Bead Inspection in Automotive
Applying sealant (sealer, primer) such as liquid gaskets (CIPG, FIPG, etc.) or urethane foam is an indispensable step in the process of assembling engine parts and ECU cases, sealing chassis parts, and assembling glass panes onto car bodies.
Currently, dispenser robots are commonly used to apply sealant in a bead shape with a high aspect ratio along the shape of the target automatically. Achieving highly airtight seals, however, requires continuous and stable sealant coating. This section introduces inspection solutions for ensuring high-quality automatic coating.
Bead shape inspection
High-performance laser displacement sensors can be used to track the movement of a dispenser robot to achieve stable inspection of bead shape immediately after coating.
2D cross-sectional shape inspection of sealant (sealer, primer) during glass pane assembly
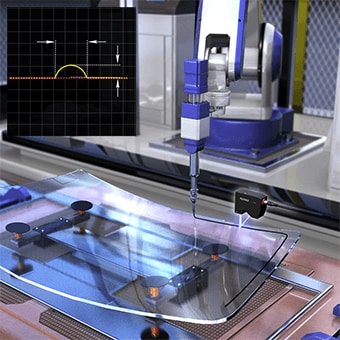
The process of assembling solar control glass panes onto car bodies requires preventing the release of products with defective sealant (sealer, primer) coating that may cause internal rust or stiffness degradation due to the ingress of water.
Adopting the LJ-X8000 Series into the process of automatic coating of urethane foam onto the glass panes with a dispenser robot enables inspection of the entire circumference immediately after coating by tracking the robot. Ultra-high-speed sampling in fine pitches is used to inspect the cross-sectional shape immediately after coating to monitor for defects.
The system ensures stable measurement even on targets with vastly different height and reflectivity, such as curved glass panes and sealant for which stable measurement is difficult when using conventional cameras.
3D shape inspection of sealant (sealer, primer) on engine parts
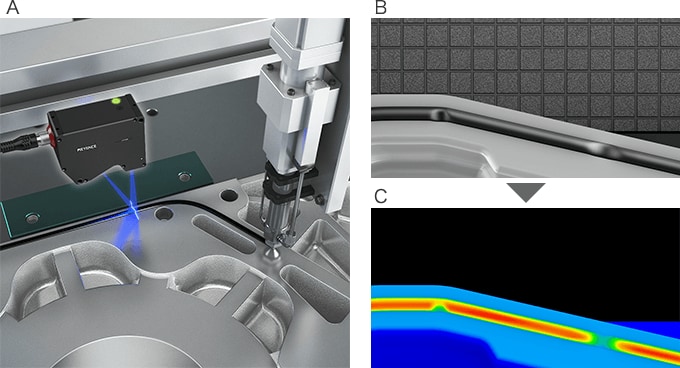
- A. Example measurement setup
- B. Enlarged view of measured section
- C. 3D image processing (Example of unacceptable product: An insufficient or interrupted bead is detected.)
For automotive components, the prevention of ingress and leakage of oil and water is required. To achieve this, it is important to ensure airtight joining and sealing through stable coating of sealant (sealer, primer) or liquid gaskets.
The High-speed 2D/3D Laser Scanner LJ-X8000 Series allows real-time measurement of the cross-sectional shape of a continuous sealant bead immediately after coating by tracking the fast movements of the dispenser robot. This system ensures stable inspection for defects such as height variations, insufficient coatings, or unevenness of the sealant without being affected by the color, shape, or material of the target or sealant, or by reflections from metal parts.
Moreover, using an image processing system to process the cross-sectional shape profile obtained with the LJ-X8000 Series enables 3D shape inspection for more precise shape, height, width, volume, and other aspects.