Film and Sheets
Coating for processing film and sheet substrates has been adopted for various purposes, including for state-of-the-art electronic equipment and components, LCD components, and food packaging. Many types of coating equipment are used depending on the purpose.
This section describes the various methods of coating on film and sheet substrates classified according to the purpose of adhesion (lamination) and film-forming (functionalization and surface processing).
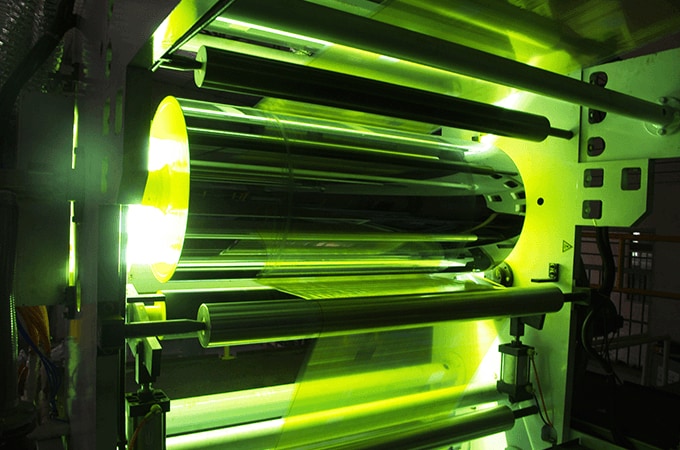
- Adhesion in film and sheet manufacturing
- Functionalization and surface processing in film and sheet manufacturing
Adhesion in film and sheet manufacturing
Adhesion in film and sheet manufacturing refers to the process of bonding multiple substrates together, or bonding a substrate and a material. This process is generally called lamination. Lamination can be broadly divided into dry lamination and extrusion lamination.
Lamination has been used in a wide variety of applications, including operation buttons (membrane switches) of consumer electronics such as washing machines and microwave ovens; hard coat films of resistive film-type pen-input touch panels on information terminals and photocopiers; and retort pouch and other food packaging that utilizes heat resistance.
Dry lamination
Adhesive or pressure-sensitive adhesive is coated over the substrate (first substrate), and the substrate is bonded to other material or another substrate (second substrate). Pressure-sensitive adhesive is used mostly for adhesive films such as protective films, double-sided tape, and transdermal absorption plasters.
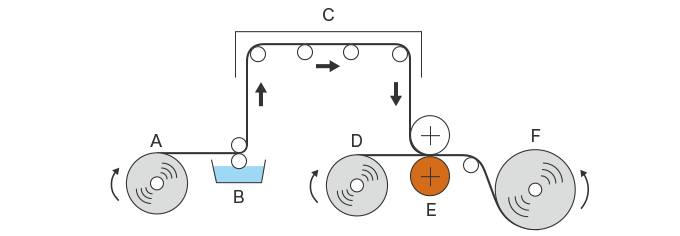
- A. First substrate
- B. Adhesive coating
- C. Drying zone
- D. Second substrate
- E. Heating (steel roll)
- F. Winding machine
Extrusion lamination
Extrusion lamination is an application that utilizes extrusion molding, a type of resin molding technique. The substrate is coated with an adhesion additive (anchor coat), and the material is melted by heat and extruded into a thin, flat sheet through a die with a slit (T-die) as it is applied over the substrate. The material is compressed and solidified by the cooling roller to achieve bonding with the substrate.
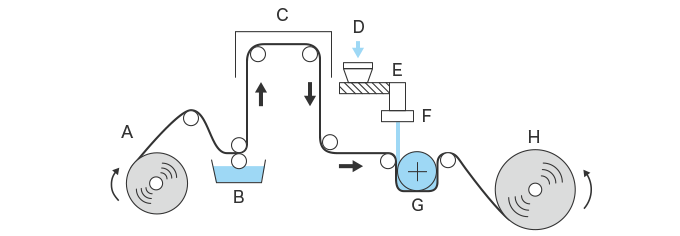
- A. Substrate
- B. Adhesion additive coating (anchor coat)
- C. Drying zone
- D. Material
- E. Extruder
- F. T-die
- G. Cooling (cooling roller)
- H. Winding
Another applied technique of extrusion lamination is "sandwich lamination”. When the material is extruded, the second substrate is fed from an unwinder, and the three layers are bonded. Connecting two sandwich lamination systems makes a "tandem lamination" system that can bond five layers. Such systems are used for multi-layer lamination.
