Improved Profitability Through Labor Saving and Reliability
Maintaining quality and reducing costs through the introduction of an image processing system
Improving production efficiency and increasing production volume will surely lead to profit expansion. There is, however, a balance between supply and demand, and you cannot continue increasing supply without limit. There is another approach to improving profitability: reducing production costs. This is more than simply reducing costs. You have to reduce costs while maintaining quality. Reducing costs only while maintaining the trust of customers and users can be expressed as "saving labor without sacrificing reliability." This page describes a method of saving labor without sacrificing reliability by using an image processing system.
How to save labor while maintaining quality levels?
There are two approaches to expand production profit: increasing production volume and reducing production costs. The approach of increasing production volume to improve profitability was described in "Improved profitability by increased production takt/equipment takt." This page focuses on the approach of reducing production costs.
Modern manufacturing has to offer high quality levels and inspection has become indispensable in every process. This requires expensive inspection equipment, and 100% inspection has become necessary to prevent the outflow of defective workpieces. As a result, labor costs and equipment investments for inspections are increasing.
For these reasons, it is extremely difficult to achieve both high quality and low cost. Maintaining quality inevitably requires certain costs. Inspection using an image processing system can be a solution for the issue of achieving both high quality and low cost.
100% inspection through the use of an image processing system
Inspections have become a heavy burden on the production sites that have to provide high quality. An increasing number of companies have been introducing image processing systems as a remedy for this problem. Using an image processing system to conduct inspections that are done visually will significantly reduce labor costs. Image processing allows inline inspection, which is effective for yield rate improvement and enables 100% inspection.
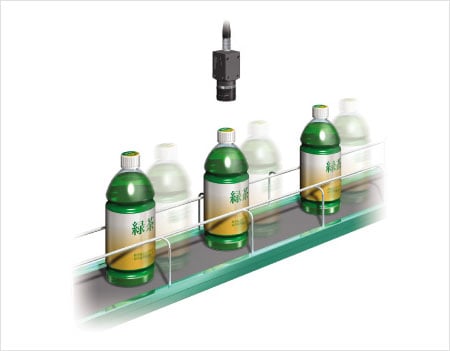
Have you ever experienced problems like these?
If you have experienced any of the following, you can expect to see profitability improvements by introducing an image processing system.
- Inspection cannot keep up with production speed, so sample inspection is conducted visually.
- The production volume is too large to perfectly prevent the outflow of defective workpieces.
- The defects are small and there seems a limit to finding them with visual inspection.
- An image processing system has been introduced, but there are some concerns about the accuracy, so visual inspection is still performed as well.
- The introduction of dedicated inspection equipment has been considered, but visual inspection is still used because the equipment is expensive.
- Although 100% inspection has been conducted, inspection personnel cannot be assigned to all processes.
A high-speed, high-pixel image processing system will solve your problems.
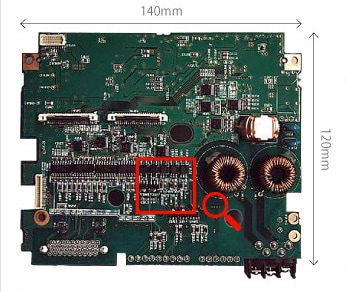
Capabilities of a 21 megapixel camera
A large capacity image of 21 million effective pixels (5104 x 4092 pixels) can be transmitted quickly at 16x speed, just 110 ms. This allows detection of minute defects or details on large targets, which were impossible with conventional cameras.

0.31 megapixel
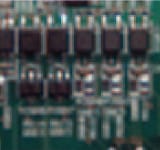
The entire image looks blurred and nothing can be identified
5 megapixels
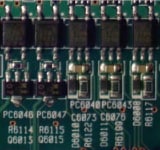
The profiles of chips appear blurred and accurate detection is difficult.
21 megapixels
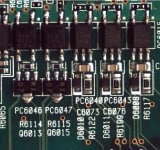
Everything is clear and detailed, so accurate judgment is possible.
It was difficult to use common 0.31 or 2 megapixel cameras to conduct inspection that satisfies requirements for high accuracy. Their transmission speed and processing speed were limited and 100% inspection was sometimes impossible on high-speed lines.
To solve these problems, KEYENCE added an ultra high-pixel camera delivering 21 megapixels (5104 x 4092) to the lineup. 16x high-speed transfer in 109.9 ms allows detection of minute defects even during inline inspection. Large targets or multiple targets can be captured as one image, which helps improve the efficiency of inspections.
Example of improved profitability through high accuracy and reliability
This section introduces a calculation formula for simple estimation of improved profitability through high-accuracy 100% inspection. Please try it to get an estimation of the effect on your production. You can use the profitability improvement calculation sheet below by just typing in the appropriate numbers.
Profitability improvement calculation
Gross productivity ÷ Individual inspection capability × Labor cost + Cost for preventing defective products = Profit improvement effect
【①】products/month ÷ 【②】products/month × $【③】/month + $【④】 = $【 】/monthly of reduced labor + Improved reliability
Profitability improvement calculation sheet
① Gross productivity | products/month | |
---|---|---|
② Individual inspection capability | products/month | |
③ Labor cost | $/month | |
④ Cost for preventing defective products | $ | |
$0 /monthly of reduced labor + Improved reliability
Please enter a numeric value
{item} is required.
{item} must be a positive values.
{item} must be an integer.
Calculation example
Assume that the total production volume is 10,000 products/month. The inspection capacity per worker is 1,000 products/month and labor costs and costs of preventing the outflow of defective workpieces are $2,000 each. The effect of profitability improvement can be calculated as follows:
10,000 products/month ÷ 1,000 products/month x $2,000 /month + $2,000 /month = $22,000/month of reduced labor + Reliability
Monthly cost reduction of $22,000 + reliability is unaffected!