Coding in Dairy Packaging with UV Laser Technology
KEYENCE UV laser coders bring advanced technology to printing and coding in dairy packaging. It seamlessly replaces traditional thermal transfer overprinters (TTO) without requiring changes to packaging films or machinery. Sharp, reliable codes are achieved while eliminating waste, consumable costs, downtime, and maintenance associated with ink ribbons and other components.
UV Laser Coding and Marking in Dairy Packaging
The FP-1000 Series UV laser coder excels in dairy packaging, adapting seamlessly to multi-layer films, foils, laminated wraps, and paper-based options.
- Cheese bags, pouches, and wrappers
- Dairy pouches
- Yogurt lids or containers
- Sour cream tubs
- Frozen ice cream or popsicle wrappers
- Creamer pods
We’re here to provide you with more details.
Reach out today!
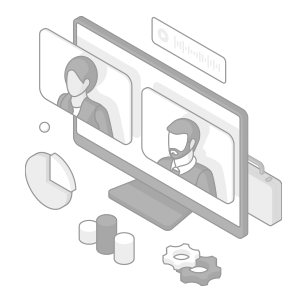
Dairy Packaging-Specific Challenges Solved by FP-1000 Series Technology
Costly Consumables
Marking methods like thermal transfer overprinting (TTO) rely on consumables such as ink ribbons and print heads, driving up costs and waste. An FP-1000 Series laser coder uses light-based marking, eliminating consumables and cutting operational expenses.
No ink ribbon costs
No head replacement costs
Downtime & Production Interruptions
Replacing ink ribbons and worn parts in TTO systems causes frequent interruptions in production lines. The FP-1000 Series’ non-contact, maintenance-free technology keeps operations running smoothly with no downtime for part replacements, reducing the risk of errors.
-
1More production in the same amount of operation time
-
2Less operation time for the same production volume
Line conditions:
100 operations/minute, 10 hours/day, 25 days/month, 1 ink ribbon replacement/day at 5 minutes/ribbon replacement.
-
1When operated at the same operation time:
150,000 units more per year
* When producing the same production volume: 1,500 minutes (2.5 days) less per year without the need to replace ink ribbons
Mark Permanence
Dairy packaging often faces challenges with fading, smearing, or illegible markings due to cold and wet storage and handling. UV laser marks are not impacted by water or condensation on the surface of the product resulting in consistent high quality permanent marks to maintain traceability for regulatory compliance.
UV lasers are not affected by traditional causes of marking that fades away:
Oil
Powder
Alcohol
Heat sterilization
Conventional thermal printer
UV laser coder
* Results comparison after rubbing on the marked area of film exposed to powder before marking
Thermal printers
UV laser coders
-
1Laminated surface (transparent)
-
2Marking layer
-
3Other film layers
-
4Sealant layer
Operating energy for packaging line equipment (packaging machine, compressor, air conditioner, lighting, etc.) can be significantly reduced.
Environmental Waste
Traditional marking methods produce consumable waste, adding to environmental impact. The FP-1000 Series’ eco-friendly, consumable-free technology supports sustainable UV laser coding in dairy packaging practices by minimizing waste and energy use.
Disposal loss simulation:
For a facility that replaces four ink ribbons per day, operating at 25 days per month will lead to disposal of 1,200 ink ribbons per year. At 500 grams 17.65 oz per ink ribbon, 1,200 ink ribbons would equal 600 kilograms 1322.76 lb, or about 1.2 tons of CO2 emissions upon disposal. UV laser coders, however, do not use ink ribbons, so the CO2 emissions can be reduced to zero.
Why Choose the FP-1000 Series for Dairy Packaging Marking Needs?
Optimize your UV laser coding and marking in dairy packaging with the FP-1000 Series. Engineered for precision and high speed, it creates permanent, eco-friendly marks without the hassle of downtime or consumable costs. FP-1000 Series coders guarantee long-lasting code durability with their smooth integration and installation design. Contact us today to see how it can revolutionize your diary packaging production line.
Contact us to learn more about how our advanced technology can help take your business to the next level.
Contact Us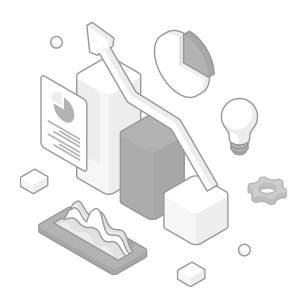
FAQs About UV Laser Technology in Dairy Packaging
How Does UV Laser Coding Improve Efficiency in the Dairy Industry Compared to Conventional Thermal Transfer Overprinters?
Because UV laser coding eliminates consumables, requires less maintenance, and offers faster marking speeds, it guarantees continuous production and reduces operating costs in facilities with dairy packaging laser marking needs.
How Does the FP-1000 Series Ensure Reliable Coding in Environments With High Humidity or Exposure to Liquids Common in Dairy Packaging Facilities?
In challenging coding in dairy packaging conditions, the FP-1000 Series provides consistent, high-quality codes. UV light goes right through water and condensation to mark inside the multilayer films commonly used in packaging with no damage. The FP is also IP65 rated to hold up much better than traditional TTO.
What Features of the FP-1000 Series Help Reduce Operator Errors and Increase Throughput for Dairy Product Coding and Marking?
Intuitive software and seamless integration minimize operator intervention, reduce errors, results in less downtime for part/ribbon replacement, and optimize throughput in high-volume dairy production lines.
How Does the UV Laser Coder Ensure Consistent, Permanent Marking on Dairy Product Packaging?
UV laser coders induce a chemical change in the plastic/pigment layers of packaging to produce durable, sharp marks on dairy packaging materials that are impervious to smudging, abrasion, and environmental influences.
How Does the FP-1000 Series Eliminate Downtime in Dairy Production Lines?
The KEYENCE FP-1000 Series eliminates downtime by having zero consumables and offers maintenance-free operation for continuous, high-speed dairy production.
We’re here to provide you with more details.
Reach out today!
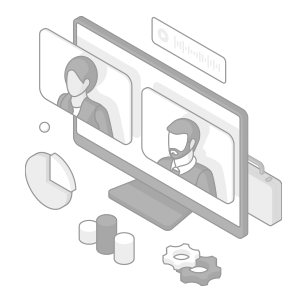