Data Acquisition (DAQ)
Applications and Examples of Temperature Measurement
Various types of measurement are performed at development and production sites, and “temperature measurement” is probably the most common among them. This section introduces examples of temperature measurement using data loggers and temperature sensors (such as thermocouples, resistance thermometers, and infrared temperature sensors). These examples are grouped into R&D and production site applications, which are further classified according to scenarios commonly seen in industries such as electronic devices, electric equipment, metal/steel, and plastic industries. We hope you will find this information useful.
R&D Applications
Electronic Device Industry Temperature Measurement During Life Testing of Electronic Components
To evaluate the service life of components, temperature distribution data is collected by repeatedly applying a high- or low-temperature heat stress to electronic devices. Various effects of temperature are verified through, for example, repeated testing under harsh environments (such as electric conduction with exposure to high temperatures); inspection of deformation, cracking, etc. due to heat; and confirmation of the durability of molded products that combine different materials such as plastic and metal. In addition to temperature measurement, the Multi-Input Data Collection System NR Series enables you to simultaneously perform different types of measurement by connecting units such as a strain measurement unit and a high-speed, high-voltage measurement unit, thereby reducing the time required for measurement.
Electrical Equipment Industry Room Temperature Distribution with Air Conditioners
In performance evaluation during the development of air conditioners, it is necessary to check the room temperature distribution. Using the Multi-Input Data Collection System NR Series, you can obtain detailed temperature distribution data thanks to this unit’s function that collects data from up to 576 channels. Multi-channel measurement (up to 576 points) can be performed simply by connecting the NR Series to your PC via a commercially available hub (a 100Base TX compatible switching hub), thereby minimizing the time and effort required during setup.
Electrical Equipment Industry Motor Surface Temperature
The surface temperature of a motor is measured to detect internal abnormalities based on temperature changes. The Multi-Input Data Collection System NR Series allows for simultaneous temperature measurement at multiple locations, so you can record the temperature of not only the motor body but also the surroundings. The ability to simultaneously measure values such as voltage, current, and rotation speed enables comprehensive inspection based on motor load conditions.
Get detailed information on our products by downloading our catalog.
View Catalog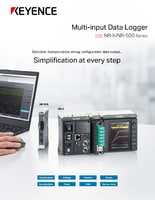
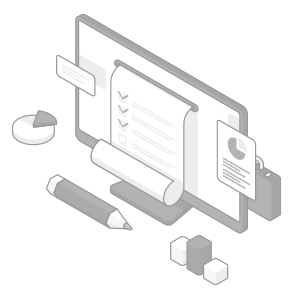
Production Site Applications
Metal and Steel Industry Temperature Distribution of Dies for Die-Cast Machines
Monitoring the temperature distribution of a die-cast machine during casting enables you to understand the casting conditions. The Multi-Input Data Collection System NR Series has a function that obtains and saves multi-channel data from up to 576 points. This function enables you to check the temperature distribution of the entire cast with better accuracy. The NR Series enables you to obtain information from a die-cast machine, such as its extrusion pressure and timing, from signals output by pressure sensors and other equipment. As such, the NR Series is also effective in performing comprehensive judgment that includes information other than the temperature.
Metal and Steel Industry Collection of Sintering Temperature Data
For sintered metal produced by sintering metal powder at about its melting point, variations in the accuracy and strength occur due to the sintering temperature. This means that you need to log the heating temperature. The Multi-Input Data Collection System NR Series has a function that accurately logs the temperature at multiple locations and thereby enables you to evaluate the temperature distribution correctly.
Plastic Industry Collection of Molding Machine Temperature Data
Injection molding of plastic requires that the temperature of each part, such as the injection molding cylinder and mold, be measured. You can use the Multi-Input Data Collection System NR Series to measure the temperature change in multiple parts, including the injection unit heater and the mold. In addition to the temperature, you can simultaneously record, for example, the pressure on the mold clamping unit side and the voltage and current of the motor. Being able to simultaneously record these values helps you set the pressure, voltage, and current properly. Setting values properly will result in higher accuracy as well as in injection molding machine operation that consumes less energy.
We’re here to provide you with more details.
Reach out today!
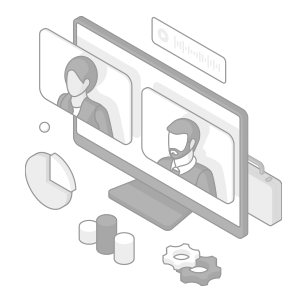
Temperature Data Collection with a Multi-Input Data Logger and a High-Precision Measurement Unit
The Multi-Input Data Logger “NR Series,” which is packed with various evaluation and analysis functions on the smallest and lightest body in its class, supports a wide variety of temperature measurements. You can accurately perform many types of temperature measurements by combining this product with the high-precision temperature/voltage measurement unit “NR-TH08,” in which each input channel is insulated with high-voltage semiconductor relays to ensure noise resistance.
