Introduction - IoT and Sensors
Simply put, Iot is an abbreviation for the Internet of things. For a clearer understanding, try to imagine an environment where things embedded with communication functions are connected via the Internet.
These "things" can include industrial equipment, automobiles, and home appliances. This page gives insight into how IoT can be used within factory automation.
Connecting factories through IoT
There are advantages to connecting your factory equipment to a network. Here are some of them
- Maintain control by monitring and collecting data from the equipment.
- Add Value by analyzing stored data.
Utlizing the Iot in factories begins with connecting your sensors and equipment to a network then collecting that data. IoT can significantly improve productivity in the manufacturing industry by streamlining factory operations in conjunction with an ERP system; or by optimizing physical distribution through links with other factories.
Enterprise Resource Planning including finance and accounting
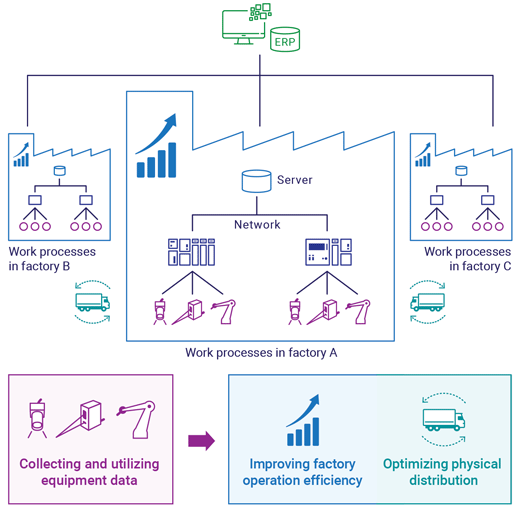
Industry 4.0, an innovation in the manufacturing industry
The most recognized attempt among them is Industry 4.0, which originated in Germany.
What is Industry 4.0?
Industry 4.0 is also referred to as the fourth industrial revolution. It aims to improve productivity in the entire manufacturing industry by networking all of the equipment in every factory and then, networking those factories together.
< History of industrial revolutions >
Factory mechanization through water power and steam engines which started at the end of the 18th century is called the first industrial revolution. Mass production using electricity in the early 20th century is called the second industrial revolution. Digitization using electronics and IT technologies in the late 20th century is called the third industrial revolution.
Industry 4.0 is a national project of the German government which is positioned as the "next-generation industrial revolution." It has been promoted since the mid 2000s through industry-government-academia cooperation and is defined in expectation of being the fourth industrial revolution.
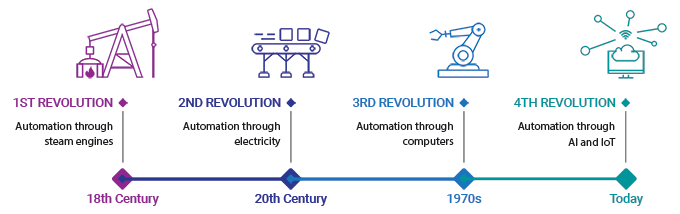
Technologies for materializing Industry 4.0
Industry 4.0 will require two broad types of innovative technologies.
The first type, is infrastructure technologies concerning the communication, storage and processing of the enormous volume of data that results from connecting everything. One example of such technologies is fog computing.
Conventionally, cloud computing has been used for data communication and processing. The materialization of Industry 4.0 requires the ability to process far more data. When cloud computing is used for processing all of these data, the network traffic may expand to an extraordinary size and go beyond conventional control.
As a countermeasure, a distributed processing environment called fog is implemented between the cloud and devices to process this enormous volume of data in advance and prevent overconcentration in the cloud. This approach of using distributed processing to prevent load concentration of network traffic is the concept of fog computing.
Another countermeasure is AI (artificial intelligence) technologies. Even when we have built the necessary infrastructure and collected enormous volumes of data, it serves no purpose unless we can utilize it. This is where AI technologies enter the picture. AI is expected to perform a wide variety of tasks, from helping humans by making plans or decisions to ultimately providing optimum predictions or decisions that are difficult for humans.
Advantages for manufacturing lines
The materialization of Industry 4.0 will provide reduced production costs and significantly shorter lead times.
This is because materialization promotes the introduction of digital data, automation, and virtual operation to production processes, which enables higher integration of the engineering chain and supply chain.
For example, precise AI-based simulations of demand planning or introduction planning allows development or design staff to shorten or skip some processes.
Moreover, timely synchronization of BOMs (bills of materials) between the design office and production site will prevent reversing manufacturing processes or producing defective targets. If data can be synchronized between manufacturers and material vendors, materials can be supplied automatically with the best timing.
