Data Acquisition (DAQ)
How to Choose the Best Data Acquisition System (DAQ)
-
Tags:
- Data Acquisition
This guide provides a structured approach to selecting the best DAQ system based on key technical factors and helps users and buyers avoid common mistakes.
Why Choosing the Right DAQ Matters
Selecting the best data acquisition system is important as different applications (e.g. manufacturing, research, or quality control) demand varying levels of sampling speed, resolution, and processing capabilities. High-speed vibration analysis, for example, differs from long-term environmental monitoring, making proper system selection essential.
We’re here to provide you with more details.
Reach out today!
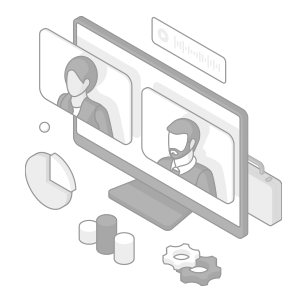
Common DAQ Selection Mistakes
Many buyers fixate on sampling rates or bit resolution but overlook sensor compatibility, data processing, and power needs. Underestimating the required sampling rate can cause aliasing errors, while low-resolution systems may fail in high-precision applications. Neglecting filtering, noise reduction, and scalability can also lead to performance issues over time.
How This Guide Helps
This guide provides a structured approach to selecting the best DAQ system based on key technical factors and helps users and buyers avoid common mistakes.
Discover more about this product.
Click here to book your demo.
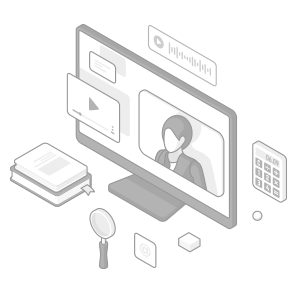
Key Technical Considerations for DAQ Hardware Selection
Sensor & Signal Compatibility
Types of Sensors Used in DAQ Systems
The best DAQ systems collect data from various sensors, including:
- Temperature Sensors - thermocouples, RTDs, thermistors
- Voltage and Current Sensors - for electrical and power monitoring
- Strain Gauges and Force Sensors - for material stress testing
- Displacement and Position Sensors - for motion tracking
- RPM and Rotational Sensors - for industrial machinery
- Digital Inputs - for monitoring on/off signals, logic states, and event triggers
Matching DAQ to Sensor Requirements
For accurate measurements, a DAQ system must be compatible with the signal output of the sensors. Some sensors output analog signals that require amplification and conditioning. Others output digital data which requires a system with appropriate communication protocols (I2C, SPI, Ethernet, USB).
Sampling Rate & Data Precision
How Fast Should Your DAQ Sample Data?
The sampling rate determines how frequently data points are recorded and is application-dependent:
- Low-Speed Applications (1-100 Hz): Temperature, humidity, and slow-changing industrial processes
- Mid-Range Applications (1 kHz-100 kHz): Structural testing, pressure monitoring, and machine diagnostics
- High-Speed Applications (100 kHz+): Vibration analysis, acoustic testing, transient signal capture, and shock monitoring
Why Oversampling Matters
Oversampling enhances accuracy and reduces artifacts. A signal must be sampled at over twice its highest frequency (Nyquist rate) to prevent distortion, but 10x ensures better noise filtering and resolution.
Bit Resolution & Measurement Accuracy
How Bit Resolution Affects Data Quality
Bit resolution defines the smallest measurable change in a signal.
A higher bit resolution improves dynamic range, allowing DAQ systems to capture both weak and strong signals simultaneously.
- 12-bit DAQ (~4,096 discrete levels) – Suitable for basic logging applications
- 16-bit DAQ (~65,536 discrete levels) – Ideal for mid-range applications
- 24-bit DAQ (~16 million discrete levels) – Best for high-precision measurements in vibration, sound, and scientific research
Accuracy & Dynamic Range Considerations
For precision applications, the dynamic range (measured in dB) should be high enough to capture small fluctuations without signal distortion. A range of 100-160 dB ensures clear and detailed signal acquisition, especially in acoustic, RF, and structural testing environments.
Real-Time Data Processing vs. Logged Data
- Real-Time DAQ: Best for immediate monitoring, automation, and control systems where instant feedback is needed.
- Data Logging DAQ: Designed for long-term data storage, allowing post-event analysis for quality control, environmental monitoring, and predictive maintenance.
Curious about our pricing?
Click here to find out more.
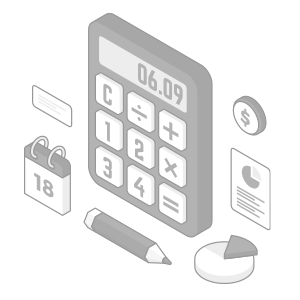
Data Filtering, Noise Reduction, and Signal Isolation
Noise affects measurement accuracy, requiring filters to remove unwanted frequencies:
- Low-Pass Filters: Remove high-frequency noise
- High-Pass Filters: Eliminate low-frequency drift
- Band-Pass Filters: Capture only the frequency range of interest
DAQ Software Considerations
DAQ hardware is only as good as its software interface. When evaluating software, consider:
- User-friendly UI (intuitive dashboard, simple configuration)
- Compatibility (Windows, Linux, cloud platforms)
- Real-time visualization (graphing, FFT analysis, live data streaming)
- API and SDK support (for Python, MATLAB, LabVIEW)
Power & Portability: Choosing the Right Form Factor
DAQ Power Needs & Energy Efficiency
- Battery-Powered DAQs: Ideal for field use and remote data logging
- AC/DC-Powered DAQs: Best for lab and industrial applications requiring high-speed data capture
Portability & Environmental Considerations
- Handheld & Compact DAQs: Lightweight and mobile
- Benchtop & Rack-Mounted DAQs: Used for permanent installations in labs and factories
- IP67 Waterproof & Rugged DAQs: Built for harsh industrial environments
- Remote Coverage: Ability to monitor sensors in different locations. Up to 100 m (32.8′) in distance!
-
1Environment-resistant remote unit
-
2Master unit
-
3Sensor wiring distance: 2 m (6.6′)
We’re here to provide you with more details.
Reach out today!
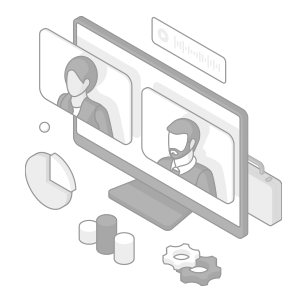
Choosing Between DAQ Brands: Key Factors to Consider
Brand Reputation & Warranty Policies
- Long-term reliability and industry recognition
- Comprehensive warranty coverage
Availability of Customer & Technical Support
- 24/7 technical assistance
- On-site calibration and repair services
KEYENCE offers advanced data loggers designed for high-precision data acquisition. Explore our NR-500 and NR-X models for industry-leading performance. Speak with an expert for personalized guidance on the best DAQ system for you.
Contact us to learn more about how our advanced technology can help take your business to the next level.
Contact Us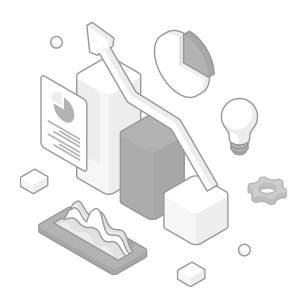