Vision Systems
- Vision System with Built-in AI VS series
- Intuitive Vision System CV-X series
- Customizable Vision System XG-X series
- GigE camera and lighting for PC-based machine vision VJ series
- Inline 3D Inspection 3D Vision series
- 3D Vision-Guided Robotics 3D VGR series
- Line Scan Technology Line Scan series
- 2D Vision-Guided Robotics 2D VGR series
- LED Lighting CA-D series
- Lenses (for Machine Vision) CA-L series
- Machine Vision System Database VisionDatabase series
- Automotive
- Automation Equipment/Machine Building
- Electric Vehicles
- Medical Device Manufacturing
- Food/Beverage Packaging
- Semiconductor/Manufacturing Electronics
- Vision-Guided Robotics
- Solar
- Logistics
- Commodities
- Paper Manufacturing
- Machine Tools
- Electronic Device
- Printing
- Mining/Metals
- Fabric/Textile
- Tobacco
- Marine
- Aerospace
Bottle Cap Inspection for Food and Beverage Packaging
Untightened caps, cracks or defects, and misassembly are challenges faced during bottle capping and bottle cap inspection in food and beverage packaging. Manufacturers require vision systems that easily integrate into their existing production lines and inspect for these issues without disruption.
KEYENCE offers a line of vision systems to help ensure proper cap sealing to prevent contamination during final assembly or spillage during shipping.
We’re here to provide you with more details.
Reach out today!
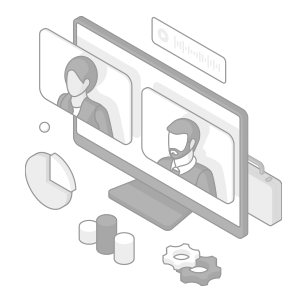
Challenges in Bottle Cap Inspection
Incorrect Cap Placement
Incorrect cap placement and improperly torqued safety rings can signify issues with the closure machine or other systems. It can be challenging to find a bottle cap closure inspection system that checks proper cap sealing and seating.
Correct Torque Requirement
Ensuring every cap is tightened to the correct torque requirement and specification can be challenging for the capping machine. Finding vision systems that check for torque consistency can be equally challenging.
Wear and Tear
Quality plastic cap defect inspection becomes crucial when capping heads have suffered wear and tear, leading to inconsistent cap tightness. Also, tiny cracks may be present through which contamination can enter, or leakages can happen.
Damage to Bottle Threads
Detecting damage to bottle threads and safety rings caused by inconsistencies in the operation of a capping machine can surprisingly be difficult for line operators to detect due to quantity and fast-moving line speeds.
Discover more about this product.
Click here to book your demo.
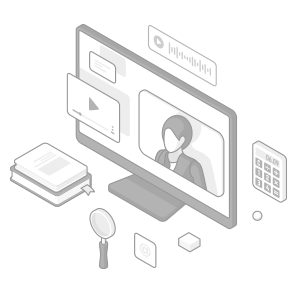
Vision Systems for Plastic Cap Defect Inspection
KEYENCE has been providing solutions to the challenges faced in packaging food and beverage products through advanced automation and vision systems. We have product solutions that ensure accurate plastic cap defect detection, including tiny cap cracks that can introduce contaminants and pose significant health challenges to consumers. Our solutions come equipped with the industry’s latest technologies and configurations that accurately check for cap presence and detect imperfections in plastic caps.
Vision System with Built-in AI
AI vision systems use algorithms to accurately identify defects, solve inspection issues related to misaligned caps, and other flaws.
Intuitive Vision System
Systems for bottle cap closure inspection must offer ease of use for human operators. Intuitive vision systems like the CV-X Series allow line operators to make advanced inspections through interactive menus.
LumiTrax™ Technology
LumiTrax™ technology provides advanced illumination through the use of LEDs and optical filters to create high contrast imaging so tiny cracks and other minor mishaps are detected even under poor lighting.
Vision-Guided Robotics With Improved Stability
A bottle capping robot becomes problematic when it can’t accurately feed caps, receive bottle trays, and place caps due to the absence of the right vision guidance system. 2D vision-guided robotics eliminate this challenge.
Curious about our pricing?
Click here to find out more.
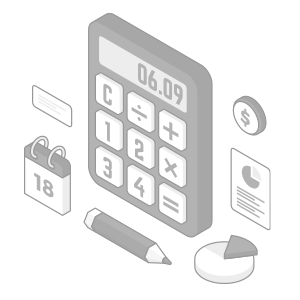
FAQs about Plastic Cap Quality Inspection
What Role Does Bottle Cap Inspection Play in Preventing Leakage and Ensuring Product Freshness?
Bottle cap closure inspection verifies tightness, detects cracks in caps, and checks cap alignment to ensure no contamination, ensuring product freshness.
What Are the Advantages of Using Vision Systems for Plastic Cap Defect Inspection in Beverage Production?
Using vision systems in cap defect inspection helps detect deformities like dents that could lead to leakage and introduce contaminants.
How Does Plastic Cap Appearance Quality Ensure Product Integrity and Consumer Safety?
Cap appearance quality inspection helps human operators remove products from final assembly that are leaking from caps, making only contaminate-free products available to consumers.
Can Bottle Cap Closure Inspection Systems Detect Improper Sealing and Alignment Issues?
Yes, bottle cap enclosure inspection systems check for even slight irregularity in the position, shape, and appearance of caps, exposing sealing and alignment issues.
How Do Plastic Cap Inspection Vision Systems Perform in Environments With High Levels of Dust or Moisture, Typical in the Food and Beverage Sector?
Vision systems for food and beverage packaging come equipped with build quality, IP67, or enclosures that make them resistant to dust and moisture.
We’re here to provide you with more details.
Reach out today!
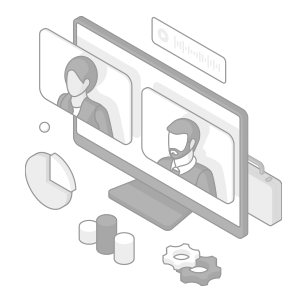
Related Downloads
Related Products
Industries
- Automotive
- Automation Equipment/Machine Building
- Electric Vehicles
- Medical Device Manufacturing
- Food/Beverage Packaging
- Semiconductor/Manufacturing Electronics
- Vision-Guided Robotics
- Solar
- Logistics
- Commodities
- Paper Manufacturing
- Machine Tools
- Electronic Device
- Printing
- Mining/Metals
- Fabric/Textile
- Tobacco
- Marine
- Aerospace