Data Acquisition (DAQ)
Temperature Measurement
Understanding and controlling temperature is crucial in numerous settings, from everyday activities, such as cooking, to using temperature to control industrial processes and scientific research.
Accurate temperature measurement and control is crucial to these activities, and it’s easily accomplished using temperature measurement devices that reflect thermal states in an easily interpreted manner.
This is particularly important in industrial settings where temperature control affects the throughput, energy efficiency, and compliance with industry standards. This makes your choice of temperature measurement tools and instruments crucial for your industrial success.
This section provides an easy-to-understand explanation of thermometers, with the main focus on those used for industrial applications, including their principles and how to select them.
This section also introduces DAQ instruments and technologies to improve measurement accuracy and measures against noise.
Measurement Improvement
- What Is Temperature?
- Basics of Thermocouples
- Basics of Resistance Thermometers
- Basics of Radiation Thermometers
- Latest Information on Temperature Measurement
- Temperature Measurement Glossary
We’re here to provide you with more details.
Reach out today!
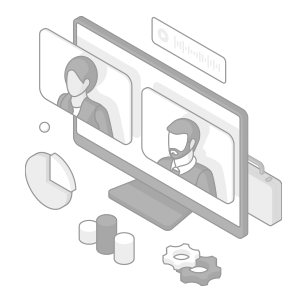
Analysis Improvement
- Basic Knowledge of Temperature Recorders
- Temperature Analysis Improvement
Curious about our pricing?
Click here to find out more.
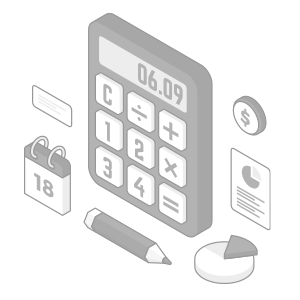
Applications and Examples
We’re here to provide you with more details.
Reach out today!
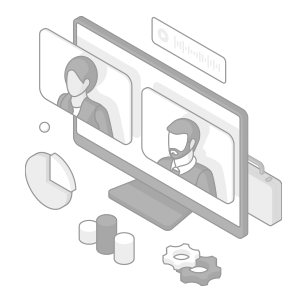
Measuring Temperature
Temperature measurement in an industrial setting involves using specialized tools and instruments designed to provide precise and reliable temperature monitoring across a variety of environments, which may include extreme heat or cold, exposure to corrosive substances, or applications in which direct contact with the measured surface isn’t possible or desirable.
This includes two basic classes of temperature measurement sensors, including contact sensors and non-contact sensors.
Contact sensors, such as resistance temperature detectors (RTDs), thermocouples, and bimetallic thermometers, are characterized by their requirement to physically touch the material being observed.
Non-contact sensors, on the other hand, don’t require physical contact with the surface, making these sensors great for applications that involve fragile and easily damaged materials. Infrared sensors are among the most common non-contact sensors that detect the thermal radiation emitted by an object, allowing the sensor to determine the temperature without physical touch.
Curious about our pricing?
Click here to find out more.
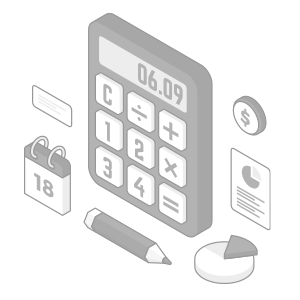
How Do Industrial Thermometers Work?
Industrial thermometers work in pretty much the same way as consumer ones. However, the accuracy rating associated with industrial-grade equipment is often higher compared to consumer goods.
- Thermocouples: These devices rely on the Seebeck effect, where a voltage is generated at the junction of two different metals with different thermal coefficients. The change in voltage is proportionate to the change in temperature. Thermocouples are durable and operate at a wide temperature range, making them perfect for industrial settings.
- RTDs: Resistance temperature detectors’ resistance changes with the temperature fluctuations. They’re quite accurate and stable, which is why they’re often used in industrial processes that require very precise temperature control. It stands to reason, of course, that they’re also pricier than thermocouples. But they’re also significantly more accurate.
- Infrared thermometers: Infrared thermometers pick up the infrared energy emitted by the surface of an object. Infrared isn’t a visible spectrum; instead, it’s perceived as heat. Much in the same way, the heat also generates IR radiation, which is picked up by these sensors. This allows non-contact temperature measurements, which is particularly important for applications in which the sensor can’t physically touch the measured surface.
Discover more about this product.
Click here to book your demo.
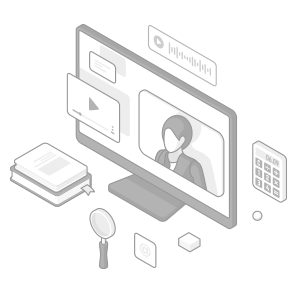
What Does Temperature Measure?
Temperature, in an industrial context, isn’t just a number on a scale; it’s a rather crucial parameter that indicates the status of a particular process, the condition of a product, or the health of the equipment used in operation. Thus, temperature measurement in an industrial setting must be precise, repeatable, and reliable—such data is often used in feedback systems for process control. A good example of this is automated control of heating elements or cooling systems inside the manufacturing or supply chains.
Interested in taking your temperature measurement and control processes to the next level? Contact us today to learn more about our cutting-edge technology and how we can help optimize your operations.
We’re here to provide you with more details.
Reach out today!
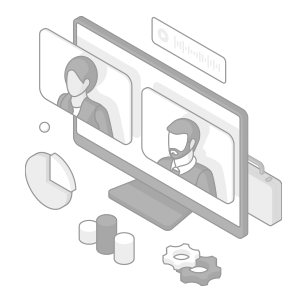
Related Downloads
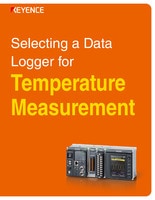
Learn how to check DAQ specifications to choose the ideal DAQ for temperature measurement according to the expected maximum number of input channels, the maximum sampling rate, the longest recording period, and other factors.