Data Acquisition (DAQ)
What is Condition Monitoring? A Guide to Predictive Maintenance
-
Tags:
- Current , Data Acquisition , Voltage
Condition monitoring is the process of proactively maintaining a specific device or machinery to detect changes and identify potential issues that may indicate an impending fault. It also involves a maintenance strategy focused on the conditions of the machinery, aimed at preventing faults from deviating from the norm; in short, it encompasses predictive maintenance.
Understanding Condition Monitoring: How It Works and Why It Matters
Traditionally, predicting machinery performance involves engineers manually inspecting machines to assess their operational output based on sounds and vibration. This process has evolved over time with digital technology, leading to advanced maintenance techniques that preempt machine breakdowns. We also make use of other process sensors measuring temperature, flow rate, voltage, etc.
With modern technology, condition monitoring has become easier and faster. Working with KEYENCE can make your process seamless and cost-effective. You can schedule predictive maintenance at regular intervals, such as every three or six months.
Rather than running your industrial machine to the ground and facing costly repairs or replacements, you can effectively use condition monitoring to predict potential failures. For this, KEYENCE measurement DAQ can be used for a wide range of measurements, from simple to complex multi-aspect, multi-channel measurements.
How Does It Work?
Condition monitoring is categorized into three steps:
1. Installation of Monitoring Systems: This is the first step for you to have proper condition monitoring. It involves installing the monitoring system hardware into your serviceable machinery. This may require you to customize or modify your existing serviceable equipment based on your requirements.
2. Data Management: Also known as Baseline Data Management, once your monitoring system is installed in the serviceable equipment, you can proceed to measure the equipment’s performance. The data collected using systems like the DAQ NR-500 will then be managed to accurately predict the performance of your machinery. The data may include vibration monitoring data, rotor speed data, temperature data, processing sensor data, and many others. Subsequently, this will help you monitor the condition of your equipment moving forward.
3. Regular Tracking: After installing the monitor and now collecting data, the next step is to use sensor and condition monitoring software to evaluate performance and provide a diagnosis of your equipment. This can be accomplished easily using the free KEYENCE Wave Logger Software.
In cases of abnormality in the performance of the equipment, the system will detect it and send out an alert. The alert may be for immediate actions to be carried out, or it will let you know if the machine can keep operating.
Get detailed information on our products by downloading our catalog.
View Catalog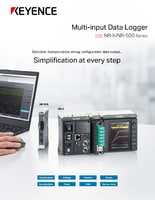
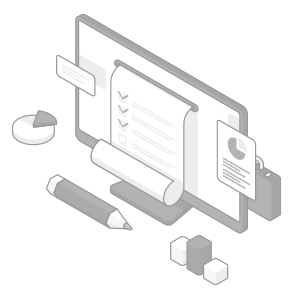
Condition Monitoring: Key Components and Benefits
The key components of condition monitoring are:
- Sensors: These devices are installed on equipment to measure the various parameters or elements such as vibration, temperature, current, voltage, etc.
- Data Acquisition System (DAQ): This is the software that collects all data and software for your baseline management, such as the Data Logger NR-X.
- Data Analysis: Advanced software or algorithms that will analyze the data collected and stored in the DAQ. It identifies the patterns, trends, or inconsistencies in the equipment to predict potential faults. The KEYENCE Wave Logger Software can be used for example.
- Decision-Making Team: Based on the analysis, maintenance teams like KEYENCE can help you analyze the data and help you schedule preventive measures.
The benefits of condition monitoring are but not limited to:
- Reduced risk of downtime
- Cost-savings
- Increased equipment lifespan
- Accurate decision-making through data collected
- Reliability and improvement
How Vibration Condition Monitoring Enhances Predictive Maintenance
Vibration condition monitoring is a technique within the frame of predictive maintenance that focuses on measuring the vibration produced by the machinery. It involves detecting and interpreting the patterns in vibration to identify potential faults. Vibration condition monitoring helps predictive monitoring by reducing the downtime of the machine. If vibrations can be monitored accurately, then any change in the pattern helps analyze or narrow the problem.
We’re here to provide you with more details.
Reach out today!
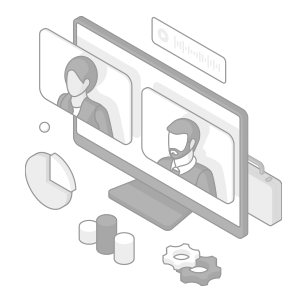
Exploring the Role of Sensors in Machine Condition Monitoring
Sensors are crucial to a machine's condition monitoring, as they provide real data to ensure the accurate detection of abnormalities and potential faults, improving your maintenance monitoring process. Without sensors, the data collected may be widely inaccurate.
Condition Monitoring Types
There are several types of condition monitoring:
- Oil Analysis: Similar to testing blood samples in the hospital, monitoring oil can reveal internal functions and accurately predict potential issues with the machine.
- Vibration Analysis: Machine condition monitoring can be done by monitoring the machine's vibrations. Detecting patterns and trends will accurately help you foresee any anomaly. It is also the oldest and most common form of condition monitoring.
- Electromagnetic Measurements: This involves monitoring a machine by measuring its magnetic fields.
- Temperature Monitoring: This monitors a machine's performance and foreseeable faults by analyzing its temperature.
Other types fall into categories like pressure monitoring, humidity monitoring, thermography, ultrasonic, and so forth.
Discover more about this product.
Click here to book your demo.
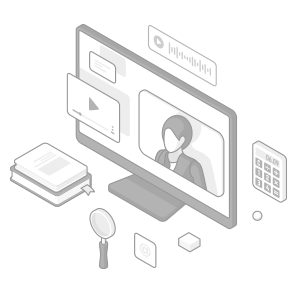
Condition Monitoring Applications
The application of condition monitoring can vary by industry and machinery. It can be used in all forms of manufacturing equipment to assess performance and efficiency, aiming to prevent unplanned breakdowns or rundowns.
Condition monitoring techniques have also been applied to aircraft, vehicles, wind turbine machinery, train door vibrations and various other equipment.
Condition Monitoring Advantages
Industries are continually searching for ways to sustain the infrastructure and longevity of machines while cutting down on the cost of repair and replacement. Some of the advantages of condition monitoring are:
- Reduces downtime and helps you maximize production
- The safety of machines is increased
- Cost-effective
- Machine lifespan is increased
Conclusion
Condition monitoring is a proven and reliable way to improve equipment and also increase productivity. However, for an effective maintenance routine, be sure to schedule the process adequately with the right team, and you will get the right result.
Looking to improve your data acquisition system? Visit our website to learn more about our products and how they can benefit your business today!
Contact us to learn more about how our advanced technology can help take your business to the next level.
Contact Us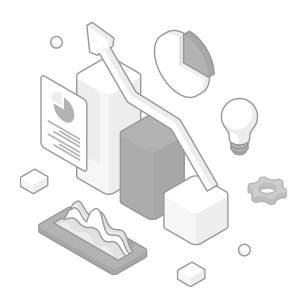