Vision Systems
- Vision System with Built-in AI VS series
- Intuitive Vision System CV-X series
- Customizable Vision System XG-X series
- GigE camera and lighting for PC-based machine vision VJ series
- Inline 3D Inspection 3D Vision series
- 3D Vision-Guided Robotics 3D VGR series
- Line Scan Technology Line Scan series
- 2D Vision-Guided Robotics 2D VGR series
- LED Lighting CA-D series
- Lenses (for Machine Vision) CA-L series
- Machine Vision System Database VisionDatabase series
- Automotive
- Automation Equipment/Machine Building
- Electric Vehicles
- Medical Device Manufacturing
- Food/Beverage Packaging
- Semiconductor/Manufacturing Electronics
- Vision-Guided Robotics
- Solar
- Logistics
- Commodities
- Paper Manufacturing
- Machine Tools
- Electronic Device
- Printing
- Mining/Metals
- Fabric/Textile
- Tobacco
- Marine
- Aerospace
Impact of Machine Vision in Manufacturing
Artificial Intelligence (AI) and machine learning technologies have revolutionized many industries by enabling machines to perform tasks previously done by humans. Machine vision allows machines to “see” and understand their surroundings and trigger appropriate processes based on the visual input they receive.
With the rise of AI-powered systems, machine vision has immense potential to transform industrial manufacturing on any scale. These systems can perform a variety of different tasks, including object recognition, scene analysis, autonomous navigation, data collection, and many other tasks related to the manufacturing process.
In this guide, we’ll discuss the impact of machine vision in manufacturing, how these systems work, as well as their significance in the industrial manufacturing process.
How Does Machine Vision in Manufacturing Work?
Before we begin with how machine vision works, it’s important to note that machine vision application in manufacturing isn’t a novel concept. It’s been around for several decades; its origins can be traced back to the late 1950s and early 1960s, with significant developments occurring in 1980 as computer technology advanced.
The early instances of machine vision in manufacturing relied on simpler technology, such as photocells and photomultipliers, vidicon tubes, early computers and processing units, and basic image processing software to capture and process the input data.
The basic principle hasn’t changed in decades, but the technology has become more sophisticated. Nowadays, machine vision in the manufacturing industry relies on a variety of different input devices, such as 3D cameras, laser sensors, LIDARs, ultrasonic sensors, RADAR, and thermal imaging. The input technology used mostly depends on the application within the manufacturing process.
The transducers (all the different sensors) capture the data, which is then sent to the data processing unit, which interprets the captured data and stores it for later inspection and subsequent processing. There’s usually some software involved, which does all the substantial image processing and analysis.
In either case, machine vision systems always consist of transducers and processing/computing units. These can be further integrated into the manufacturing process. For example, if the observed part is defective, machine vision can trigger a process that would remove the particular part from the assembly line.
Additionally, these can also be effective in CNC machining environments, particularly when it comes to safety and setup verification, as well as precise measurement data capturing and processing.
Discover more about this product.
Click here to book your demo.
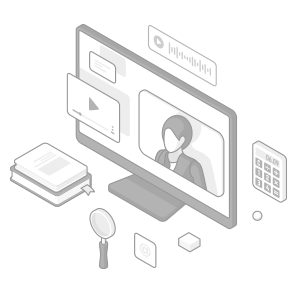
Significance of Machine Vision in Manufacturing
The industrial adoption of machine vision began in the 1980s, and it has only become more sophisticated. The advancements in digital cameras, processing power, and machine learning algorithms have allowed modern systems to handle complex tasks, such as 3D measurements, color inspection, and defect detection, at high speeds and with incredible precision.
Enhances Quality Control
Quality control is one of the most critical applications of AI technologies and machine vision in manufacturing. Traditional quality control processes often involve human inspectors, which implies human error, not to mention inconsistency and resource waste—humans are slower than machines.
