Optical Comparator (Profile Projector)
Dimensional Inspection for Plastic Forming
Browse our types of plastic forming machines. Forming machines draw out the necessary length of coil material & automatically process it into the desired part at high speeds.
Overview and Characteristics
Equipped with capabilities of stamping, bending, and cutting, a forming machine can continuously manufacture parts like springs, clips, rings, and coils from wire materials and band plates. Before the emergence of forming machines, parts needed to be finished through numerous processes after the wire material was cut. This caused increased material waste and longer processing times. In contrast, forming machines draw out the necessary length of coil material and automatically process it into the desired part at high speeds. Forming machines can also use materials without any waste and can continue manufacturing with no changeovers.
We’re here to provide you with more details.
Reach out today!
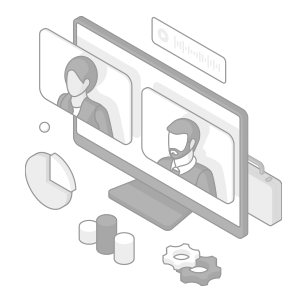
Application and Assembly
Today, metal parts produced by forming machines cover a range of products, including automobile parts, electric and electronic components, metal building materials and fittings, and stationary. The specialized forming machines used to manufacture springs are called wire forming machines or spring forming machines. In recent years, forming machines have increasingly adopted computer numerical control (CNC) and multi-functionality in order to manufacture parts with complex shapes precisely and quickly using servo motor control. Furthermore, some newer models offer all inclusive functions that range from bending to riveting and welding to assembly.
Discover more about this product.
Click here to book your demo.
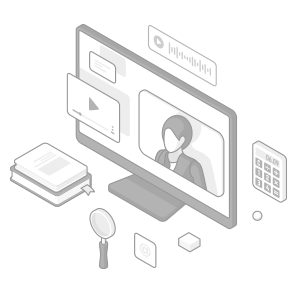
Standard Plastic Forming Machine
Standard plastic forming machines use pneumatic or hydraulic methods to form wires. They use computer numerical control (CNC) to control the movement of the machine. The pneumatic method uses pressurized air or gas as the power in the CNC machine, and the hydraulic method uses pressurized oil or water.
We’re here to provide you with more details.
Reach out today!
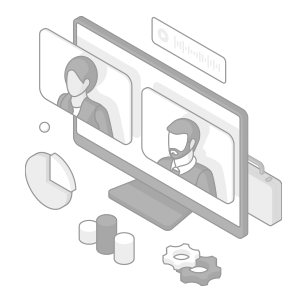
Four-Slide Plastic Forming Machine
A four-slide plastic forming machine is a machine that combines the forming process with other machining. “Four slide” refers to how the machine has four axes that it processes with. Because of the four axes, it can use four tools at once. This expedites the forming process by completing it in fewer steps and with less energy than a standard machine.
Discover more about this product.
Click here to book your demo.
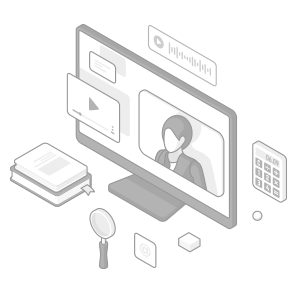
Plastic Forming Process
The plastic forming process involves four steps: drawing, straightening, forming, and finishing. First is drawing, which is when the wire is pushed through a die and pulled out on the other end. This first step makes the wire thinner.
Next is straightening, which is when the wire is straightened to remove any deformities. Then comes forming, where the machine shapes the wire. Lastly is the finishing process, where the wire receives extra processes to improve appearance, corrosion resistance, or electrical conduction.
We’re here to provide you with more details.
Reach out today!
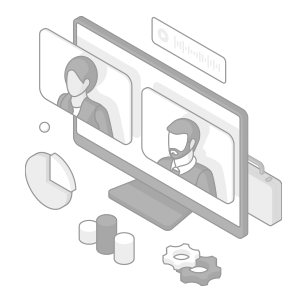
Measuring Formed Parts
Before and after a wire goes through the plastic forming process, it needs to be measured. Using an optical comparator to measure wires is ideal because wires are so thin and hard to measure with handheld devices. KEYENCE’s optical comparator options, called image measurement systems, the IM Series, which can measure a wire’s outer diameter, pitch diameter, and other GD&T measurements.
The IM is simple, it only requires placing the wire onto the stage and pressing the measure button. The stage holds up over 100 parts, and the IM auto positions its camera so the wire is consistently measured at any angle.
Related Downloads
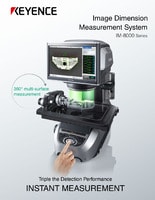
Brochure for the IM-8000 Series Image Dimension Measurement System. Accurately measure parts in seconds at the push of a button.