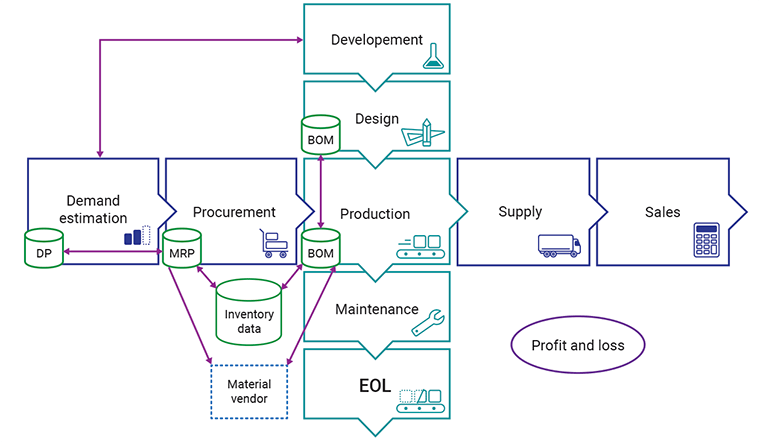
Data synchronization/exchange
Engineering chain: the process from product development and design to the discontinuation of production
Supply chain: the process from demand estimation and material procurement of a product to delivery to consumers
Smart factories as the goal of Industry 4.0
A smart factory is a factory in which Industry 4.0 has been realized. It is a manufacturing site where all of the equipment, robots and sensors in the factory are connected to a network to visualize various kinds of information and clarify the causal relationships among that information.
The realization of a smart factory leads to productivity improvements and cost reductions. Information is collected in real time and the facility and robots operate through programming. Work efficiency improves and problems caused by human error can be eliminated.
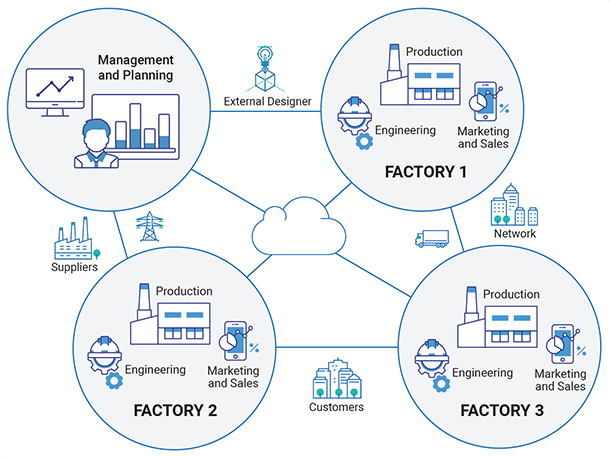
Introduction of sensors to make an innovation possible
Sensors are essential for the promotion of smart factories. It is sensors that enable the acquisition and collection of various data and the retrieval or tracking of manufacturing conditions or lot information of products.
When AI technologies are combined with sensors, the AI will make decisions autonomously and cooperate with machines and robots to optimize production.
This is a different level of operation from simple automation, and is also very different from the manufacturing lines based on digital data of the third industrial revolution.
KEYENCE's solutions to problems with sensors
Industry 4.0 lets equipment on different levels exchange data with each other.
The information system in a factory can be expressed as a structure of layers as follows:
- ERP (Enterprise Resource Planning) system for managing operating resources such as finance and accounting
- MES (Manufacturing Execution System) for operating and controlling production lines
- Industrial control system for computer-based system monitoring and process control
- Controller/PLC (Programmable Logic Controller)
- Industrial robots, sensors, and actuators on the site
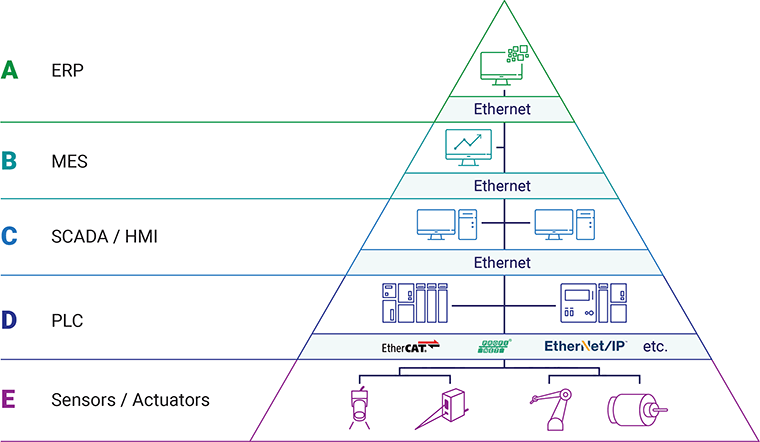
When sensors or other terminal devices are connected to a network, problems occur frequently due to the use of many different standards. Since the introduction of IoT is in a transition period, companies establish networks using different communication standards, which often makes connections between networks difficult. This also prevents the connection of sensors and other devices that are not compatible with the relevant standard.
In the current transitional condition where every item in a factory is being networked through Industry 4.0, KEYENCE will support customers on manufacturing site by developing product lines that are compatible with different networks and can adapt to changes.