Machine vision systems, on the other hand, are incredibly fast and efficient; they can perform quality control tasks with speed, precision, and reliability that can’t be matched by a human operator. Additionally, they’re so precise they can detect defects otherwise invisible to the naked eye, which gives them an obvious advantage over human-powered quality control.
These systems capture images or other data (depending on the transducer used) in real-time at great speed. These images or data are then analyzed by the system, which is capable of detecting defects or irregularities, even if they’re invisible to the human eye. Once the defect is identified, the system triggers a pre-programmed action.
This mostly includes stopping the production process for further inspection or just removing the product/part from further manufacturing and sending it to subsequent QC and corrections. The level of detail at which these systems operate is astonishing. For example, machine vision can even detect cold solder joints on electronic circuitry, which previously required a visual/manual inspection.
- Improves Safety and Compliance
-
Traditional inspection methods previously relied on human intervention and judgment. For example, each 50th or 100th product made in mold or stamp manufacturing would be inspected. This implied taking the product off the conveyor and performing a manual inspection. If the product is defective, the whole manufacturing process would halt for a bigger inspection sample.
However, machine vision systems ensure complete compliance with industry standards, increased product safety, and eliminate any safety concerns associated with humans near moving machinery. - Reduces Production Costs
-
Depending on the application and placement of machine vision in the manufacturing process, machine vision systems collect and optimize process control over time. The increased precision across all applications of machine vision systems significantly reduces resource waste, which also lowers production costs.
For example, sawmills use machine vision in manufacturing planks to optimize plan yield from a log, thus maintaining product quality and reducing unnecessary waste. The increased precision brought by machine vision in manufacturing has a long-term benefit in terms of reducing production costs and increasing profit margin.
Contact us to learn more about how our advanced technology can help take your business to the next level.
Contact Us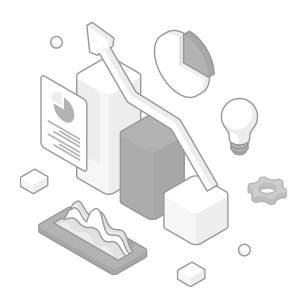
FAQs about Machine Vision Use Cases in Manufacturing
What are the Benefits of Machine Vision in Manufacturing?
The benefits of machine vision in manufacturing include enhanced quality control, better optimization of the manufacturing process, improved safety and compliance, more optimized resource management, and reduced manufacturing costs.
How Do Machine Vision Systems for Manufacturing Ensure Compliance and Traceability?
Machine vision systems for manufacturing ensure compliance through precision inspections, consistency and repeatability of measurements, and real-time feedback. These systems also log the captured data, which ensures better product tracking and allows for subsequent analysis. And most importantly, machine vision systems also automatically document inspections and outcomes.
Why is Industrial Automation Important in the Manufacturing Industry?
It’s important for all the aforementioned reasons, which include eliminating or at least minimizing human error, streamlining the process, ensuring better quality of the end product, and reducing production costs.
Is Machine Vision in Manufacturing Customizable by Process?
Machine vision in manufacturing is highly customizable and can be adapted to nearly any manufacturing process that might benefit from a “visual” inspection.
We’re here to provide you with more details.
Reach out today!
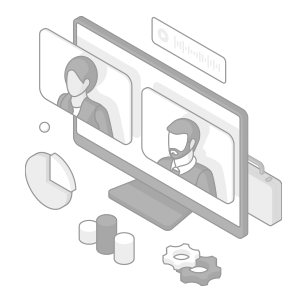
Related Downloads
Related Products
Industries
- Automotive
- Automation Equipment/Machine Building
- Electric Vehicles
- Medical Device Manufacturing
- Food/Beverage Packaging
- Semiconductor/Manufacturing Electronics
- Vision-Guided Robotics
- Solar
- Logistics
- Commodities
- Paper Manufacturing
- Machine Tools
- Electronic Device
- Printing
- Mining/Metals
- Fabric/Textile
- Tobacco
- Marine
- Aerospace