Vision Systems
- Vision System with Built-in AI VS series
- Intuitive Vision System CV-X series
- Customizable Vision System XG-X series
- GigE camera and lighting for PC-based machine vision VJ series
- Inline 3D Inspection 3D Vision series
- 3D Vision-Guided Robotics 3D VGR series
- Line Scan Technology Line Scan series
- 2D Vision-Guided Robotics 2D VGR series
- LED Lighting CA-D series
- Lenses (for Machine Vision) CA-L series
- Machine Vision System Database VisionDatabase series
- Automotive
- Automation Equipment/Machine Building
- Electric Vehicles
- Medical Device Manufacturing
- Food/Beverage Packaging
- Semiconductor/Manufacturing Electronics
- Vision-Guided Robotics
- Solar
- Logistics
- Commodities
- Paper Manufacturing
- Machine Tools
- Electronic Device
- Printing
- Mining/Metals
- Fabric/Textile
- Tobacco
- Marine
- Aerospace
Using Vision Systems to Solve EV Battery Inspection Challenges
The cost of EV batteries takes up a significant portion of an EV’s price tag, making manufacturers look for ways to cut costs without compromising quality or safety. In the efforts to manufacture cost-effective EV batteries, however, there are inspection challenges for each battery type that need proper attention.
EV battery inspection is required to ensure defects and other quality issues are detected to prevent EVs with unreliable battery systems from reaching the market. This resource covers common EV battery inspection challenges and how vision systems help address these issues.
Common EV Battery Inspection Challenges
Inspection systems are essential in identifying defects with battery packs and modules, measuring features, verifying assemblies, and identifying parts. During production some issues could arise due to different factors, including the battery cell type. Below are some inspection challenges posed by pouch, prismatic, and cylindrical EV battery cells.
Identifying Defects and Imperfections
Flexible and metallic, pouch EV batteries are susceptible to specular glare and wrinkles, making defect detection difficult.
Prismatic battery cells require a lot of welding. Separating acceptable weld anomalies from defective weld seams can be challenging for a vision system.
For cylindrical battery cells, manufacturers etch lot codes, material origin, and other important information directly on the battery to make recalls possible, isolate issues in production, and comply with regulatory requirements. Ensuring the accuracy and correctness of printed codes can be problematic due to the print orientation often used.
Codes can be printed anywhere on the sides of the battery. The shape of the batteries, being round or metallic, can cause deformed or distorted coding, making code reading and verifications challenging. Machine vision can help address these EV battery inspection challenges.
Vision systems for automotive manufacturing from KEYENCE can be used to address issues with specular glare and wrinkles in pouch-style battery inspections. We have solutions with AI detection capabilities in addition to rule-based detection programming.
Rule-based programming is limited to predefined rules, meaning defects outside of programmed variables and iterations of defects can go undetected. AI-powered detection technology, on the other hand, analyzes thousands of labeled images to learn what “good” and “bad” batteries look like and continuously uses data to improve system accuracy.
Equipped with powerful high-resolution cameras and an advanced illumination unit, our machine vision solution can detect flaws in prismatic battery weld seams and inconsistencies in cylindrical battery coding information.
Ensuring Safety and Reliability
Regardless of the EV battery type, cracks in the battery cells or modules, electrode misalignment, corrosion, terminal damage, and dimensional inaccuracies are common sets of challenges that can affect the safety and reliability of EV batteries.
Cracks can expose the internal components of an EV battery to surrounding spaces, increasing the risk of thermal runaway. This situation can lead to fire or explosion.
Improper placement of electrodes can lead to uneven current distribution. It can also increase the internal resistance of the battery, causing decreased power output and slower charging times.
In pouch cells, warped or bent cells can lead to battery performance and safety issues. During pouch cell production runs, accurate inspection is especially required as these battery types are more prone to dimensional inaccuracies due to their flexible design. Making sure even subtle defects are accurately detected depends on the capability of the vision system being used.
KEYENCE EV battery defect inspection solutions use powerful cameras to capture high-definition images and feed captured data to a powerful image processing unit that uses artificial intelligence to identify and classify defects.
Maintaining Production Speed and Efficiency
To stand out in a highly competitive market, manufacturers need to reduce cycle times and scale up production. One way to stay relevant is to get products into the market fast. Speed, however, must be achieved with production efficiency and regulation compliance in mind.
For example, there is no point in achieving 200 production parts per minute when there are structural issues like loose terminals, warped cells, and incorrect connections passing on to the next stage of production undetected. A high throughput without quality assurance is a quick way to upset any client base and become irrelevant in the market.
The right vision solution should be able to cover a greater field of view, perform simultaneous image capture, and do a quick analysis of capture data to keep up with the demands of today’s fast-moving battery production plants.
KEYENCE vision systems help manufacturers in speed and efficiency efforts without sacrificing quality. Our LumiTrax™️ technology, for instance, combines intelligent directional lighting with high-speed cameras and advanced image processing algorithms to deliver reliable rapid EV battery inspection results.
Compliance with Industry Standards
The rise in the demand for safer, more efficient, and reliable EV batteries means more stringent testing and compliance requirements.
First, manufactured batteries are tested for performance to ensure they meet charging efficiency, voltage stability, energy capacity, and cycle life requirements. Also, regulatory compliance demands that EV batteries tick production boxes for energy efficiency, safety, and energy emissions.
Interoperability testing is another standard covering the compatibility of coupled battery systems with charging stations. Moreover, environmental impact standards ask that production processes and EV batteries adhere to recycling guidelines and responsible handling of hazardous materials.
EV battery inspection assists in achieving compliance with these many standards by helping engineers check for defects that can affect product integrity at every production stage.
Curious about our pricing?
Click here to find out more.
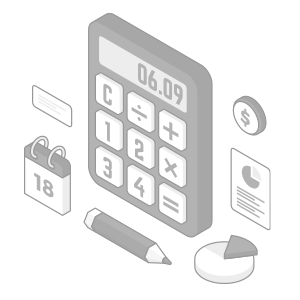
Benefits of Implementing Vision Systems for EV Battery Defect Inspection
The individual benefits of using vision systems for EV battery inspections are too numerous to count, but all boil down to three things: quality, compliance, and growth.
Using machine vision technology to achieve quality production means safe batteries for electric vehicles. Vision systems make it easy for EV battery plants to comply with all governmental and industrial regulations. And vision-assisted productions contribute immensely to a satisfied clientele that keeps patronage going.
As an industry leader, KEYENCE specializes in vision systems in the electric vehicles industry. Our vision systems can be used to address different types of EV battery inspection challenges.
For more information about our vision systems, contact us today.
Contact us to learn more about how our advanced technology can help take your business to the next level.
Contact Us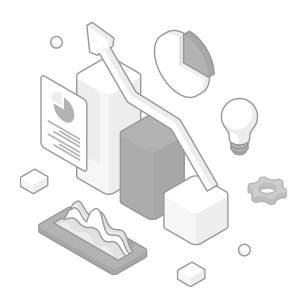
Related Products
Industries
- Automotive
- Automation Equipment/Machine Building
- Electric Vehicles
- Medical Device Manufacturing
- Food/Beverage Packaging
- Semiconductor/Manufacturing Electronics
- Vision-Guided Robotics
- Solar
- Logistics
- Commodities
- Paper Manufacturing
- Machine Tools
- Electronic Device
- Printing
- Mining/Metals
- Fabric/Textile
- Tobacco
- Marine
- Aerospace