Industrial Laser Marking Systems / Laser Markers
How to Etch a Curved, Cylindrical, or Multi-Plane Part With a Laser
-
Tags:
- Laser Marking , Laser Etching , Laser Engraving
Etching intricate designs on flat surfaces is challenging enough, but what happens when your project involves a curved, cylindrical, or multi-plane part? Historically, achieving consistent results when marking these surfaces has been a challenge. However, new advantages in technology for laser etching curved surfaces have addressed such challenges and created a number of operational benefits.
Laser engraving of round surfaces or etching other shapes requires less effort, training, and time. This can apply to many materials, including metal, glass, and plastics.
Ready to tackle these challenges and hear more about the latest laser etching equipment? Read on to learn techniques on how to etch curved surfaces, cylindrical components, and multi-plane parts.
Understanding Laser Etching on Curved Surfaces
Achieving desired markings on curved surfaces requires a good understanding of materials and shapes. Even with advanced laser etching software, laser etching curved surfaces can be costly for businesses and time-consuming for operators.
These complex shapes and surfaces demand adaptable machinery that adjusts laser power, speed, and focal point movement. While this may seem tough to achieve manually, many aspects of the technology can be automated for efficiency.
Thanks to programmable laser marking systems, laser etching applications are more diverse than ever, whether you're working with one or multiple material types on the production line. Considering the various techniques for laser etching curved surfaces will help you choose the laser marker that's right for your operation.
Curious about our pricing?
Click here to find out more.
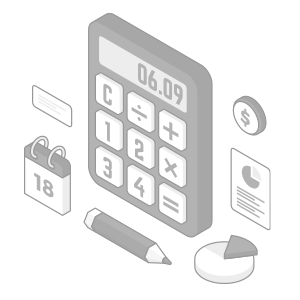
Techniques for Etching Curved, Cylindrical, or Multi-Plane Part Surfaces
The versatility of an etching laser is undeniable, but achieving great results relies on the right equipment and techniques. For example, marking cylindrical and curved surfaces requires features like 3-axis control and autofocus to simplify operations. These features allow operators to precisely mark parts over wide fields and varying focal depths, but are only available with certain laser markers. On the contrary, some laser etching machines require technicians to move the target manually, or tie in additional machinery like a rotary, to get to the correct positioning. This can lead to costly errors that are time-consuming and preventable.
Because of these and other advancements in technology, manufacturers are expanding their laser engraving applications. As equipment evolves, so do the techniques used.
Several examples of techniques used in laser etching curved surfaces include:
- Multi-axis laser systems to handle more complex surface area
- 3D modeling for pre-visualization to set parameters for laser path and automated features
- A Z-axis tool that's programmable for quick changes with the added benefit of maintaining efficiency
- Creating uniform markings with the help of variable lens clusters built within the laser head to deliver uniform markings on cylindrical parts
Many of the parameters of this technology work to automate and streamline your operation, but that doesn't mean a manual approach isn't possible. Those on the ground floor can intervene to make manual focus adjustments, change measurements, and even navigate the laser head by hand if needed.
Versatile tech is valuable to have on hand, but it is relevant to consider that a manual approach isn't the most time-sensitive technique. Many of the points made in this section apply to comparisons in laser etching vs laser engraving vs laser marking. While each specific process and its common applications have many unique components, there are plenty of cross-application and features involved.
Etching has a number of popular applications in manufacturing, both traditional and emerging. Some are intuitive, while others are new markets unlocked by modern laser marking technology.
We’re here to provide you with more details.
Reach out today!
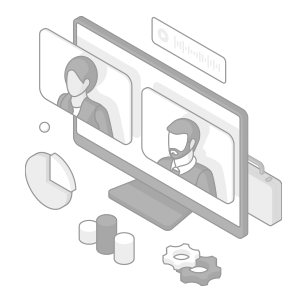
Applications of Laser Etching on Curved Cylindrical or Multi-Plane Parts
From a consumer standpoint, laser etching is merely a form of customization, but the process serves a much larger purpose. With an ever-growing list of industrial applications, laser etching curved surfaces is a global need, not just a creative way to personalize products.
Once you get a comprehensive view of the industry reach that laser etching has in manufacturing, you'll realize how easily it can be integrated into your own production line. Below are a few popular examples of industries that learned how to etch curved surfaces for a variety of applications:
- Etching measurement and calibration marks on surgical equipment
- Marking high-quality packaging for consumer goods
- Creating consistent etching for serial numbers and other part or batch details
- Improving end-to-end traceability on every component
- Enhancing consumer safety due to legible and durable markings
- Adding complex numbers and information to automotive parts
- Creating detailed etching on the many parts found in aircraft and aerospace
These applications and their surrounding processes will continue to evolve. Although covering a broad range of industries, this overview only scratches the surface of laser etching's potential. Laser etching technology has raised the bar for manufacturing, but we aren't looking at the ceiling here.
New innovations within this space are always on the horizon, stemming from industry experts and adopters like yourself. The quick-paced nature of manufacturing constantly fuels the need for new ideas, processes, and innovations. Between industrial necessity and personal business growth, learning how to etch curved surfaces can take your operation to the next level and discover a newfound competitive advantage.
Discover more about this product.
Click here to book your demo.
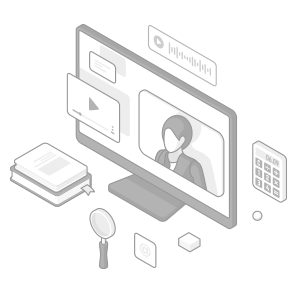
KEYENCE Laser Marking Solutions
Whether you are brand new to laser etching curved surfaces or simply looking to learn new techniques, you now have some helpful insights to consider. The great news is that almost every KEYENCE laser etching system has built in 3-axis control. This means that marking curved, cylindrical, and multi-planed surfaces is as easy as can be. Models like the MD-X Series also have built in distance sensors that can map out different geometries before marking to assure that everything is clean and in focus.
If you still have technical questions or need help finding the right laser marking equipment for your operations, contact us today. Our team has decades of experience and is happy to assist.
Get detailed information on our products by downloading our catalog.
View Catalog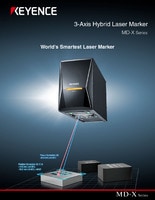
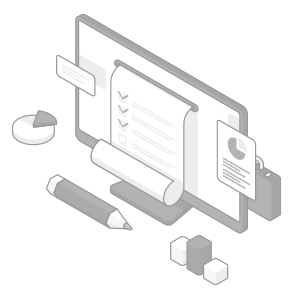
Related Downloads
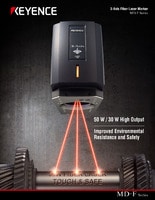
KEYENCE's MD-F Series offers unmatched functionality in a compact design.