Cutting Formulas
This page introduces formulas for calculating basic parameters necessary for machine cutting. The figures obtained from the calculations are for reference only. The conditions for machining depend on the machine tool you are using. Use the optimal conditions according to your actual machining circumstances.
- Cutting Speed (vc)
- Feed (f)
- Machining Time (Tc)
- Theoretical Finished Surface Roughness (h)
- Net Power (Pc)
- Kc Values (Cutting)
Cutting Speed (vc)
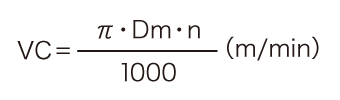
- π (3.14): Circular constant
- Dm (mm): Diameter of workpiece
- n (min-1): Spindle speed
- memo
-
This formula is used to calculate the cutting speed from the spindle speed and the diameter of the workpiece.
Example:
Diameter (Dm) = 60 mm
Spindle speed (n) = 500 min-1
In this case, the cutting speed (vc) is approximately 94 m/min.
Feed (f)
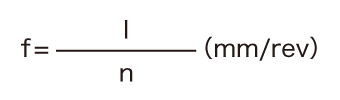
- l (mm/min): Machined length per minute
- n (min-1): Spindle speed
- memo
-
This formula is used to calculate the feed rate per revolution from the spindle speed and the length cut per minute.
Example:
Machined length per minute (l) = 150 mm/min
Spindle speed (n) = 600 min-1
In this case, the feed rate per revolution (f) is 0.25 mm/rev.
Machining Time (Tc)
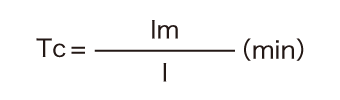
- lm (mm): Length of workpiece
- l (mm/min): Machined length per minute
- memo
-
This formula is used to calculate the machining time from the length of the workpiece and the spindle speed.
Example:
Feed (f) = 0.2 mm/rev
Spindle speed (n) = 1100 min-1
Length of workpiece (lm) = 120 mm
First, the machined length per minute is calculated, in this case from the rotational speed and the feed amount.
Machined length per minute (l) = n × f
= 0.2 × 1100 = 220 mm/min
Substitute this into the formula:
Tc = lm ÷ l
= 120 ÷ 220
= 0.55 (min) × 60
= 33 (sec)
The machining time (Tc) is approximately 33 seconds.
Theoretical Finished Surface Roughness (h)
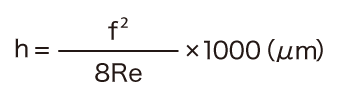
- f (mm/rev): Feed per revolution
- Re (mm): Insert’s corner radius
- memo
-
This formula is used to calculate the theoretical finished surface roughness from the blade corner radius of the insert and the feed per revolution.
Example:
Feed per revolution (f) = 0.1 mm/rev
Insert’s blade corner radius (Re) = 0.5 mm
In this case, the theoretical finished surface roughness (h) is 2.5 µm.
Net Power (Pc)
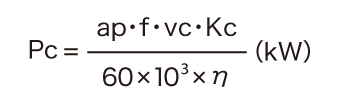
- ap (mm): Depth of cut
- f (mm/rev): Feed per revolution
- vc (m/min): Cutting speed
- Kc (MPa): Specific cutting force
- η: Machine efficiency
- memo
-
This formula is used to calculate the net power from the depth of cut, the feed per revolution, the cutting speed, the specific cutting force, and the machine efficiency.
Example:
Depth of cut (mild steel: ap) = 5 mm
Feed per revolution (f) = 0.1 mm/rev
Cutting speed (vc) = 140 m/min
Machine efficiency (η) = 80% (0.8)
Given:
Specific cutting force (Kc) = 3610 MPa
In this case, the net power for machining (Pc) is 5.26 kW.
Kc Values (Cutting)
Workpiece material | Tensile strength (MPa) and stiffness | Specific cutting force Kc (MPa) for each feed | ||||
---|---|---|---|---|---|---|
0.1 (mm/rev) | 0.2 (mm/rev) | 0.3 (mm/rev) | 0.4 (mm/rev) | 0.6 (mm/rev) | ||
Mild steel (SS400, S10C, etc.) | 520 | 3610 | 3100 | 2720 | 2500 | 2280 |
Medium steel (S45C, S50C, etc.) | 620 | 3080 | 2700 | 2570 | 2450 | 2300 |
Hard steel (S55C, S58C, etc.) | 720 | 4050 | 3600 | 3250 | 2950 | 2640 |
Tool steel (Carbon tool steel (SK), etc.) | 670 | 3040 | 2800 | 2630 | 2500 | 2400 |
Tool steel (Alloy tool steel (SKS), etc.) | 770 | 3150 | 2850 | 2620 | 2450 | 2340 |
Chrome-manganese steel (Manganese carbide (MnC), etc.) | 770 | 3830 | 3250 | 2900 | 2650 | 2400 |
Chrome-manganese steel (Manganese carbide (MnC), etc.) | 630 | 4510 | 3900 | 3240 | 2900 | 2630 |
Chrome molybdenum steel (SCM grades, etc.) | 730 | 4500 | 3900 | 3400 | 3150 | 2850 |
Chrome molybdenum steel (SCM grades, etc.) | 600 | 3610 | 3200 | 2880 | 2700 | 2500 |
Nickel chrome molybdenum steel (SNCM415, etc.) | 900 | 3070 | 2650 | 2350 | 2200 | 1980 |
Nickel chrome molybdenum steel (SNCM439, etc.) | 352HB | 3310 | 2900 | 2580 | 2400 | 2200 |
Hard cast iron | 46HRC | 3190 | 2800 | 2600 | 2450 | 2270 |
Meehanite cast iron (FC350, etc.) | 360 | 2300 | 1930 | 1730 | 1600 | 1450 |
Gray cast iron (FC250, etc.) | 200HB | 2110 | 1800 | 1600 | 1400 | 1330 |