Laser Marking Systems / Laser Markers
Laser Marking for Traceability - An Essential Tool in the Medical Industry
-
Tags:
- Medical , Laser Etching , Laser Labeling
Traceability is the practice of marking a device with an identifying text, logo, or 1D/2D code for tracking the product back to its production site. This practice is common and critical across numerous sectors, including the medical industry.
Importance of Traceability in the Medical Industry
Since the medical sector uses devices on and in patients, product traceability in medical devices is essential for responding to defects, preventing counterfeiting, and ensuring health and safety. Using a laser marker for the medical sector is a foolproof way to create permanent, clean, and FDA compliant marks.
Benefits of Implementation
Managing medical equipment through direct marking offers the following advantages.
- Maintenance of quality by being able to monitor how frequently tools are used
- Optimisation of replacement and order timing
- Improvement in efficiency and standardisation of instrument sets
- Tracking of instruments during each process (location management)
- Prevention of excess stock
- Analysis of loss and theft, etc.
Responding to Defective Devices
Any product manufactured can have a defect that could range from minor to life-threatening. However, no matter how dire the defect is, defects should always be taken seriously by manufacturers and consumers of the product.
Consider how a defect could be particularly threatening to medical devices. For example, a defective hip replacement inserted into a patient's body could be detrimental to health and ability to function.
Medical device traceability solutions are essential for quick responses to defects. If a medical professional notices a defect in a device, traceability marks are a reference to figure out where the device came from and then quickly alert the manufacturing company. Alternatively, if a manufacturing company recalls a product, professionals can examine the marks on their devices to determine whether the product came from a defective production site.
Preventing Counterfeiting
Counterfeiting is the practice of imitating a product, usually using cheaper labor and cheaper materials. It is harmful because the materials used are less effective than the approved ones. The cheaper imitations are prone to break down quicker or produce inaccurate results.
Counterfeiting is especially dangerous to the medical industry because it increases the procedural risk to the consumer due to lower quality imitations of the medical tool. Traceability on approved devices is necessary to slow down the rise of counterfeiting because it provides a reference point for devices. With a traceability mark, professionals can confirm the validity of the device.
We’re here to provide you with more details.
Reach out today!
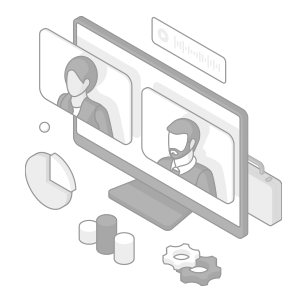
Benefits of Using Laser Marking for Medical Traceability
Clean and Permanent Marks
Using a laser marker for the medical sector ensures clean and permanent traceability marks. Laser markers use heat absorption and a focused beam to interact with product material. The result is a clean and permanent mark that outperforms printing and stamping methods. Printing and stamping use ink, which can wear over time and become smudged, distorted, or erased.
Laser markers' clean and permanent marks can withstand heat, friction, and frequent sterilization. The permanency of marks is essential to traceability practices to ensure each device has a code that is easily identified and traced correctly.
Fast and Consistent Marking
KEYENCE Laser markers provide automation capabilities superior to alternative marking methods. Process automation ensures fast and consistent marking while mitigating the risk for human error and expensive scrap in a production setting.
Particularly with KEYENCE’s laser markers, the laser markers use proprietary Marking Builder software and 3-Axis control to enhance the ease of use and eliminate barriers common to traditional laser systems. The software uses its programming and 3-Axis control to manipulate its focus to match the product. The 3-Axis control and software eliminate the need for manual adjustments to either the laser or part placement, providing an increase in throughput and decreased risk of operator error.
Mark Difficult-to-Reach Areas
Medical devices are often of odd shapes and sizes. For example, catheters, medical tube connectors, and needle hubs. Because of the odd shapes, these devices are difficult to mark without distorting the pattern.
