Vision Systems
- Vision System with Built-in AI VS series
- Intuitive Vision System CV-X series
- Customizable Vision System XG-X series
- GigE camera and lighting for PC-based machine vision VJ series
- Inline 3D Inspection 3D Vision series
- 3D Vision-Guided Robotics 3D VGR series
- Line Scan Technology Line Scan series
- 2D Vision-Guided Robotics 2D VGR series
- LED Lighting CA-D series
- Lenses (for Machine Vision) CA-L series
- Machine Vision System Database VisionDatabase series
- Automotive
- Automation Equipment/Machine Building
- Electric Vehicles
- Medical Device Manufacturing
- Food/Beverage Packaging
- Semiconductor/Manufacturing Electronics
- Vision-Guided Robotics
- Solar
- Logistics
- Commodities
- Paper Manufacturing
- Machine Tools
- Electronic Device
- Printing
- Mining/Metals
- Fabric/Textile
- Tobacco
- Marine
- Aerospace
Differential Gear Inspection for the Automotive Industry
Gear inspection solutions help automotive manufacturers achieve production standards that boost performance, safety, and durability. Our vision solutions have helped many manufacturing and production lines prevent defective and damaged products from entering the market.
Vision systems with built-in AI couple powerful algorithms with rules-based programming to achieve accurate inspection results on diverse surfaces at speeds of up to 142,800 lines per second. Focusing on stability and durability, our differential gear inspection solutions provide consistent results.
We’re here to provide you with more details.
Reach out today!
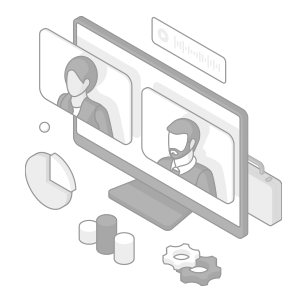
Challenges in Gear Inspection
Limited Visibility
An automotive differential gear is made up of many parts, including pinion gears and ring gears. These parts and other components are tightly packed, making gear inspection challenging.
Complexity of Components
Whether open, locking, limited-slip, or a torque-vectoring differential, every type of gear differential has highly specialized and interdependent components of complex shapes and angles. These intricate components can make inspection difficult to accomplish.
Defect Pattern Analysis
The differential can be exposed to debris, dirt, and metal wear. These foreign materials on gears and components can mimic or come off as wear patterns. This situation can make accurate gear visual inspection difficult.
High-Speed Inspection
It's one thing to have a system that can inspect gears and components at high speeds, but it’s a different matter for the system to simultaneously maintain accuracy and reliability—which can create complications.
Discover more about this product.
Click here to book your demo.
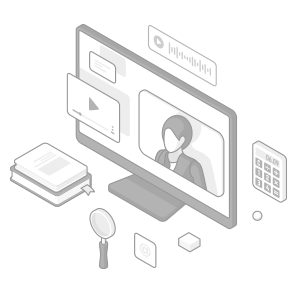
Vision Systems for Differential Gear Inspection
KEYENCE provides a line of gear inspection machine vision systems for automotive manufacturing. Our vision systems provide reliable extraction of even minute defects from high-resolution images captured. Powerful detection algorithms accurately eliminate false positives and false negatives. Our solutions consistently detect defects and irregularities on gear components with shiny, uneven, or rough surfaces.
These differential gear appearance inspection solutions allow manufacturing line operators to isolate the causes of gear imperfections and defective components for intervention. This way, defective products that are prone to failure are stopped from reaching the market.
Vision System with Built-in AI
The VS Series is a game-changing AI vision system for users of all experience levels. Program any inspection with the newly developed VS Creator software. AI and rules-based inspection programming ensure consistent and high-accuracy detections.
Line Scan Technology
KEYENCE vision systems with line scan cameras automatic inspection for defects and contamination, even on uneven surfaces. The line scan camera can capture up to 142,800 lines per second.
Inline 3D Inspection
The XT, an inline 3D Inspection vision system, includes two camera models with a 60 × 60 mm (2.36″ × 2.36″) field of view, a 9+ megapixel sensor, and a large telecentric lens to inspect gear differential parts with accuracy.
Intuitive Vision System
The KEYENCE CV-X Series brings user-friendly, intuitive vision system solutions for all manufacturing and production applications. Coupled with the simple-to-use graphical interface, the high-resolution cameras and sensors ensure stable detection.
3D Vision-Guided Robotics
KEYENCE 3D vision-guided robotics systems feature four powerful cameras, projector lighting, a picking simulator function, and a path planner ideal for assembly automation, machine tending applications, and de-palletizing with unparalleled object detection.
Curious about our pricing?
Click here to find out more.
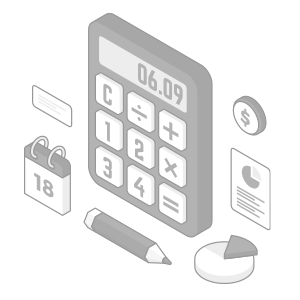
FAQs about Differential Gear Visual Inspection
What Are the Benefits of Using Vision Systems for Differential Gear Inspection?
Using vision systems during the inspection of differential gear and components helps to detect defects and contaminants that affect gear appearance and functionality.
How Do Vision Systems for Inspection Improve Vehicle Performance?
Differentials are a crucial part of vehicle performance. Gear inspection via machine vision helps detect and classify damages like cracks, wear, and breaks for necessary intervention.
What Common Issues Can Be Identified Through Differential Gear Visual Inspection?
Common issues that differential gear inspection exposes include cracks, breaks, and other visual imperfections that could make a vehicle underperform or fail.
Can Gear Inspection Solutions Prevent Differential Gear Failure?
Yes, gear inspection systems before final assembly help to detect errors that could lead to gear failure when in use.
What Are the Advantages of Using a 3D Vision System Over Traditional Methods for Gear Inspection?
3D vision systems offer more accurate measurements than manual gear inspection by using multiple industrial cameras and advanced computer vision algorithms to capture and analyze data.
We’re here to provide you with more details.
Reach out today!
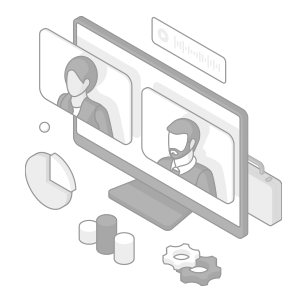
Related Downloads
Related Products
Industries
- Automotive
- Automation Equipment/Machine Building
- Electric Vehicles
- Medical Device Manufacturing
- Food/Beverage Packaging
- Semiconductor/Manufacturing Electronics
- Vision-Guided Robotics
- Solar
- Logistics
- Commodities
- Paper Manufacturing
- Machine Tools
- Electronic Device
- Printing
- Mining/Metals
- Fabric/Textile
- Tobacco
- Marine
- Aerospace