Because the NR Series supports measurement using up to 576 channels, it is also effective in measuring the temperature distribution. The addition of a measurement unit enables a single unit to collect multiple types of data—including analog measurement, distortion, and acceleration. Also, this product’s compact design enhances its portability, and its dedicated software allows for easy setup and analysis. In this way, you can utilize this general-purpose, multi-input data logger for various types of analyses in a wide variety of situations.
Get detailed information on our products by downloading our catalog.
View Catalog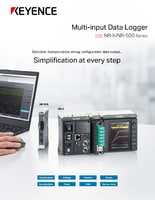
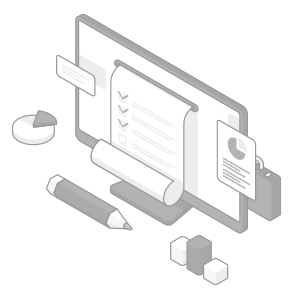
What are Temperature Measurement Systems?
Temperature measurement systems are, for lack of a better term, device setups consisting of measuring units and input transducers that are dedicated to measuring temperature. These devices usually use sensors to detect the object’s temperature, which is then converted into a digital signal by the measuring unit and relayed to the main computing unit for processing and data storage.
These systems are incredibly important across a variety of different industrial, commercial, and residential applications. However, we’ll focus primarily on the industrial aspect of temperature measurement, as they’re used to monitor and record temperature data but also trigger specific pre-set processes during the production and other manufacturing processes.
Temperature measurement systems come in a variety of shapes and sizes depending on the application. Large-scale manufacturing facilities would most likely benefit from large, stationary temperature measurement systems that are capable of receiving, processing, and storing data from tens, if not hundreds, of input transducers.
Other applications might benefit more from smaller, more compact, and portable temperature measuring tools with a more limited processing power and number of channels/inputs. As such, the choice of an adequate temperature measurement system mostly comes down to the application.
Discover more about this product.
Click here to book your demo.
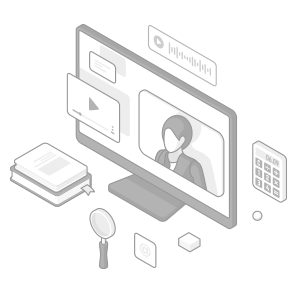
What are Temperature Sensors?
How do temperature sensors work, and what are they? Temperature sensors are input transducers, which means they measure a certain physical property, in this case, the temperature of an object, and convert the measurement into an electrical signal. Temperature is an analog physical property that represents a continuous range of values instead of discrete steps or levels.
Because of that, many sensor types output an analog signal, such as voltage, current, or resistance.
There are several different types of sensors, but the main categorization divides temperature sensors into two classes: contact and non-contact sensors—both are pretty self-explanatory. The classification is further divided into the following types:
- Resistance temperature detectors: Resistance temperature detectors change their resistance with temperature. They’re mostly made of platinum, as the metal offers a linear response to temperature fluctuations, thus eliminating the need for complex readouts. They’re typically suitable for temperature ranges from 200° to 600°C.
- Thermistors: Thermistors are resistors whose resistance changes with the temperature; however, their response is exponential rather than linear. This makes them less accurate over larger temperature ranges but incredibly accurate within limited temperature ranges that require a rapid and accurate temperature response. However, the exponential response requires using calculation methods to derive the readout.
- Infrared sensors: Infrared sensors are non-contact temperature sensors that capture the heat of a particular object by measuring the infrared radiation the object emits due to high temperature. This readout is then converted into either an analog or digital electrical signal and relayed to the measuring unit, which converts the signal and sends it to the computing unit for storage and further analysis.
Discover more about this product.
Click here to book your demo.
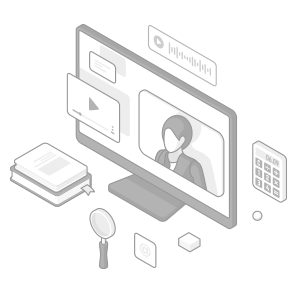
What are Temperature-Measuring Devices?
Temperature-measuring devices are an important component of temperature-measuring systems, as they’re directly responsible for receiving the sensor signal, converting it into an adequate form, and relaying it to the system’s central computing unit for storage and further analysis and interpretation. In simpler terms, they are the interface between the input transducers and the computing unit.
Are you in need of accurate temperature measurement solutions for your business? Look no further than KEYENCE. Contact us today to learn more about how we can help you improve your processes and increase productivity.
We’re here to provide you with more details.
Reach out today!
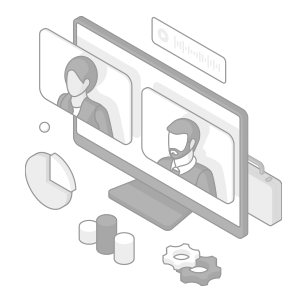