Functionalization and surface processing in film and sheet manufacturing
Coating-based functionalization and surface processing has been used in various industrial fields due to the improved functionality and diversified techniques, equipment, and materials. The following lists typical functions and surface properties that can be added by coating:
Addition of optical functions
- Reflection prevention
- Applications: LCDs, watch crystals, eyeglass lenses, camera lenses
- Anti-glare function
- Applications: Screen films for smartphones/tablets, LCDs
- Anti-newton (AN) ring function
- Applications: To prevent a "newton ring”, a ring of rainbow colors created by light interference in the small gap between two surfaces of overlaid transparent films, sheets, or glass panels.
- Light-blocking function
- Applications: Light-blocking materials for optical equipment such as the shutter, lens aperture, and finder mask of a camera, and internal coating of toner cartridges
- Photosensitivity
- This function makes an object change color or solubility upon receiving light. The types of reactions against light are as follows:
- • Photopolymerization: Solidification
- • Photocrosslinking: Bonding of multiple molecules
- • Photodecomposition: Breaking down and becoming soluble in developing solution
- • Photochromic darkening: Color production in only areas exposed to light
- • Photochromic fading: Preventing color production in only areas exposed to light
Addition of film physical property controls
- Hard coat
- Applications: For improving anti-scratch functions and surface durability of touch panels, LCDs, and buttons on consumer electronics
- Writability
- Applications: Adding the ability to write on the surface of stationery paper
- Hydrophilic and water retention
- Applications: Offset printing plates, inkjet printing films (Desensitization of hydrophobic substrate surfaces, coating with water-soluble material)
- Drainage and water-repellency
- Applications: Cellophane tape backing, adhesive film separators (Coating with organic solvent soluble resin)
- Liquid absorbency (water, oil)
- Applications: Porous absorption-type inkjet media
- Printability
- Applications: Printing paper, printing film (Surface processing for a compination of printing methods [screen, offset, gravure] and inks [UV-curing, water-soluble, soy oil-based])
- Weather resistance
- Applications: Suppressing ultraviolet degradation or hydrolytic degradation (Adding UV absorption or water-repellency)
Topic: Controlling coating conditions
Forming a continuous, uniform film coat is important for coating on film and sheet substrates. Thin-film forming in particular requires high-accuracy control and management of the film thickness.
The control method varies depending on the coating equipment. For example, a lip coater controls the coating amount at the head, and some machines coat excessive amounts and then control the thickness using a blade.
Unfortunately, variations in coating film thickness and other coating defects may not necessarily occur only in or around the coating amount control mechanism. Wrinkles and high edges may occur in the web (substrate) transfer process. Gaps between the rolls and rotation run-out accuracy may also lead to coating defects.
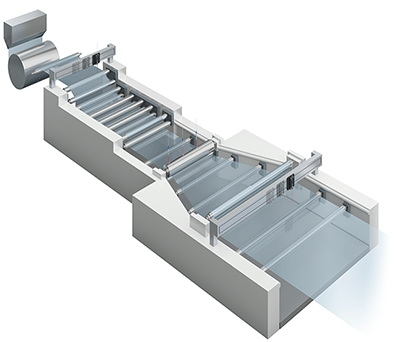
The introduction of high-accuracy displacement sensors enables comprehensive control of coating quality. Install the sensors at appropriate points in the coating process to measure the thickness in MD (Machine Direction) or TD (Transverse Direction), the state of the substrate, edge coating, and the rotation of and gaps between the rolls.
Introduction example: Coating Inspection of Films and Sheets