Optical Comparator (Profile Projector)
What is Stamping? Types & Processes
For thousands of years, people have been shaping and molding metal for different purposes. As this process has evolved, it has provided more versatility to industries like automotive, aerospace, and electronics.
In the following, we’ll examine stamping, its origins, and how it plays a crucial role in manufacturing. Additionally, we’ll discuss stamping parts and precision metal stamping techniques and offer insights into the stamping manufacturing process, including its application in car manufacturing.
What Is Stamping? From the Beginning
Dating back to the seventh century B.C., stamping is an iconic metal processing method that creates sturdy shapes with precision and accuracy. Stamping parts began with Lydians, modern-day Turks, using handmade dies and heavy hammers to carve gold and silver coins. Over time, the stamping manufacturing process evolved into the industrial world of manufacturing in 1890 Germany.
Stamping parts is no longer a manual process used for small coins. Metal stamping parts grew from simple friction between a die, hammer, and coin to spanning four subcategories of processing. Manual stamping is a process of the past, with stamping methods now conducted by machines using tons of friction onto metal sheets. Even more, the stamping manufacturing process has grown to manufacture a range of component sizes for massive car companies like Honda and Toyota.
We’re here to provide you with more details.
Reach out today!
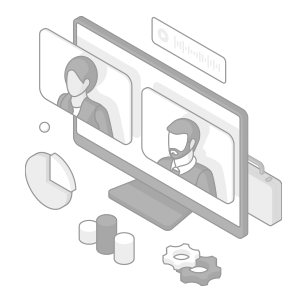
What is Metal Stamping?
Metal stamping is the manufacturing process of shaping a metal sheet using applied pressure with a die and tool. Stamping parts may change the sheet into an entirely new shape or puncture holes for the addition of more components. Because stamping is a general term, there are categories of stamping for identifying specific processes. These processes are piercing, punching, plastic forming, and blanking.
Since stamping is an all-encompassing term, the stamping process is typically achieved with an automated machine that can maneuver more than one stamping process at once. Due to this, it’s common for one sheet metal to take on many processes. Stamped parts are used across all industries but are notably used in the automotive industry.
Contact us to learn more about how our advanced technology can help take your business to the next level.
Contact Us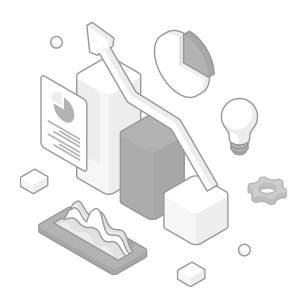
Why Use Stamping?
The use of stamping parts is popular because of its versatility and effectiveness in the manufacturing process. The incredible force used by metal stamping machines conquers thick metals while keeping the integrity of component results.
Additionally, stamping machines can reuse dies, tools, and extra sheet metals for large and efficiently processed manufacturing batches. Using a stamping machine allows for every piece of sheet metal to be used since these machines cycle through the entire sheet.
We’re here to provide you with more details.
Reach out today!
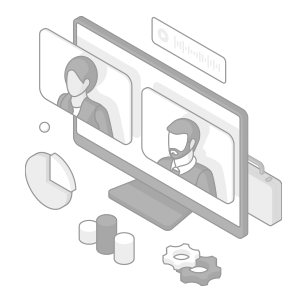
Categories of Stamping
Stamping includes several processes, such as piercing, punching, forming, and more. It’s also important to discern the difference between cold metal stamping and hot metal forming practices like forging. For example, cold stamping does well at room temperature settings, while forging is best for less malleable metals that require heat treatment. Stamping manufacturing is a unique process that has decades of relevance amidst changing technologies.
Below are some of the more common stamping processes.
Piercing
Piercing is a stamping parts process that produces holes in sheet metal for the final product. The final component uses the pierced hole as a means for connecting parts or components.
- Piercing Applications
-
- Fasteners
- Nozzles
Punching
Punching uses a similar process as piercing, but the result is where they differ. Punching is a form of stamping parts that uses the punched-out material for the final product.
- Punching Applications
-
- Washers
- Brackets
Plastic Forming
Plastic forming is a metal stamping parts process identified as a combination of machining processes like welding with stamping. Utilizing other machining processes for stamping—like wire drawing, deep drawing, bending, and riveting—strengthens the stamping parts process and results.
The reason why the word “plastic” is used for this category is because extra machining increases the metal’s plasticity. When conducting plastic forming, two subcategories make for an even more detailed process: hot-plastic forming and cold-plastic forming.
- Hot-Plastic Forming
- Hot-plastic forming involves integrating heat into the forming. Heating the metal allows for easier expansion and shape plasticity. The temperatures can rise above 900 degrees Celsius for hot stamping.
- Hot-Plastic Forming Applications
-
- Body pillars
- Roof rails
- Rockers
- Bumpers
- Door intrusion beams
- Cold-Plastic Forming
- Cold-plastic forming is the typical type of forming which does not use heat. Instead, it is simply stamping parts by forming a metal at room temperature.
