Predictive Maintenance
Networking eliminates the need for regular inspection and reactive inspection.
Not only can you back-up the setting values and measured values of individual sensors, you can set thresholds for predictive maintenance to receive prior notice and can analyze errors. Sending data to a host computer through network communication allows various predictive maintenance measures.
Inspect after a problem occurred
In conventional systems, sensors could only output ON/OFF signals. You were only able to take measures after a problem occurred.
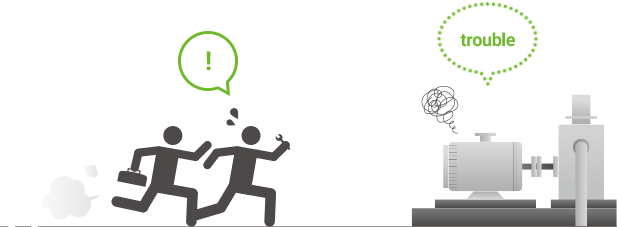
Notice before a problem occurs
When sensors are connected to a network, their measured values can be checked in real time. You can notice abnormalities before a problem occurs.
If you can predict failures or problems before they actually occur, you can take measures such as partial inspection of the relevant section before the manufacturing line is affected. This eliminates the need for recovery work completely, allowing efficient factory operation without production delay.
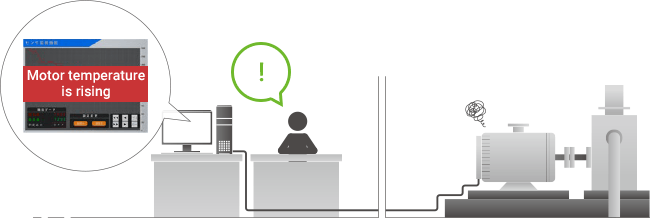
Advantages of IoT/NetworkingPredictive Maintenance
- The current values and OK/NG states of multiple sensors installed in the facility can be monitored in real time.
- Since abnormalities in sensors can be found before problems occurs, countermeasure can be taken before production is affected.
- There is no more need for continuous monitoring and regular inspection of the facility.
- This system should be improved in the future, so that when a sensor detects an abnormality, the main computer processes the data and takes countermeasures automatically. This will lead to significant reduction in the labor of the workers on the site.