Vision Systems
- Vision System with Built-in AI VS series
- Intuitive Vision System CV-X series
- Customizable Vision System XG-X series
- GigE camera and lighting for PC-based machine vision VJ series
- Inline 3D Inspection 3D Vision series
- 3D Vision-Guided Robotics 3D VGR series
- Line Scan Technology Line Scan series
- 2D Vision-Guided Robotics 2D VGR series
- LED Lighting CA-D series
- Lenses (for Machine Vision) CA-L series
- Machine Vision System Database VisionDatabase series
- Automotive
- Automation Equipment/Machine Building
- Electric Vehicles
- Medical Device Manufacturing
- Food/Beverage Packaging
- Semiconductor/Manufacturing Electronics
- Vision-Guided Robotics
- Solar
- Logistics
- Commodities
- Paper Manufacturing
- Machine Tools
- Electronic Device
- Printing
- Mining/Metals
- Fabric/Textile
- Tobacco
- Marine
- Aerospace
Fill-Level Inspection for the Food and Beverage Packaging
Inadequate and uneven bottle filling can lead to customer dissatisfaction and costly product recalls. KEYENCE offers quality vision systems for the food and beverage industry, ensuring accurate fill-level inspection to help manufacturers verify that each bottle meets the required standards.
We’re here to provide you with more details.
Reach out today!
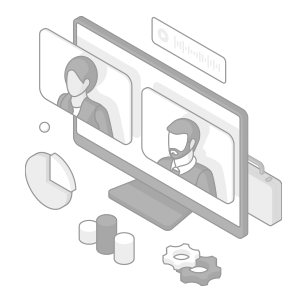
Vision Systems for Beverage Fill Level Inspection
Our machine vision systems ensure product quality in bottling factories by checking capping, labeling, and packaging while verifying fill levels. Use our solutions to quickly detect underfilled or overfilled bottles on conveyor tracks.
CV-X Series
The intuitive vision system CV-X Series combines powerful cameras, advanced lighting function, and other features in addition to intuitive interactive menus. These combinations help operators complete advanced bottle fill level inspection tasks easily.
VS Series
Our Vision System with Built-in AI packs software algorithms and advanced functions that let you train the system on accurate fill level. The system gets smarter at detection as it works more with inspection data.
2D VGR Series
The 2D VGR Series is a 2D Vision-Guided Robotics system that can be incorporated into bottle fill level inspections. Use it to automate secondary packaging handling or pick incorrectly filled bottles off the conveyor line.
Curious about our pricing?
Click here to find out more.
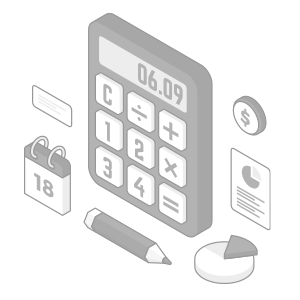
Challenges in Bottle Fill Level Inspection
Lighting Conditions
Overwhelming or underwhelming lighting conditions can affect inspection accuracy and analysis. With advanced illumination and AI algorithms, our vision system can adjust to different lighting conditions, ensuring bottles and inspection environments are well-lit.
Bottle Sizes and Shapes
Defective bottles can make accurate liquid level inspection difficult. Our intuitive vision systems can easily be programmed to recognize defective bottles and route them off the line, ensuring overall fill-level inspection integrity.
Production Speed
An inspection that can't keep up with the speed of filling systems is not useful. Our vision products have quick capture speeds thanks to their inherent rapid nature and the addition of advanced and proprietary features.
Foam Formation
In carbonated drinks, bubbles and foaming can “confuse” an inspection system. Use both the rule-based and AI inspection configurations in our vision systems to take care of all variables.
Discover more about this product.
Click here to book your demo.
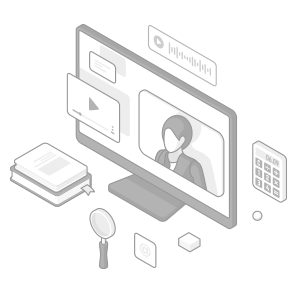
FAQs about Liquid Fill Level Inspection
What Are the Benefits of Vision Systems for Fill-Level Inspections in the Food and Beverage Industry?
By monitoring liquid levels, ingredient consistency, and color uniformity, vision systems enhance inspection accuracy and speed while minimizing contamination risks in food and beverage production.
How Is a Fill-Level Inspection Performed for Various Types of Containers?
Bottle fill-level inspections can use vision inspection, x-ray inspections, check weighing, or a combination. The best method for your production line depends on product type, packaging material, and required accuracy.
How Does Fill-Level Inspection Contribute to Improved Product Quality and Reduced Waste?
Manufacturers protect their brand reputation by detecting and rejecting underfilled or overfilled bottles early and ensuring consumers receive quality and consistency. This process reduces waste and end-of-the-line costs.
How Do Vision Systems Handle Inconsistencies in Liquid Level Detection in PET Bottles?
Advanced software algorithms, lighting adjustments, and necessary calibrations are some ways vision systems reliably address fill-level inconsistencies in PET bottles, despite the presence of bubbles.
How Does Automated Fill-Level Inspection Reduce Labor Costs and Time Compared to Manual Methods?
Automated fill-level inspection uses cameras and image processing to measure fill levels, defects, and more, reducing labor costs. These systems enhance efficiency and throughput compared to manual methods.
We’re here to provide you with more details.
Reach out today!
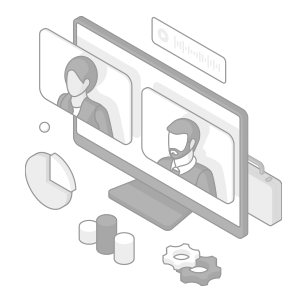
Related Downloads
Related Products
Industries
- Automotive
- Automation Equipment/Machine Building
- Electric Vehicles
- Medical Device Manufacturing
- Food/Beverage Packaging
- Semiconductor/Manufacturing Electronics
- Vision-Guided Robotics
- Solar
- Logistics
- Commodities
- Paper Manufacturing
- Machine Tools
- Electronic Device
- Printing
- Mining/Metals
- Fabric/Textile
- Tobacco
- Marine
- Aerospace