What is Plastic Forming?
- 1. Overview
- 2. Types of Plastic Forming
- 3. Overview of Plastic Forming Machines
- 4. Precautions for Plastic Forming
1. Overview
Metalworking using machines and machine tools includes cutting using a lathe, plastic forming, and welding. When grouped with other such metalworking techniques, plastic forming is also called stamping and makes the designed shapes by pressing the material into a die. This processing method utilizes the plasticity—the characteristic that a material remains in the shape it is changed to by the application of a certain force—of metals and other solids. Plastic forming is primarily used in the metalworking of steel materials such as those for automobile parts. Unlike cutting with a lathe, this method does not produce chips and also allows mass production of the same parts through mold pressing.
2. Types of Plastic Forming
There are two types of plastic forming: Cold-plastic forming, which is performed at ambient temperatures, and hot-plastic forming, which uses heat. When heated, metal undergoes thermal expansion and changes shape. As such, cold-plastic forming is used whenever possible, and hot-plastic forming is used only when the material of the target being produced is hard.
In addition to the pressing methods mentioned above, some examples of other types of plastic forming include forging for manufacturing nuts and bolts; extrusion, wire drawing, and pultrusion for forming wire materials and pipes; deep drawing for creating spherical surfaces in metal sheets; bending for producing leaf springs; riveting for securing assemblies in place; and shearing for cutting metal sheets.
Punch (top)
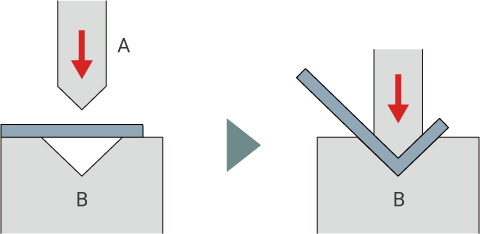
Die (bottom)
- A
- Pressure (press)
- B
- V groove
3. Overview of Plastic Forming Machines
In general, plastic forming machines mold materials by pressing them against dies attached to the press. A high-speed press can stamp materials several thousand times a minute. Other machines include transfer presses, which can form a number of parts at once through the alignment of dies, and roll forming machines, which continuously press roll materials.
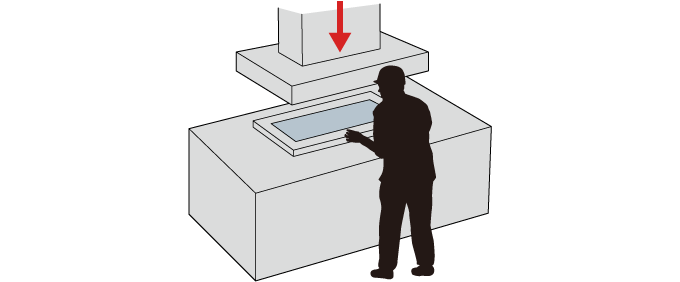
4. Precautions for Plastic Forming
Large plastic forming machines can apply tens of thousands of tons of force to material. In practice, the strength of the force to be applied is determined based on the material; the minimum required force for forming, friction, and other factors are calculated before the process. Meanwhile, the material may deform or break during the forming process, and in order to prevent that, it is necessary to know the limits of bending or deep-drawing the material. The force used for forming must also be minimized so that damage to the material can be prevented.
On the stamping work floor, for small lots of different parts, an operator manually places the material and forms parts in each process. This is called a “single-shot press” system. On the other hand, for mass production, a “progressive press” system is used where coil materials are loaded and transferred in order through multiple press processes. Another kind is the “transfer press” system, which combines the advantages of both the single-shot press and progressive press to enable continuous automatic processing.