Fine Blanking
Fine blanking is the process of using micron-order precision metal stamping to form complex shapes with smooth finishes. This type of stamping is unique in that pressure is pushed from the top and bottom of the material instead of just the top.
Discover more about this product.
Click here to book your demo.
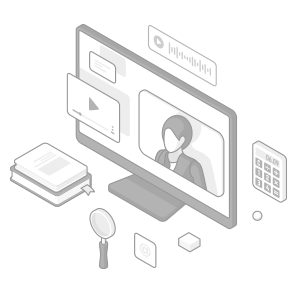
Step-by-Step Process of Stamping Manufacturing
Next, we will go through each step of the process to offer a better visual of the stamping operation. It is all pretty straightforward, but it still requires the right skill, equipment, and engineering precision to get the job done.
Design and Engineering
There are several designs commonly associated with the stamping manufacturing process. These include blanking, bending, and coining, each of which comes with its own nuances in the design operation.
Material Preparation
Preparation for metals going through stamping manufacturing can entail a handful of requirements. Aside from material selection, cutting, lubrication, and cleaning are all important focal points when choosing metal materials for stamping.
Feeding the Material
A seemingly simple step that requires a bit of tact, feeding the material is a crucial part of the equation. Other angles to consider for this step pertain to the following:
- Feeding length control
- Straightening (if applicable)
- Coil unwinding (if applicable)
- Die registration
It may seem like stamping manufacturing is pretty basic, but the process from start to finish includes several necessary steps.
Stamping Operations
Overall, stamping operations are widely used in the manufacturing industry due to their efficiency, versatility, and cost-effectiveness. They will remain a core part of metal transformation and are commonly used alongside other manufacturing techniques to create all kinds of products. Stamping parts is a common piece of the process, but it focuses on a broad variety of metal formations.
Contact us to learn more about how our advanced technology can help take your business to the next level.
Contact Us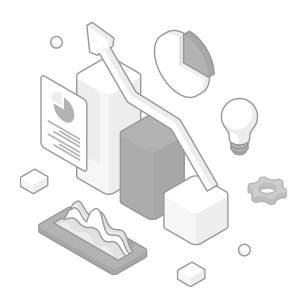
Challenges and Considerations in Stamping Parts
Operators have many different factors to consider throughout each stage of industrial stamping and manufacturing. To ensure consistent output and quality across the board, operators should focus on design complexity, material thickness, potential fractures, springback, and more.
Safety precautions should always be a part of auto parts stamping or any other form of the process. However, the future of stamping is bound to come with less risk due to technological advancements. Then again, it will also adapt alongside modern instruments like high-accuracy image dimension measurement systems.
Get detailed information on our products by downloading our catalog.
View Catalog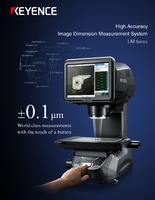
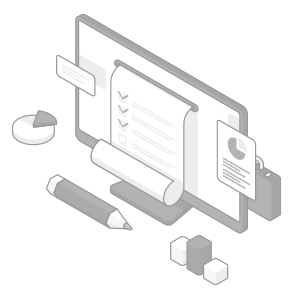
Importance of Stamping in Manufacturing Processes
Stamping is a versatile process that is not slowing down, especially within the automotive industry. The overall consensus puts the global metal stamping market at growing between $200-300 billion by 2028. From the evolution of carving coins to being a driving force in the automotive industry, stamping is a process that can’t be ignored.
Given the demand for metalwork across an endless number of industries, the process of stamping manufacturing continues to help make components and products with specific needs.
Stamping is also known to be a very efficient method of metal manufacturing, delivering results in a fraction of the time compared to many other processes. Moreover, stamping is often a cost-effective solution, making it a reliable option for metal manufacturers of all sizes. Lastly, using the stamping process allows manufacturers to handle large production orders more easily.
Looking for a Measurement Tool For Your Stamped Parts?
If you’re in the automotive industry, you’re all too familiar with the precision that comes with metal stamping. Especially with the responsibility of following strict regulations and making parts that easily form a whole part—measuring precisely is crucial. At KEYENCE, we created an automated optical comparator, also known as an Image Dimension Measurement System (IM), that is specialized for small, non-geometric parts that need precise measurements.
At the press of a button, the IM Series will autofocus, auto adjust, and measure up to 300 features simultaneously across 100 parts. Contact KEYENCE today for a free demo!
Contact us to learn more about how our advanced technology can help take your business to the next level.
Contact Us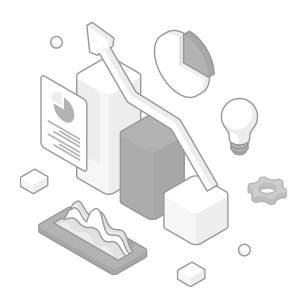
Related Downloads
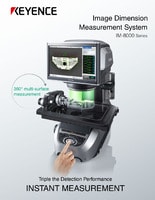
Brochure for the IM-8000 Series Image Dimension Measurement System. Accurately measure parts in seconds at the push of a button.