Cutting Tools
1. Tool Bits
Tool bits are blades used when cutting workpieces on a lathe. While there are a wide variety of types, the most commonly used tool bits for cutting are roughing tools for cutting the outer diameter, parting tools for grooving, and internal boring tools for making holes.
Additionally, throwaway tool bits with replaceable blades are currently popular due to the reduced hassle from not having to sharpen the blades. These types have a two-part structure that includes the tool holder and the blade tip. Once the cutting edge of the tip becomes dull, it can be replaced like the blade of a utility knife.
attached to a tool holder

2. Chucks
The chuck is the clamping part of the lathe or drill press. In a lathe, the chuck is the part that holds the workpiece in place. In a drill press, it is the part that restrains the drill blade.
Chucks fix the workpiece in a variety of ways, such as mechanical chucks that clamp through a mechanical structure, magnetic chucks that fix the workpiece with a magnet, and vacuum chucks that hold the workpiece in place with a vacuum—all of which are selected according to the differences in mechanisms and applications. Mechanical chucks come in two types―one that restrains with three jaws, and one that uses four jaws.
Precision machining using a lathe or drill press requires a chuck that keeps workpieces and tools completely immobile even in the face of large loads.
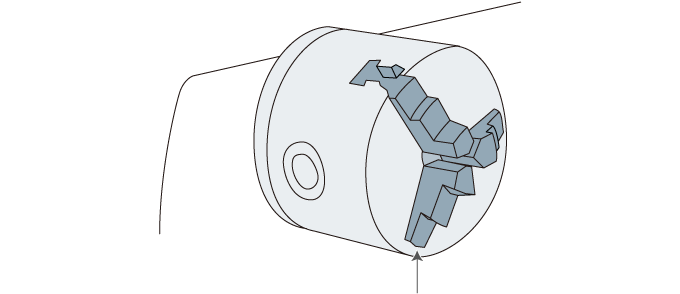
3. Cutting Tools Materials
The material cutting tools are made of is called tool steel, which is characteristic of hardness, resistance to abrasion and impact, and shape retention under elevated temperatures. There are a variety of different tool steels; one is carbon steel (plain-carbon steel), which is made of an alloy of carbon and steel. Today, tool steels with high levels of cleanliness, as well as stable mechanical and thermal treatment properties, are commonplace.
Typical tool steels include high-speed steels and carbide alloys. High-speed steels are alloys that contain tungsten or chromium in carbon steel. They are widely used in cutting thanks to their flexibility in shaping tips to suit the application. Its shortened name, “HSS,” is often used on manufacturing work floors. Carbide alloys, on the other hand, contain tungsten carbide and other components, and are used for machining hard workpieces and dies.