KEYENCE’s Z-MAP Creator software combats this problem using 3D-CAD model data to create a foundation for three-dimensional marking. The software aligns a code, logo, or pattern onto a 3D shape; then, with a click of a button, the laser will mark based on the alignment. The laser’s ability to mark difficult-to-reach areas without distortion makes for reliable medical device traceability designs that ensure compliance and safety with all devices.
Discover more about this product.
Click here to book your demo.
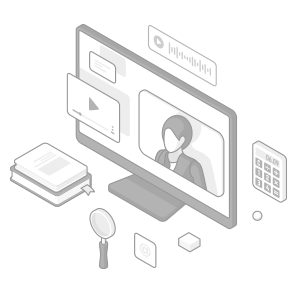
Applications of Laser Marking in the Medical Industry
Multi-Colored Resin Devices
Plastic is a common material used for medical devices because it’s easy to clean and durable. When working with plastics, a common tactic is using colors to improve the visual identification of devices. The visual identification of devices is a reliable method for preventing mistakes when administering medicines.
UV lasers are ideal for plastic medical device traceability. The high absorption rate of UV lasers mitigate the risk of causing damage to a medical device from marking. The improved rate of absorption permits photolytic processing as opposed to the traditional thermal processing accomplished by lasers at wavelengths other than UV.
Examples of resin devices include:
- Needle hubs
- Catheter connectors
- Medical tubes
- Syringes
- Medical instrument covers
- Medicine bottles
Metal Devices
Metal is a material frequently used for surgical devices because of its sterilization properties and durability. Since metal devices are regularly coming into contact with a patient’s body, medical professionals habitually sterilize them with soap, water, and other chemicals.
With this in mind, the permanency of a laser mark is essential to a metal device. If marked correctly, laser marks can be rust-resistant, avoid collecting foreign matter, and will not wear over time. Using a laser marker instead of a stamper or printer ensures that traceability markings withstand any outside forces.
Examples of metal devices include:
- Catheter wires
- Medical drills
- Medical bolts
Hybrid lasers are ideal for metal medical device traceability. The hybrid laser structure improves the absorption rate and beam control to permit contrast marking across a wider range of materials with improved cycle time compared to a traditional fiber laser marker.
Discover more about this product.
Click here to book your demo.
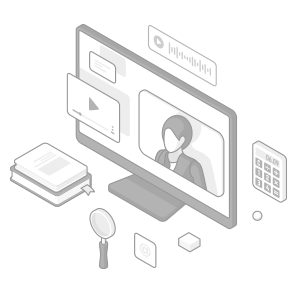
Ensuring Safety and Compliance Through Laser Marking
In 2013, the FDA passed a regulation requiring medical devices to have a unique device identification (UDI). UDIs ensure the identification of medical devices from manufacturing to distribution to patient use. The FDA requires UDIs to be readable by both machines and humans, which the FDA predicts will “improve patient safety, modernize postmarket surveillance, and facilitate medical device innovation.”
All manufacturers must follow FDA guidelines regarding UDIs. UDIs have two necessary identifiers: device identifier and production identifier. The device identifier is a mark, while the production identifier is a serial number, batch number, expiration date, and manufacturing date.
Laser marking for medical compliance achieves all of these marks with permanency, consistency, and precision. Choosing a laser marker for UDIs rather than an inkjet printer or stamp ensures compliance. Manufacturers can be confident that the UDI will not fade over time and will be easily read by both machines and humans.
We’re here to provide you with more details.
Reach out today!
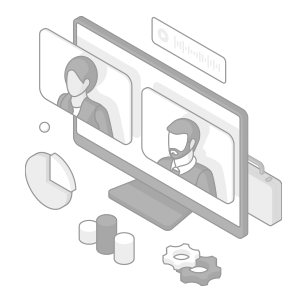
Related Downloads
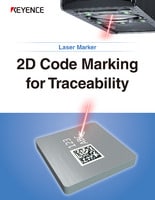
2D codes are used to store date codes, lot codes, serial numbers, and more. Users who are considering 2D code marking should read this laser marking guidebook.