Laser Marking Systems / Laser Markers
11 Top Direct Part Marking Methods
-
Tags:
- Laser Marking , Laser Etching , Laser Engraving
When it comes to industrial production, permanent part identification is a necessity. Traceability, safety, and quality control are a few reasons direct part marking methods are used in many industries. Whether you’re dealing with aerospace components or automotive parts, it is essential to distinguish between the available methods and equipment. To help clarify, the following examines the eleven top direct part marking methods that are being used today.
Understanding Permanent Part Marking Methods
Before we get into the specifics, it's important to understand what makes direct, permanent part marking methods unique. Unlike labels or stickers that can wear out or be removed, these methods permanently alter the surface of the part. This process creates durable marks that can withstand harsh environments, frequent use, or tough conditions.
Method 1: Laser Engraving
Laser engraving is a standout technique in the world of direct part marking methods. It uses a high-powered laser, like a 3-axis Fiber laser marker, to remove material from the surface, leaving a lasting, etched design. Exceptional precision and contrast are possible with laser engraving, making it ideal for parts that require clear markings. For marks like serial numbers to logos, this method is widely favored for its durability and detail.
Method 2: Laser Etching
Laser etching is often confused with engraving, but the two direct part marking methods have fundamental differences. While engraving digs deeper into the material, etching slightly alters the surface, creating a raised or indented texture. Faster and more cost-effective than engraving, etching still offers strong readability and permanence. Industries needing rapid production without sacrificing quality utilize laser etching as it balances speed and performance.
Method 3: Fiber Laser Marking
The next versatile method, fiber laser marking, excels with metal components, especially machined parts. A fiber optic cable is used to amplify the light, producing clear, high-contrast markings. Extreme conditions like heat, corrosion, and abrasion are no match for marks created with fiber lasers. Industries like oil and gas and automotive, where every mark needs to hold up against wear and tear over time, find its precision very useful. A 3-axis fiber laser marker can even process multiple products on a single line, eliminating tool changes.
Method 4: UV Laser Marking
If you’re dealing with materials like glass, ceramics, or plastics, UV laser marking is a reliable choice. Known for its "cold marking" process, it doesn’t generate heat, so it's safe for sensitive materials that might crack or deform under other marking methods. An excellent option for intricate designs, such as microchips or electronic circuits, UV laser marking is one of the most common permanent part marking methods. Systems like the 3-axis UV laser marker eliminate burrs and yellow tinting for a perfect finish.
Method 5: CO2 Marking
CO2 laser marking is another popular direct part marking method, particularly for non-metallic surfaces like wood, paper, and plastics. By vaporizing the surface of the material, marks from CO2 lasers leave behind a distinct, lasting mark. Common in packaging, manufacturers can easily print expiration dates or barcodes directly onto products without slowing down production. Because CO2 lasers do not require any consumables or have any running expenditure, this method is commonly used.
Method 6: Green Laser Marking
Green laser marking is perfect for marking materials that are challenging to handle, like reflective metals or glass. Operating at a shorter wavelength, the green laser's exceptional contrast and accuracy are beneficial. Solar and electronics industries, for example, prefer these features and methods for specific use cases. Telecentric green laser markers minimize thermal stress on the part, unlike many other methods. As a result, there’s no damage to the integrity of delicate materials.
Method 7: Dot Peen Marking
Dot peen marking, also known as pin marking, is a direct part marking method where a stylus strikes the surface of the part to create a series of dots that form text or patterns. Even in harsh environments, this method is favored for its simplicity and durability. Whether it’s a VIN number on a car chassis or a serial number on heavy machinery, dot peen marking offers a rugged solution that can endure extreme temperatures and exposure to chemicals.
Method 8: Electrochemical Marking
Electrochemical marking, or etch marking, is a process that creates high-contrast marks on conductive materials. Perfect for marking stainless steel or titanium without compromising their corrosion-resistant properties, it is gentle yet effective. You'll often find electrochemical markings on surgical instruments or aerospace components because of the precision and durability.
Method 9: Scribing Marking
Scribing, or scratching, is another form of mechanical marking. It uses a diamond or carbide-tipped stylus to draw characters or symbols directly onto the part’s surface. While it’s not as fast as other methods, scribing is highly reliable for permanent markings that need to be deep and easily readable. Also, it is often used in applications where the mark needs to withstand extreme environmental conditions.
Method 10: Stamp Marking
Stamp marking involves pressing a shaped die into the surface of a part, leaving a permanent, indented mark. Industries like automotive and heavy equipment choose this method for batch coding, serial numbers, or part identification. Stamp marking is straightforward but highly effective for large production runs, as it provides consistency and longevity in the mark.
Method 11: Inkjet Marking
Inkjet marking, while not as permanent as other methods, is still widely used for direct part marking. A continuous flow of ink droplets prints directly onto the surface of a part. While inkjet isn’t ideal for long-term durability, it offers flexibility and speed, especially for temporary markings or coding that may not need to last a long time. Industries that prioritize high-speed marking, like food and beverage packaging, will use this method at times.
We’re here to provide you with more details.
Reach out today!
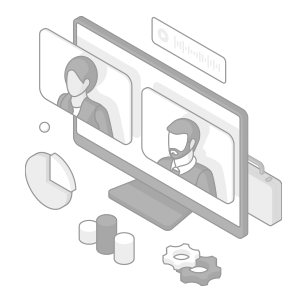
How to Choose the Right Part Marking Method
With so many direct part marking methods to choose from, how do you decide which is suitable for your project? First, consider the material you’re working with—whether it’s metal, plastic, glass, or something else entirely. Think about the durability and if you require permanent part marking methods (i.e., do the marks need to survive high temperatures, corrosion, or constant wear). Finally, take production speed and cost into account. Although some laser marking systems and methods have higher upfront costs, they can save money in the long run by reducing wear and tear on your equipment.
Discover more about this product.
Click here to book your demo.
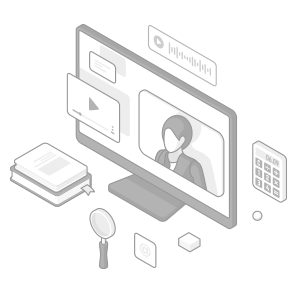
Future Trends in Part Marking Technology
Part marking methods are moving quickly. Automation and artificial intelligence are changing how operations are performed. Machine learning algorithms, for example, can now assess and adjust marking processes in real time. Analyzing material type, surface condition, and marking speed is becoming easier for operators. Fewer errors, faster production cycles, and more consistent quality are possible, and it can reduce costs as less human intervention is needed.
A growing demand for sustainability is also pushing manufacturers to adopt eco-friendly methods (such as UV laser marking, which minimizes waste and energy consumption). Direct part marking methods will become even more integrated into the broader manufacturing ecosystem as these trends take shape.
Ready to narrow down the best part marking methods for your particular application? Contact us today to talk to a specialist or receive a free demo.
We’re here to provide you with more details.
Reach out today!
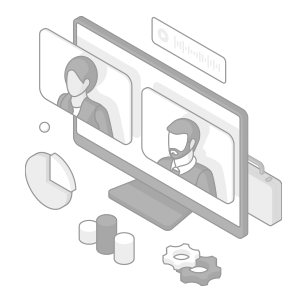
Related Downloads
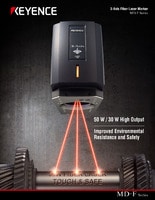
KEYENCE's MD-F Series offers unmatched functionality in a compact design.