
Key inspection points
Reading the 2D codes marked on parts with machine vision to identify the parts ensures traceability. Conventional methods sometimes could not read the codes due to the surface condition or reflection of the parts. KEYENCE's machine vision allows accurate identification.
Recognition result with machine vision
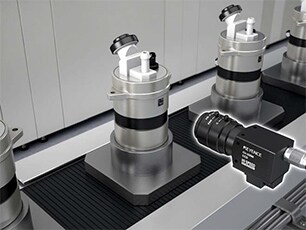
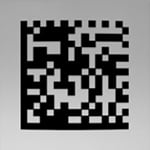
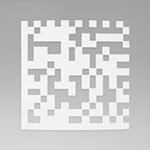
Injector stock number OCR
Use machine vision to capture an image of the part numbers marked on injectors and read them with the OCR tool.
Key inspection points
Read the part numbers marked on injectors with the OCR tool. The part numbers can be read accurately without being affected by marking quality. This prevents the mixing of different types.
Recognition result with machine vision
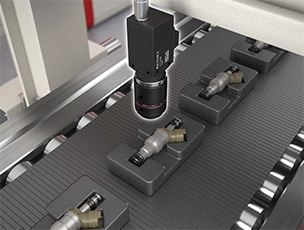

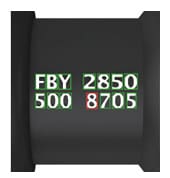
Character recognition for inscriptions on casted parts
Recognize characters marked on cast parts using machine vision.
Key inspection points
It was difficult to introduce machine vision for the recognition of characters marked on cast parts due to difficult lighting conditions. However, the combination of the LumiTrax function and an area camera allows low-cost, stable detection.
Recognition result with an area camera and LumiTrax
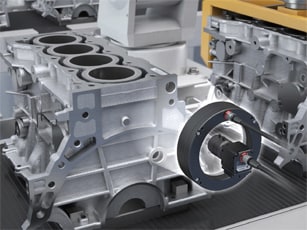
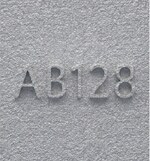
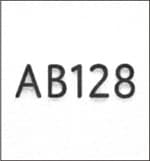
3D image processing
Torque Converter Assembly Inspection
This is an example of an inspection of torque converter assembly.
Key inspection points
With a Pattern Projection Vision System, height data acquired from 3D images can be used to inspect the presence and positioning of low-contrast components.
When pattern projection lighting is used to perform inspections, the optimal image can be selected from normal images, LumiTrax™ images*1, and 3D images. Therefore, man-hours required for adjusting settings can be reduced, and yield rate can be improved.
*1 LumiTrax™ lighting creates two images: one to reduce glare, and one to emphasize height features while ignoring color.
Recognition result with pattern projection lighting
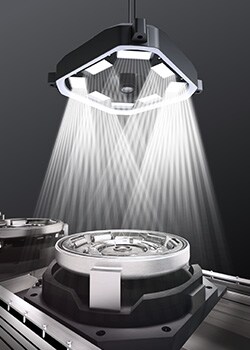
- A
- Spring assembly defect
- B
- Fitting defect
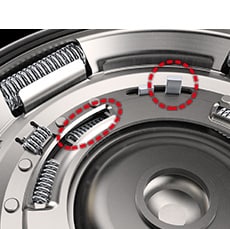
(color image)
![[A][B]](/Images/ss_visionbasics_e_auto_067_1962922.jpg)
(height image)
Electrical Component Assembly Inspection
Inspect electrical components for loose screws, diagonal insertion of gears.
Key inspection points
3D height data adds a variety of possible inspections to assembly and part sorting applications. Low-contrast 2D images can struggle with assembly and seating inspections when the camera can only be mounted above the part. The combination of 2D and 3D images adds stability when detecting loose parts as well as detecting shape differences with a single camera.
Recognition result with pattern projection lighting

