Data Acquisition (DAQ)
Fatigue Testing and Analysis
-
Tags:
- Fatigue Testing
Fatigue testing and analysis are critical processes in any material science. Through these methods, the fatigue life and endurance limits of materials can be determined, which, in turn, helps predict when and how failures may occur. By examining materials' stress/strain relationship, engineers can verify that materials can withstand repetitive stresses in real-world applications.
What is Fatigue Analysis? Understanding the Basics
Fatigue analysis studies how materials respond to cyclic loading over time. Unlike static loads, cyclical loads cause progressive damage, even if the material is not experiencing its full weight capacity.
There are three primary methods used to perform a fatigue analysis:
- Stress-Life Method: This method is ideal for high-cycle fatigue scenarios where stress levels remain within the accepted variable range of the material.
- Strain-Life Method: Best suited for low-cycle fatigue, this method is typical when accounting for material deformation, like plastic.
- Linear Elastic Fracture Mechanics (LEFM): This method primarily focuses on the growth of cracks in brittle materials, like ceramic. Measurements are taken of the fracture stress at the crack notch.
Importance of Fatigue Testing in Material Science
Designing reliable and safe components requires a deep understanding of how materials behave under prolonged stress. For example, fatigue tests in the electric vehicle sector ensure that engines and structural parts can withstand millions of loading cycles without issue.
Fatigue testing also contributes to cost efficiency. If a material is not optimal for its chosen stress load, it can result in costly recalls or redesigns. This process allows engineers to identify potential failures early and improve the overall quality of the end product.
Steps to Perform Accurate Fatigue Testing and Analysis
- 1. Define Fatigue Test Parameters: Establish the type of load, stress amplitude, and number of cycles to replicate the environment of the intended material usages.
- 2. Prepare the Material Specimen: Verify that the specimen’s geometry, surface finish, and any other conditions align with the testing requirements.
- 3. Conduct Fatigue Test: Using modular data acquisition and DAQ systems to capture stress/strain relationship data, load frequencies, and failure patterns.
- 4. Visualize Data: Whether through S-N curves or range histograms, a visual must be used to interpret the material’s behavior.
- 5. Perform Post-Processing: Analyze large datasets to identify trends and crack initiation points.
- 6. Validate Results: Compare all test data with predictive models to confirm the material can meet real-world demands.
We’re here to provide you with more details.
Reach out today!
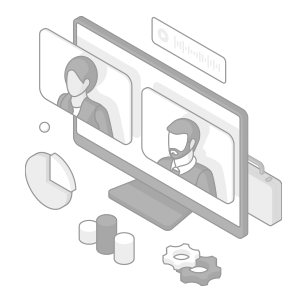
Composite Fatigue Analysis: Key Considerations
Unlike metals, composites are more complex under cyclic loading as they are influenced by factors such as their fiber orientation and interfacial bonding. A critical factor in composite fatigue analysis is understanding how fiber alignment affects performance. A unidirectional composite may excel under specific directional loads but fail when stress is applied in other directions.
Common Challenges in Fatigue Testing and How to Overcome Them
One common issue in fatigue testing is accurately simulating an operational environment. Specifying factors such as temperature and humidity is hard, so these tests must be conducted in multiple scenarios.
There are also challenges in data collection and processing as fatigue testing produces large datasets that require massive modular data acquisition systems and specialized software to be processed effectively.
Benefits of Fatigue Analysis in Product Design
Fatigue analysis helps determine material selection for lightweight and cost-effective designs. It can also help prevent catastrophic failures and lower the risk of costly recalls.
To optimize your fatigue testing and analysis, look no further than KEYENCE. Our advanced systems are fully customizable to handle datasets of any size, efficiently detecting anomalies and delivering real-time alerts.
Contact KEYENCE today to optimize your designs with precise fatigue analysis!
Discover more about this product.
Click here to book your demo.
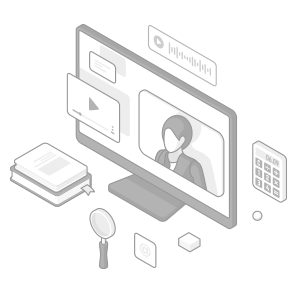