Eliminating the 3Ms (Muri (Overburden), Muda (Waste), and Mura (Unevenness))
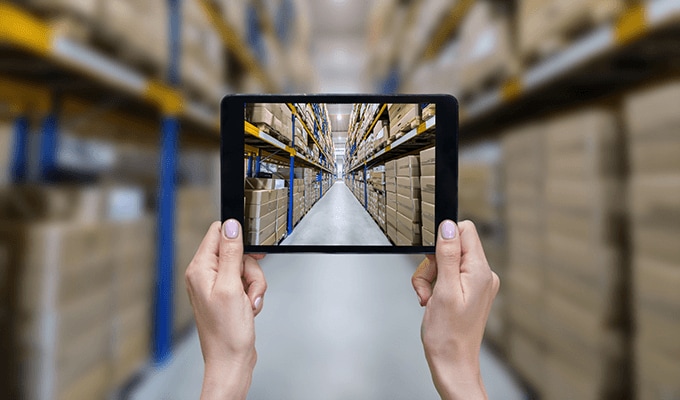
When improving the efficiency of production management and work flows, the elements that should be eliminated are the 3Ms (muri (overburden), muda (waste), and mura (unevenness)), and these same elements exist in logistics worksites. This section explains basic knowledge of the 3Ms, where the 3Ms are latent in logistics worksites, and how to eliminate the 3Ms.
- What are the 3Ms (Muri (Overburden), Muda (Waste), and Mura (Unevenness))?
- How to Eliminate the 3Ms (Muri (Overburden), Muda (Waste), and Mura (Unevenness))
- Countermeasures by Adopting Handheld Computers
What are the 3Ms (Muri (Overburden), Muda (Waste), and Mura (Unevenness))?
- Muri (Overburden)
- When a load is applied that exceeds capacity
- Muda (Waste)
- When the load is less than capacity
- Mura (Unevenness)
- When both muri (overburden) and muda (waste) exist and occur at different times
In an ideal work environment, the load (amount of work) and capacity are even. For example, if a target was set to finish a certain amount of work within a fixed time, muri (overburden) occurs if that cannot be achieved. On the other hand, muda (waste) occurs if the target is cleared with a large amount of spare time. Mura (Unevenness) occurs when both muri (overburden) and muda (waste) exist and the work is unstable.
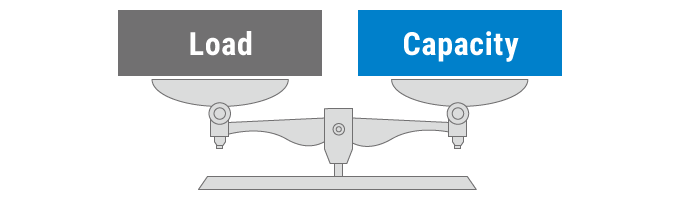
Reasons Why the 3Ms (Muri (Overburden), Muda (Waste), and Mura (Unevenness)) Occur
There is an ideal work environment where the load (amount of work) and capacity are even. However, the 3Ms occur when the balance between the load and capacity is upset. Reasons for this may be an inappropriate distribution of personnel or production plan. If the load increases, work becomes delayed. And if capacity increases, personnel become idle. Maintaining this balance is very important.
- When load exceeds capacity
-
- Work accumulates and backs up
- When a load is applied that exceeds the work capacity, the work backs up and the 3Ms (muri (overburden), muda (waste), and mura (unevenness)) occur.
- When capacity exceeds load
-
- Excess personnel and idleness
- When there is plenty of work capacity but the load is small, personnel become idle and the 3Ms (muri (overburden), muda (waste), and mura (unevenness)) occur.
3M Problems at Logistics Worksites
Insufficient Personnel | Excess Personnel |
---|---|
|
|
How to Eliminate the 3Ms (Muri (Overburden), Muda (Waste), and Mura (Unevenness))
The largest cause for the occurrence of muri (overburden), muda (waste), and mura (unevenness) at logistics worksites is the inappropriate distribution of personnel. It is bad if there are insufficient personnel and it is also bad if there is an excess of personnel. Busy processes and idle processes occurring at the same time or day is also a problem.
However, the amounts of receiving and shipping goods varies greatly depending on the day at logistics worksites, so it can be difficult to know how many personnel to distribute to each section. For this reason, the 3Ms (muri (overburden), muda (waste), and mura (unevenness)) occur easily because personnel cannot be distributed according to a clear production plan like in manufacturing.
To eliminate the 3Ms in logistics, the dependency on personnel needs to be reduced to a level greater than the optimal personnel distribution. One method for this is accurate management using handheld computers.
Countermeasures by Adopting Handheld Computers
At logistics worksites where there is less room for automation and mechanization unlike in manufacturing, it is not easy to reduce the dependency on personnel which is a cause of the 3Ms (muri (overburden), muda (waste), and mura (unevenness)). However, adopting handheld computers can be a relatively easy and efficient countermeasure.
At logistics worksites, visual inspection work is performed and invoices/delivery statements and actual goods are checked. The load of this work is great and careless mistakes, such as misjudgments and omissions, occur easily. Large reductions in labor requirements can be made and mistakes, such as shipping the wrong goods, can be prevented by adopting handheld computers for processes in which visual inspections were performed and automating the verification work in those processes. Personnel can be reduced while achieving a balance between capacity and load (amount of work).
Verification by handheld computer is accurate and fast to a degree that it cannot even be compared to visual inspection, so both experienced and inexperienced workers can perform the target amount of work without mistakes and eliminate mura (unevenness). This also simplifies the distribution of personnel.
- Balance load and capacity while reducing personnel requirements in logistics processes.
- Eliminate inefficiencies in inspections and checking invoices against actual goods. Prevent mistakes as well.
- Personnel distribution can be optimized because verification work can be done by even inexperienced workers.
Improvement Points in Inventory Management
The status of inventory can be verified when an order is made and the accuracy of inventory management can be greatly improved by using handheld computers. Various types of data can be managed if handheld computers are used, which also eliminates handwritten slips, so that input and writing work is no longer necessary and mistakes on slips can be prevented. Handheld computers are also effective in optimizing personnel distribution because work can be reduced and free resources can be assigned to other processes.
- Data That Can Be Managed by Handheld Computers
-
- Data to Input
- Representative code (who)
- Storage or retrieval
- Destination (where to)
- Product code (what)
- Quantity (how much)
- Obtainable Data
- Processing date/time
- Storage and retrieval data
- Extracting goods with insufficient quantity
- Applications for Data
- Inventory
- Location management
- Picking
Improvement Points in Shipping Inspections
Conventionally, shipping inspections were performed visually, but shipping mistakes would occur and lead to the risk of recovery work. However, visual inspections can be eliminated, the work required to perform those inspections reduced, and shipping mistakes can be prevented by managing goods using handheld computers and barcodes/2D codes. This also frees workers from stress, reduces work loads, and allows capacity to be maximized.
- Shipping Inspections Using Handheld Computers
-
- Data to Input
- Representative code (who)
- Storage or retrieval
- Destination (where to)
- Product code (what)
- Quantity (how much)
Inspection data is managed in the shipping history on the PC - Obtainable Data
- Check product quantity
- Verify shipping destination
- Check for insufficient package contents
- Main Applications for Data
- Inventory management
- Print shipping labels
- Receiving inspection