- A
- Loose screw
- B
- Diagonal insertion of gear
- C
- Product sorting by presence/ absence of protrusions
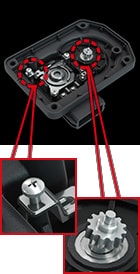
(color image)
![[A][B]](/Images/ss_visionbasics_e_auto_070_1962925.jpg)
(height image)
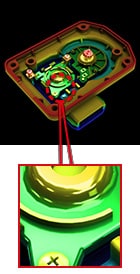
![[C]](/Images/ss_visionbasics_e_auto_072_1962927.jpg)
Assembly Inspection of Valve Body
This is an example of an inspection of valve body assembly.
Key inspection points
Acquire color and height data on parts up to 10x10 inches for stable assembly verification. Detect screw presence and surface defects simultaneously. Remove glare and ambient light with the built-in LumiTrax™ mode that comes standard with all Pattern Projection Lights.
Recognition result with pattern projection lighting
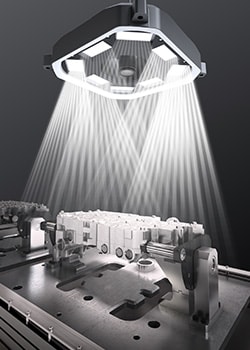
- A
- Valve absent
- B
- Valve assembly defect
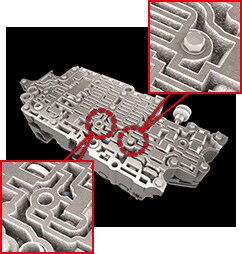
(color image)
![[A][B]](/Images/ss_visionbasics_e_auto_075_1962930.jpg)
(height image)
Drum Assembly Inspection
Inspection of retaining ring/snap ring dimensions, single insertion, and proper seating.
Key inspection points
Since 2D and 3D images are both captured with one trigger, it is possible to verify the opening dimension of the retaining ring while leveraging height data to inspect for seating and double insertion. Conventionally, it was not possible to perform these inspections with only a vision system, and additional inspection equipment such as displacement sensors were required. With Pattern Projection, all of these inspections now can be completed in a single process.
Recognition result with pattern projection lighting
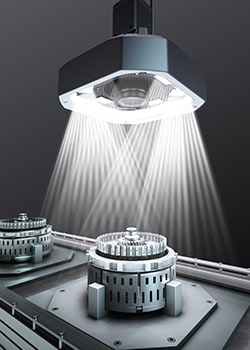
- A
- Diagonal insertion of C ring
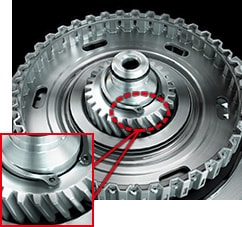
(color image)
![[A]](/Images/ss_visionbasics_e_auto_078_1962933.jpg)
(height image)
Welding Inspection on Motor Parts
Inspection of welding misalignment, welding defects, and terminal disassembly
Key inspection points
With a conventional 2D image, weld misalignment and bent terminals are easily missed because grayscale values alone are not enough for reliable inspection. 3D imaging adds stability to these inspections with height data, so it is possible to inspect for misalignment, wire disassembly, and welding defects without concern of part color variation.
Recognition result with pattern projection lighting
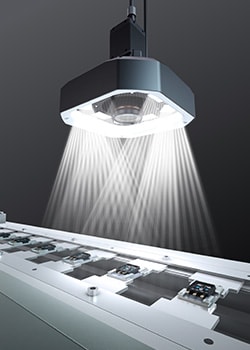
- A
- Welding misalignment
- B
- Bent terminal
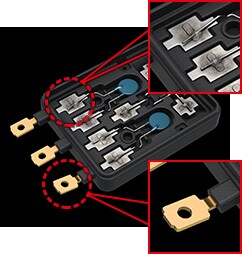
(color image)
![[A][B]](/Images/ss_visionbasics_e_auto_081_1962936.jpg)
(height image)
Automotive sensor base solder inspection
Measure the height of solder using a 3D camera.
Key inspection points
Solder inspection was difficult with 2D cameras. 3D cameras can measure height, so solder can be inspected accurately. Use the height extraction function that converts 3D height images into gray-scale images (mm → shade) to generate a cross-sectional image at a specified height, such as 0.1 mm above the PCB surface. Using the cross-sectional area and shape of the image achieves stable fillet inspection.
Recognition result with a 3D camera
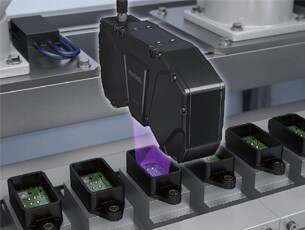
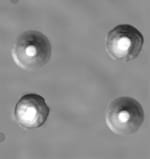

3D inspection of welding status
Judge welding status using a laser displacement sensor and 3D vision inspection.
Key inspection points
Measuring welding width or gaps may not be stable with an area camera depending on the surface conditions. The combination of a laser displacement sensor and an image processing system enables accurate judgment using a 3D image based on height information.
Recognition result with a laser displacement sensor and 3D measurement
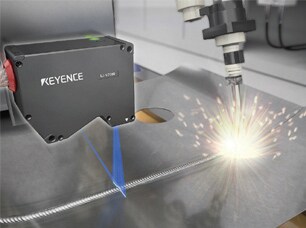
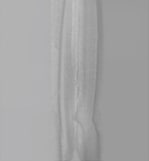
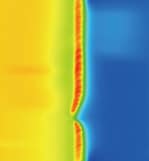